Linc Moss: A Career in Modular Construction
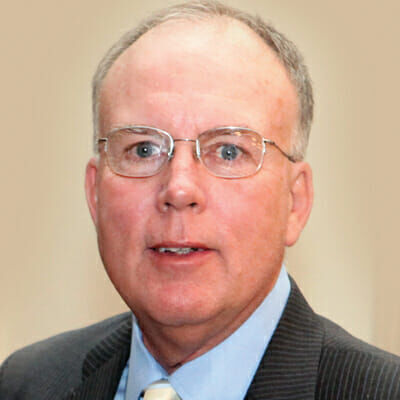
Linc Moss served as president and board chair of the Mobile Modular Office Association from 1987 to 1988, and then served again as president of the Modular Building Institute from 1999-2000.
Linc Moss worked in the modular construction industry for nearly 45 years and served as a Board Member and twice as President of the MMOA/MBI before retiring at the close of 2020.
Several veterans of the modular construction industry can look back with pride at their contributions over the years, and none more so than Linc Moss.
A Lucky Break
Sometimes a challenge is really a door to a new opportunity—a lucky break. For young Linc Moss in the mid-1970s, that was the case. Facing a shortage of funds to continue his college education, he took a job with Holiday Rambler in northern Indiana with the aim of replenishing his bank account.
“I was going to take a year off and put together the funds to go back to school…and on the job application I put down that I had mechanical drafting in high school,” Moss said. “And next thing I know the VP of HR comes out and talks to me and two days later, I’m sitting at a drafting board wearing a shirt and tie and thinking, you know, this is kind of a slick gig.”
That lucky break was soon followed by another. A friend informed him that Cliff Industries had landed a substantial project and opportunities were there for the taking.
“Cliff Industries had taken on this monster project with Aramco (Arabian-American Oil Company) that essentially required 80+ hour weeks from the design group to keep up with it,” Moss noted. “So I went over there and my first taste of commercial modular construction were 6-1/2-day work weeks, with a typical day ranging from 10 to 12 hours a day. This schedule went on for over 6 months.
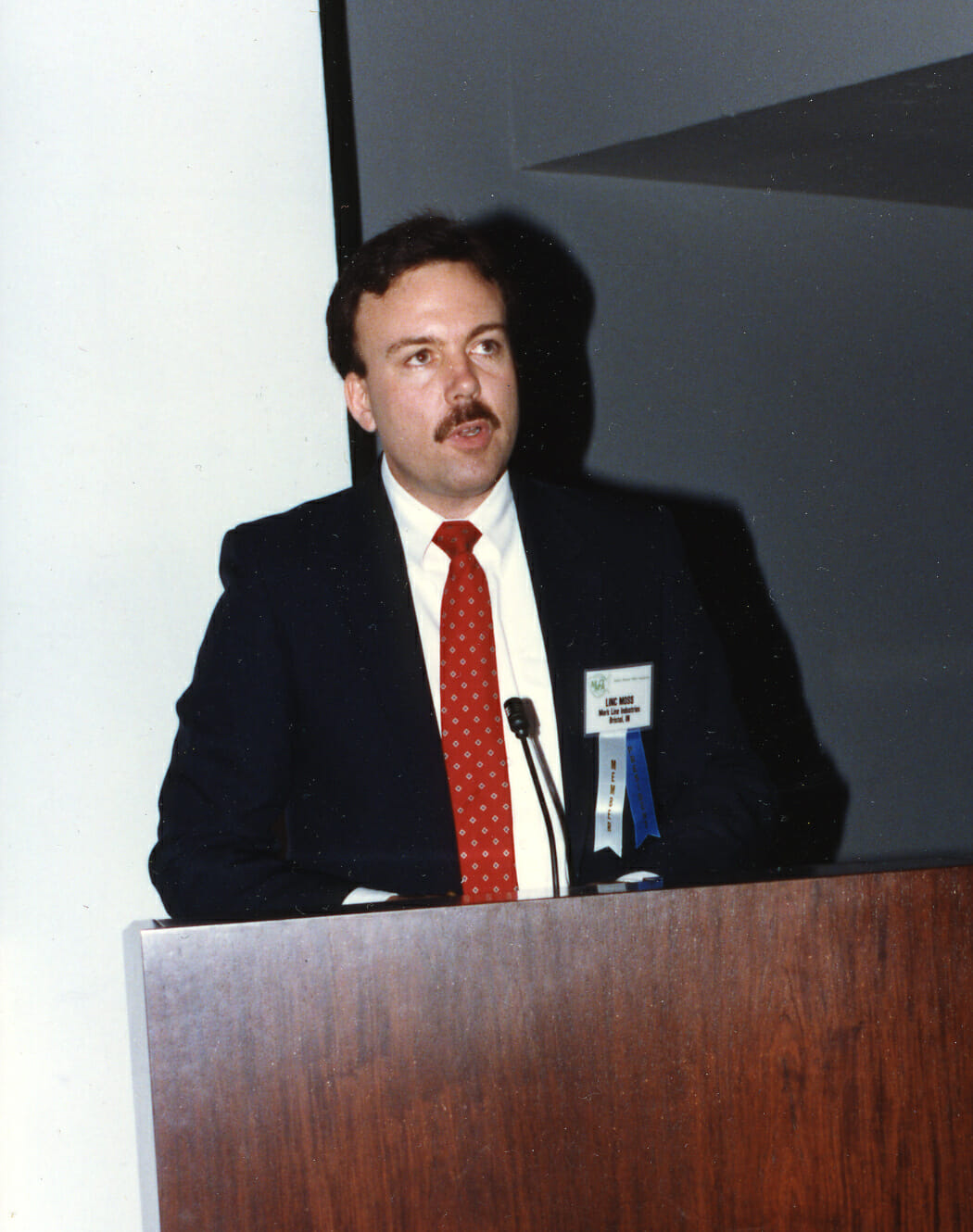
Linc Moss addresses attendees at the 1987 MMOA annual convention and tradeshow.
That Aramco project introduced Moss to modular construction in the form of “knock-down” buildings for the oil fields. “Nowadays, they call them flat packs, where it’s panelized construction and you just build a floor and then you collapse all the walls on top of it, stack it, and then put the roof on top of that,” he said. “Take it out to the job site, take a crane, pick the roof up, stand walls up, set the roof back on it, then you’ve got a 3D structure.”
