Laying the Foundation of the Modular Building Institute
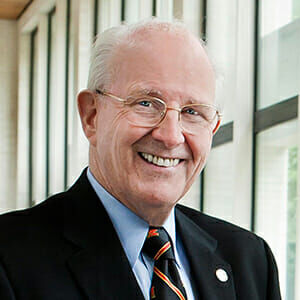
Barry Gossett is one of the founding members of the Mobile Modular Office Association, now known as the Modular Building Institute. In addition, his generosity led directly to the creation of the MBI Educational Foundation.
Trade associations, like anything else, aren’t borne from nothing. And the Modular Building Institute (MBI) was no exception.
Formally incorporated in 1983, the association that was to become MBI began in an Atlanta meeting room in 1982. Barry Gossett, then President of Williams Mobile Offices, was one of several regional dealers and manufactures in attendance who agreed to discuss the idea of forming a trade association.
“I recall the meeting was organized by Toni Sylvester,” said Gossett. “She who became our first Executive Director. She and her husband, Ted Hamre, operated Ace Mobile Offices in Irmo, SC, a dealer serving the southeast area.
“Toni had an association management background and Ted had sales experience. They wanted to get industry folks together to talk about the industry in general and some of the common problems everybody was facing. One issue in particular—one that still exists: code application, compliance, and enforcement—was a primary topic of discussion.
“I remember building codes because almost every time a unit was delivered a local building inspector would usually have negative remarks about the equipment, like ‘we don’t allow mobile homes here’ or similar statements. There was confusion about what building code applied to the use as a ‘temporary office’ as most equipment was being used on construction sites. Usually, the inspector would understand it was part of the equipment needed for the project and allow its temporary use, but it was always a challenge. Another issue was transportation of equipment as most units were 12’ wide and required ‘oversize load permits’ in some but not all jurisdictions.”
Other discussions came up as well, including those about the type of memberships to create. “We were dealers, manufacturers, and suppliers, so how would interactions be handled? Dealers were worried about manufactures going direct to customers and bypassing them. Suppliers voiced similar concerns. Competitive issues came up. Finally, we said, ‘Wait a minute, if this is to be an effective trade association there are some issues we can’t talk about. We must have a code of conduct.”
Price-fixing was one of the issues the group agreed to not discuss. “Still,” Gossett chuckled, “One of the manufacturers there kept asking, ‘Well, I want to know how I get paid. Can you give me a list of all these people that are deadbeats?’ And, of course, we couldn’t do that.”
An Association in Need of a Name
Another main discussion was what to call the association. Modular construction had been developing for years, but in the early 1980’s it was far from mainstream. Mobile office leasing, on the other hand, was doing well and the biggest source of revenue in the industry.
“Modular construction was very rudimentary compared to today’s products,” said Gossett. “In the early days we had double-wides; just putting two unit together, sometimes not even joined at the roof line. Often units were parked side by side, one forward the other backward with a platform in between.” Many folks said, ‘Modular buildings don’t make money but leasing and related setup fees do.’ So, after much discussion we settled on Mobile Modular Office Association.
“It was just majority rule,” Gossett said. “We didn’t hire a marketing firm to find the best name. We just voted and moved on.”
First Conventions
“I did not attend the first convention,” said Gossett, “but I was there when it was being planned. I remember a dealer from Lancaster, Ohio, Lloyd Helber and Bob Houchin from Cliff Industries—Bob was our first president—agreeing to set up the first convention.
“Honestly,” continued Gossett with a smile, “I think they just wanted to go to Las Vegas so the company could pay for the trip. Reports came back about the fun times and some business discussions among the 10 to 15 people who attended. In the end, the trips’ success could be measured by the relationships that were established and seeds planted for future conventions and industry growth.”
“The first MMOA convention I attended was in Kissimmee, Florida, in 1985,” recalled Gossett. “There were probably 40 to 50 attendees, including dealers, manufacturers, and suppliers. Williams Mobile Offices was a major sponsor. We purchased a 12’ x 60’ fully equipped mobile office from King’s Custom Builder to display on the hotel parking lot for all attendees and guests to visit. Invitations were sent to many Industry players asking they come to learn about the Association and discuss common industry issues. We had a good turnout and many new members joined.”
