Make Allies and Win Together
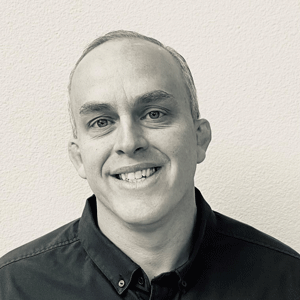
Landon Boucher is the director of business design and innovations at MiTek Inc.
Off-Site Construction is a term that has become a bit of a buzzword (that’s putting it mildly). Everyone these days, seems to tout the same exasperated (albeit valid) talking points about being built in a factory-controlled environment, improved processes, sustainability, reduced on-site build cycle, labor etc.
What many fail to mention, unfortunately, is that none of this matters if we have the wrong people managing it all. It is not just about process or product. It’s about people. All three are needed to make building successful.
Too often, those of us in the off-site construction sector dismiss the incredible accomplishments of our on-site construction counterparts and the tradesmen and women that are the workforce behind this industry. It’s inaccurate to claim that not much has changed in the last 100 years in the way we build homes. The list of what has changed in the last 20 years alone is too long for this post. What has always amazed me about construction is the people. The people who build our homes, our communities, our world. It is the people who have developed improved processes and products and it is the people who must be relied upon to utilize them efficiently. Like all things with people, sometimes we do it well and sometimes we don’t. This reality exists just as much in off-site construction. I have seen many projects delayed, factories failed, and processes not followed. Every single time, I can point to the people as the key factor in derailing otherwise well thought out plans.
I do believe off-site construction can be the better solution. All things being equal (i.e., good process, product, and people), I believe off-site teams will outperform on-site teams every time. But we need to be honest with ourselves and our industry by acknowledging that many times things are not equal. I think we do a disservice to the advancement of off-site construction when we fail to recognize (and furthermore, proclaim) this truth.
In lieu of making claims about how “traditional construction” is outdated, slow, and prone to problems, how about we work together, create allies, and foster a relationship of collaboration? I see a lot of posts on social media and in industry presentations that contain side-by-side comparisons of off-site and on-site construction. One photo is a messy and disorganized project and the other is a clean, well-managed depiction of just-in-time delivery methods utilizing mods or panels. I don’t ever see anyone share the failures of their own respective side of this equation. As a consultant for many years to contractors, engineers, and manufacturers, I’ve seen the failures and successes of both. I’ve seen them up close. Some I’ve even been responsible for, at least on some level.
It is my hope that we will see further progress in continuous improvement of construction by letting down our guards and engaging in collaborative efforts where we can share best practices and lessons learned based on our own direct experiences. A rising tide will raise all ships.
Let’s be authentic in our communications and win together.
More from Modular Advantage
Oregon’s Prevailing Wage Proposal: A Wake-Up Call for Modular Construction
Should House Bill 2688A become law, building projects would increase in price, face longer completion timelines, and produce significantly more waste. The bill also incentivizes contract awards to out of state businesses who would not reinvest their earnings into the local Oregon economy.
Behind the Design of Bethany Senior Terraces, NYC’s First Modular Passive House Senior Housing Project
As more developers seek to meet new regulations for energy efficiency, the team at Murray Engineering has set a new record. With the Bethany Senior Terraces project, Murray Engineering has helped to develop NYC’s first modular structure that fully encompasses passive house principles — introducing a new era of energy efficiency in the energy-conscious city that never sleeps.
How LAMOD is Using Modular to Address Inefficiency, Sustainability, and the Future of Construction
As developers, designers, and contractors seek to understand the evolving needs of the modular industry, no one is as well-versed in the benefits of going modular as Mārcis Kreičmanis. As the co-founder and CBDO of LAMOD in Riga, Latvia, Mārcis has made it his ultimate goal to address the inefficiencies of traditional construction.
From Furniture Builder to ‘Activist Architect’: Stuart Emmons’ Unique Journey
Stuart Emmons was fascinated by buildings at a young age. He remembers building sand cities with his brother during trips to the Jersey shore. His father gave him his first drawing table at the age of ten. Today, he is an experienced architect who received his FAIA in June 2025. The road he took is unique, to say the least.
Forge Craft Architecture + Design: Codes, Contracts, and Intellectual Property
Founding Principal and Director of Modular Practice for Forge Craft Architecture + Design, Rommel Sulit, discusses the implications of codes, contracts, and intellectual property on
modular construction.
Eisa Lee, the “Bilingual” Architect
Now as the founder of XL
Architecture and Modular Design in Ontario, Canada, she applies not just her education as a traditional architect but an entire holistic view on modular design. It’s this expansive view that guides her work on being a true partner that bridges the gap between architects and modular factories as they collaborate on the design process.
Tamarack Grove Engineering: Designing for the Modular Sector
The role of a structural engineer is crucial to the success of a modular project, from initial analysis to construction administration. Tamarack Grove offers structural engineering services — project analysis, plan creation, design creation, and construction administration — for commercial, manufacturing, facilities, public services, and modular. Modular is only one market sector the company serves but it is an increasingly popular one.
Engineer Masters the Art of Listening to His Customers
Since founding Modular Structural Consultants, LLC. in 2014, Yurianto has established a steady following of modular and container-based construction clients, primarily manufacturers. His services often include providing engineering calculations, reviewing drawings, and engineering certification
Inside College Road: Engineering the Modules of One of the World’s Tallest Modular Buildings
College Road is a groundbreaking modular residential development in East Croydon, South London by offsite developer and contractor, Tide, its modular company Vision Volumetric (VV), and engineered by MJH Structural Engineers.
Design for Flow: The Overlooked Power of DfMA in Modular Construction
Unlocking higher throughput, lower costs, and fewer redesigns by aligning Lean production flow with design for manufacturing and assembly.