Moss worked at Cliff Industries from 1976-1983 and learned several roles in working in the modular construction industry. “Cliff was a publicly traded company. We had plants in Idaho, Texas, Indiana, Pennsylvania, and Georgia at the time,” he noted. Employees in the engineering department typically moved from role to role to develop comprehensive knowledge about the business.
“The president of the company viewed the engineering department essentially as “‘princes in waiting.” We were being groomed,” Moss said, “and he firmly believed that if you knew how to design them, then you knew how to price them. If you knew how to price them, you knew how to sell them. And if you knew how to sell them, you knew how to build them.”
Engineering employees would typically work in estimating and in production for a time. “So that was the route I found myself on,” he added. “I worked in estimating and then ended up transferring to Texas and building a new manufacturing plant in Fort Worth, and then being the general manager of it for several years, before the company went under,” Moss said.
From Cliff Industries, Moss moved on to Markline Industries, staying from 1983-1991. Markline was also, Moss said, a wholesale manufacturer of modular structures. He was part of the team that built several new Markline factories in Pennsylvania and grew the business in the Northeast US.
After that stint at Markline, Moss transitioned to Ramtech Building Systems, which he described as a design-build firm utilizing modular construction. “The industry was evolving, and a whole new segment of integrated builders (providing design-manufacturing and field construction services) were coming up.” He started as their Director of Technical Services, responsible for estimating and project management, then, “I ran the construction department and ended up being Chief Operating Officer there, taking over the reins to the manufacturing plant, as well as the field operations.”