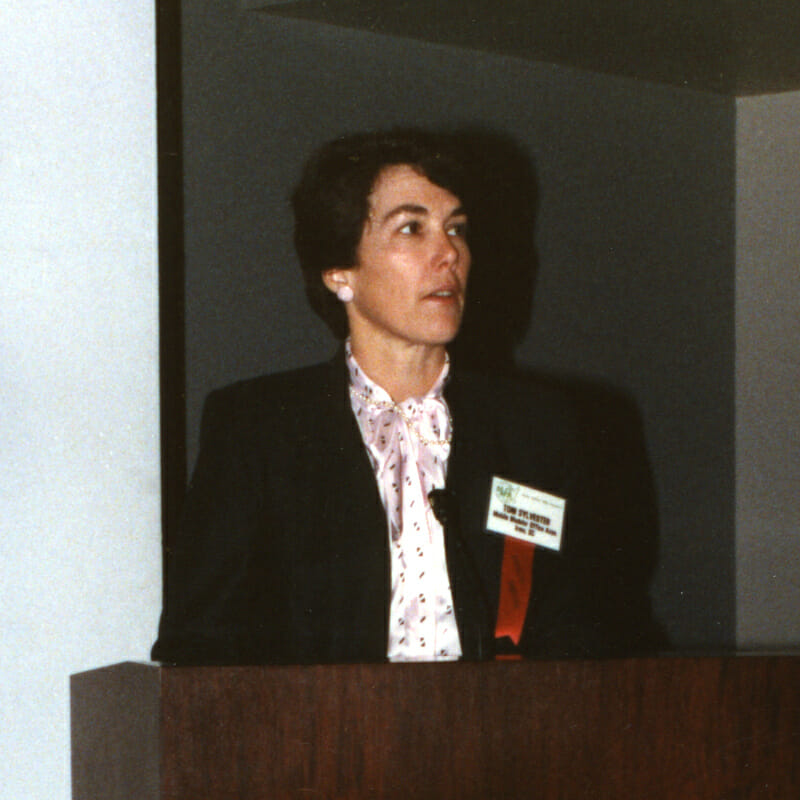
Toni Sylvester was the first executive director of the Mobile Modular Office Association.

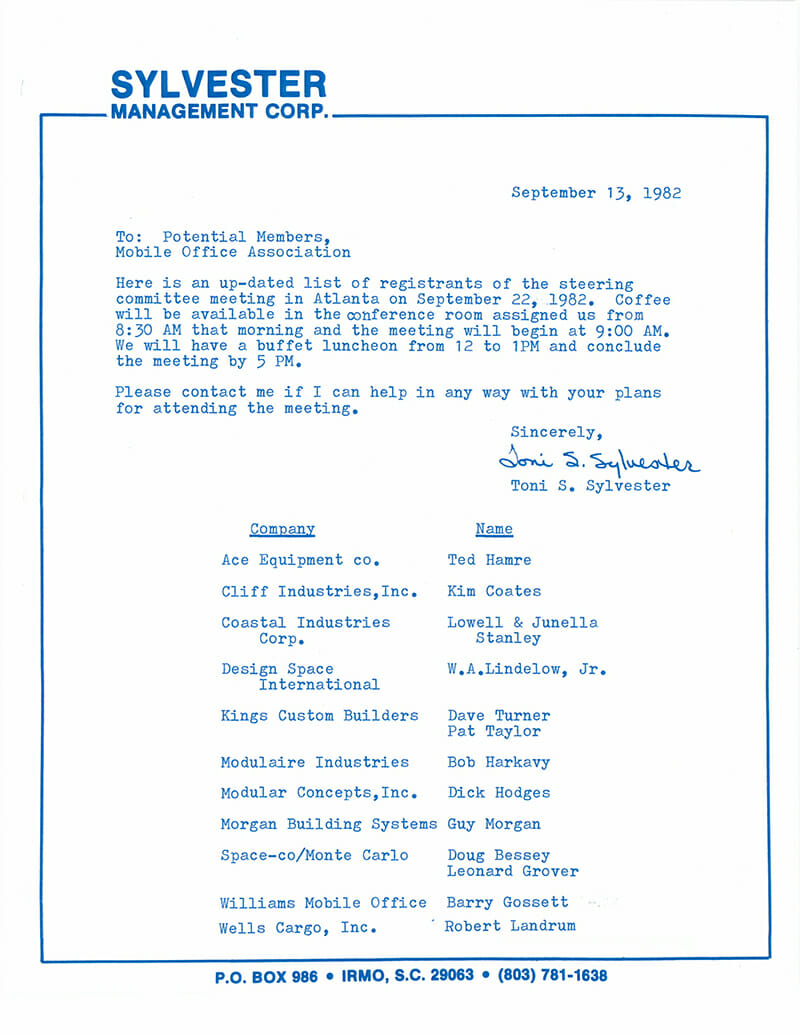
A listing of the attendees for the "Mobile Office Association's" first exploratory meeting.