The penultimate step was serving as President starting in 2011, a post he held until 2019. During the last two years before his retirement in 2020, Moss acted primarily in a training role. First for Ramtech’s new President, Matt Slataper, then for Ramtech’s next COO, Randy Van Zandt.
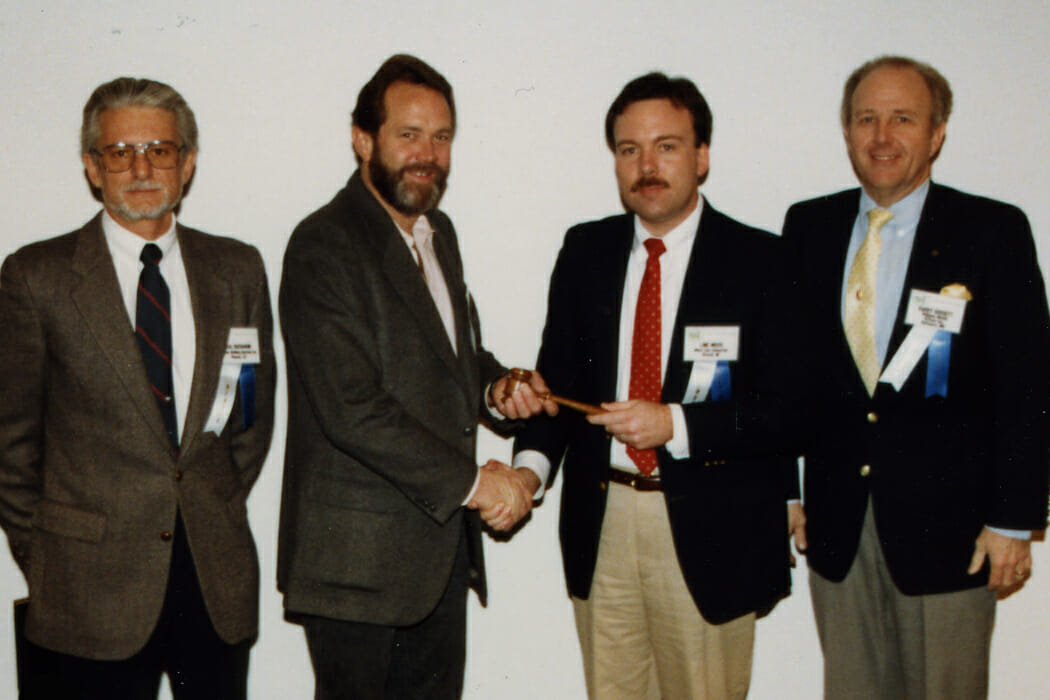
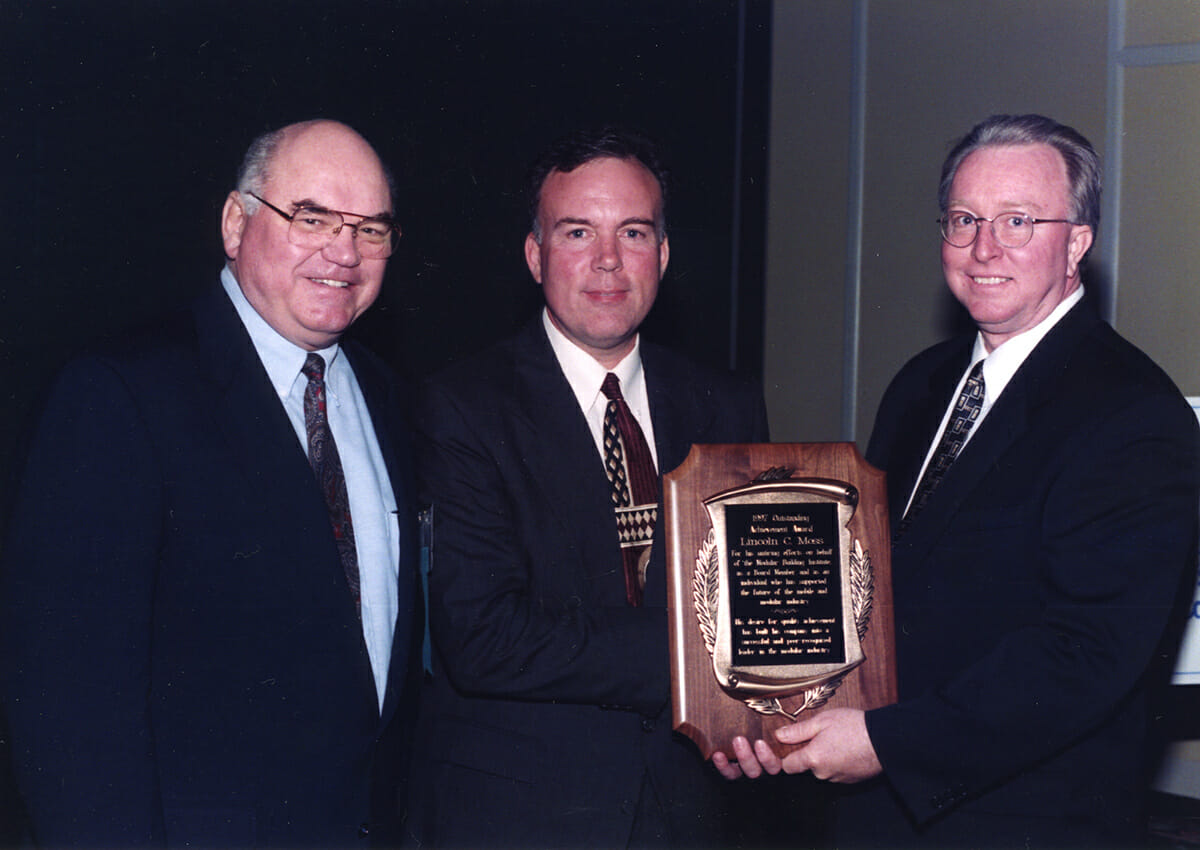
Joining the MMOA
Not long after starting in the modular construction industry, Moss found himself assuming a leadership role in the fledgling association created to represent the industry (Mobile Modular Office Association). In 1984, while working for Markline Industries, Moss was invited to attend a meeting in Palm Springs, California. At the meeting, he was invited to join the board of directors, and accepted.
“We had a fairly limited talent pool,” he said. “The reason I say it was limited, were the people that bought into promoting a national trade association, at that time was a fairly small number. Up to that point, the early 1980s, this whole industry, being an offspring of mobile homes, was very entrepreneurial.
There were many owners that were very guarded with what they wanted to share, as far as best practices in the factory and field, project processes, and design practices. In the earliest years of the Association, this “keep it close to the vest” mentality stunted some of our ability to deliver true educational value to our members.”
While in a board role, Moss was part of developing the Awards of Distinction for the organization. Those awards, he said, were born of a central goal: gaining visibility. At the time, Moss said, “The majority of the product we produced was essentially just construction field offices in support of the construction industry. Your biggest customer, if you were a leasing company, were ERN Top 500 Contractors. “Basically, we were just building construction field offices to support someone else’s project. A home run would be a huge project where they might put together a 5000-6000-square foot complex for a field office at a job site. As an industry, we needed to figure out how to make modular construction the prime project and not continue to act in a supporting role for other contractors producing the prime project.”
Firms in modular construction, “were doing some pretty neat things in those days,” Moss noted, and the association was eager to publicize their efforts in order to advance the industry as a whole. “Anything we could do to showcase modular construction, beyond being a rental office to a construction company, was our primary goal,” he said.
Moss assumed the role of Association President in 1987, and worked to continue the momentum of the MMOA. “We had approximately 100 members; all were in the continental United States. Once again, marketing of commercial modular buildings was our primary mission in those days.”
In addition, Moss said, rules and regulations affecting modular construction were a challenge for the industry and the association. “In those days, there wasn’t an International Building Code that was universally accepted. More of a problem was the lack of uniform rules and regulations on the administration of the codes at the state level. Most states did not utilize third parties for review. Every state was different, for example, in those days, it wasn’t uncommon for New Jersey to have a three- to four-month backlog just on review of the plans for approval, which killed one
of modular construction’s strongest selling points: speed. So, we were doing everything in our power to form some sort of interstate compact that would be universally accepted. Since we were dealing with individual state agencies and state employees, this proved to be a nearly impossible task.”
Notable Projects
In a career of more than 40 years, Moss certainly faced some interesting professional challenges. Delivering modular buildings for a Combat Aviation Brigade-Battalion headquarters to Fort Bliss, located in El Paso, Texas, stands out, according to Moss.
“Ramtech was the only commercial modular company, in the nation, to be awarded an IDIQ contract from the Corps of Engineers. IDIQ is ‘indefinite delivery-indefinite quantity’, so essentially a master design-build contract.”
All told, the project was 126,000 square feet with 100 modules. The modules were placed side-to-side and end-to-end and stacked to two stories. The facility housed a “specialized compartmented information facility,” or “SCIF”, which secured the most sensitive information. SCIFs also demand studio-like sound deadening in walls, floors and ceiling, as well as extensive electronic shielding. It was an incredibly detailed and sophisticated project, he said.
That wasn’t the only highly sensitive government project for Moss, however. Los Alamos National Laboratory (LANL), located at Los Alamos, New Mexico and best known for its role in the Manhattan Project, required multiple two-story buildings, which Ramtech produced. Getting those structures on site, clearly, was a different type of project from the norm. “Most areas at LANL are ultra-sensitive and require armed security forces present during any construction activity,” Moss said.
The Modular Building Institute Years
In 1999, Moss assumed the role of Association President for a second time. By that time a seasoned industry leader, Moss said the industry was gaining recognition from the design community, as well as owners and some contractors. MBI was coming into its own as the recognized voice of the commercial modular industry, a new website was up and running, and plans were in place for the launch of the MBI Education Foundation. The Association was truly beginning to make a difference. “I was honored and gratified that MBI’s leadership asked me to assume the Presidency for a second term.”
The Finale
After decades around the MBI, Moss cites a familiar theme for his favorite memories. “Far and away the best has been the networking, developing friendships over the years, and sharing best practices,” he said. “Being able to share knowledge” was a key impetus for MBI’s growth, as well as the modular construction industry to grow into the thriving
sector it is today.
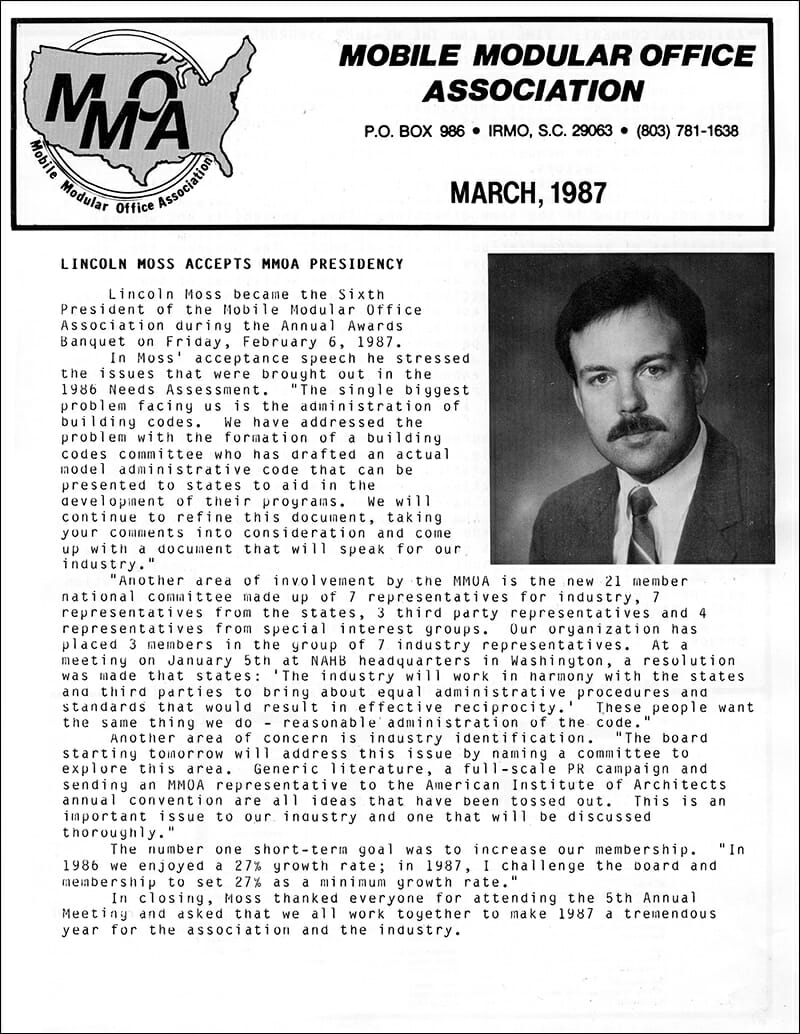
Linc Moss was announced as MMOA president in March 1987.
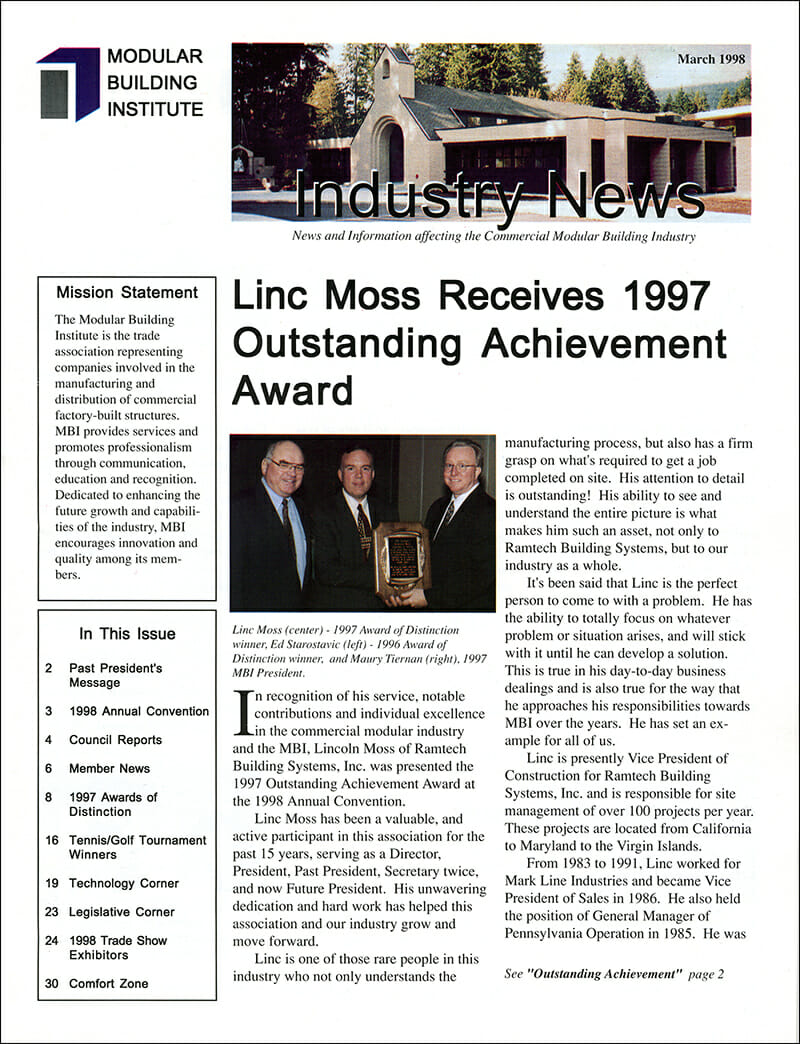
Linc Moss was awarded MBI's Outstanding Achievement Award in March 1998.
The modular construction industry is well positioned to thrive in the coming decades, as well, thanks to the efforts of Linc Moss and others over the last few decades. For those starting fresh in modular construction now, and even those with some experience, Moss offers a clear view of how to proceed:
“Don’t look at what’s already been done and think that’s where the limits are. High-rise modular buildings that were once thought an impossibility are now the norm. As trite as it sounds, ‘think outside the box.’”
About the Author: Steve Hansen is a Colorado-based writer with a focus on the built environment—architecture, construction, renewable energy, and transportation. He can be reached on LinkedIn.
More from Modular Advantage
Oregon’s Prevailing Wage Proposal: A Wake-Up Call for Modular Construction
In early February, 2024, the Massachusetts Board of Building Regulations and Standards (BBRS) released its proposed 10th Edition building codes. This draft included several amendments targeting modular construction that would have created an extremely difficult environment for the entire modular industry and could have eliminated the industry entirely in the state.
Behind the Design of Bethany Senior Terraces, NYC’s First Modular Passive House Senior Housing Project
As more developers seek to meet new regulations for energy efficiency, the team at Murray Engineering has set a new record. With the Bethany Senior Terraces project, Murray Engineering has helped to develop NYC’s first modular structure that fully encompasses passive house principles — introducing a new era of energy efficiency in the energy-conscious city that never sleeps.
How LAMOD is Using Modular to Address Inefficiency, Sustainability, and the Future of Construction
As developers, designers, and contractors seek to understand the evolving needs of the modular industry, no one is as well-versed in the benefits of going modular as Mārcis Kreičmanis. As the co-founder and CBDO of LAMOD in Riga, Latvia, Mārcis has made it his ultimate goal to address the inefficiencies of traditional construction.
From Furniture Builder to ‘Activist Architect’: Stuart Emmons’ Unique Journey
Stuart Emmons was fascinated by buildings at a young age. He remembers building sand cities with his brother during trips to the Jersey shore. His father gave him his first drawing table at the age of ten. Today, he is an experienced architect who received his FAIA in June 2025. The road he took is unique, to say the least.
Forge Craft Architecture + Design: Codes, Contracts, and Intellectual Property
Founding Principal and Director of Modular Practice for Forge Craft Architecture + Design, Rommel Sulit, discusses the implications of codes, contracts, and intellectual property on
modular construction.
Eisa Lee, the “Bilingual” Architect
Now as the founder of XL
Architecture and Modular Design in Ontario, Canada, she applies not just her education as a traditional architect but an entire holistic view on modular design. It’s this expansive view that guides her work on being a true partner that bridges the gap between architects and modular factories as they collaborate on the design process.
Tamarack Grove Engineering: Designing for the Modular Sector
The role of a structural engineer is crucial to the success of a modular project, from initial analysis to construction administration. Tamarack Grove offers structural engineering services — project analysis, plan creation, design creation, and construction administration — for commercial, manufacturing, facilities, public services, and modular. Modular is only one market sector the company serves but it is an increasingly popular one.
Engineer Masters the Art of Listening to His Customers
Since founding Modular Structural Consultants, LLC. in 2014, Yurianto has established a steady following of modular and container-based construction clients, primarily manufacturers. His services often include providing engineering calculations, reviewing drawings, and engineering certification
Inside College Road: Engineering the Modules of One of the World’s Tallest Modular Buildings
College Road is a groundbreaking modular residential development in East Croydon, South London by offsite developer and contractor, Tide, its modular company Vision Volumetric (VV), and engineered by MJH Structural Engineers.
Design for Flow: The Overlooked Power of DfMA in Modular Construction
Unlocking higher throughput, lower costs, and fewer redesigns by aligning Lean production flow with design for manufacturing and assembly.