Early Growth & Challenges
Based on the success of the Kissimmee convention and one’s that followed, the MMOA began to expand. “It grew,” said Gossett, “because people understood there was strength in numbers, especially when faced with the constant challenges of differing state and local regulations.”
Examples of those challenges were not hard to come by.
“I remember shipping units from our Indiana factory to Long Island,” stated Gossett. “Our customer, Grumman Aviation, required a multi-unit building and the direct route was through New York City, but we were literally stopped at the border. The police informed us we could only go through between 2:00am and 4:00am and needed their escort. Of course, we supplied “donuts and coffee money” to all those on escort duty.
“In fact,” continued Gossett, “once we were stopped and told we could not bring units into or through the city because the units did not meet the city’s electrical code.”
“As a trade association, we were able to discuss those type of issues with regulators, legislators, and others because MMOA represented the industry, not just individual companies, about issues affecting our customers and the public at-large. We wanted to resolve the issues by doing the right thing.”
Despite – or perhaps because of – these and similar challenges faced by the industry, MMOA continued to attract new member organizations and become a recognized nationwide voice of the industry. “It was exciting to get companies to join,” said Gossett. “Sometime in the mid-80’s we signed member number 100, Scotsman Manufacturing. (Williams merged with them in 1990.) Those were the milestones that were important. When could we get member number 150? 200? What segment of the industry would they come from? The more members, the stronger the association.”
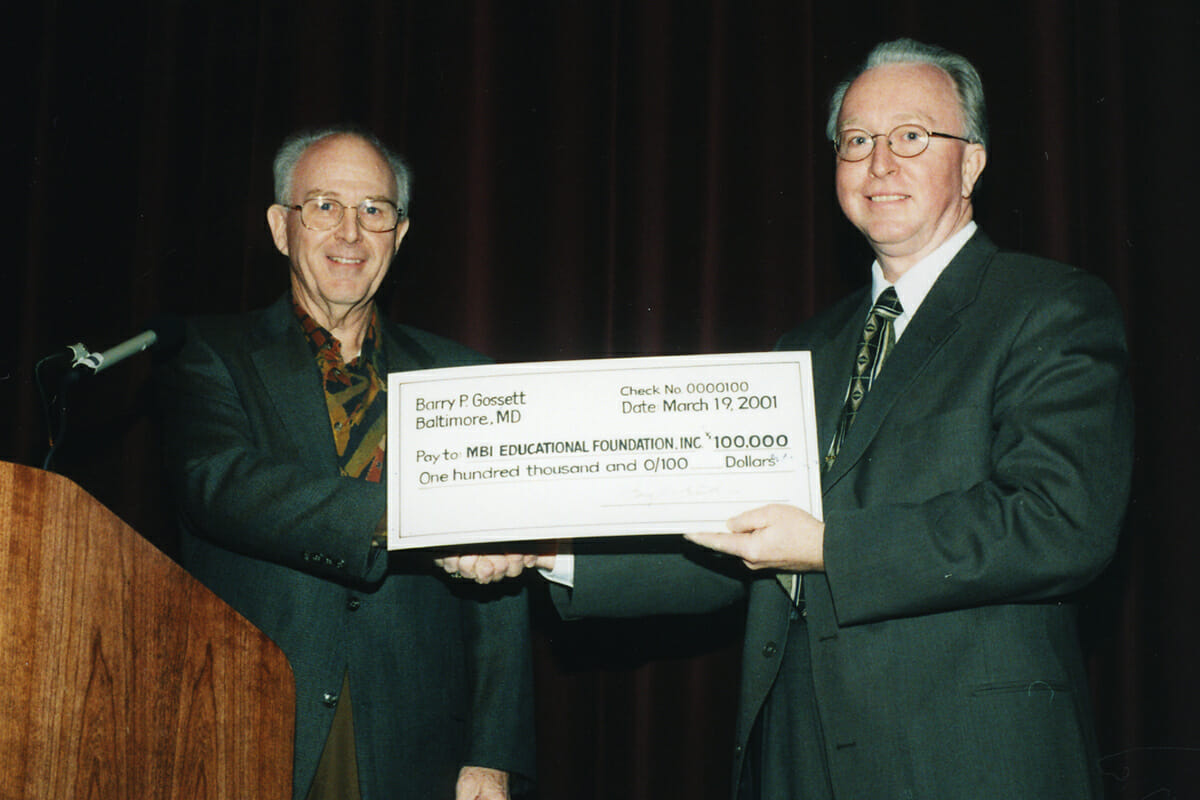
Barry Gossett (left) presents a check to establish the MBI Educational Foundation.
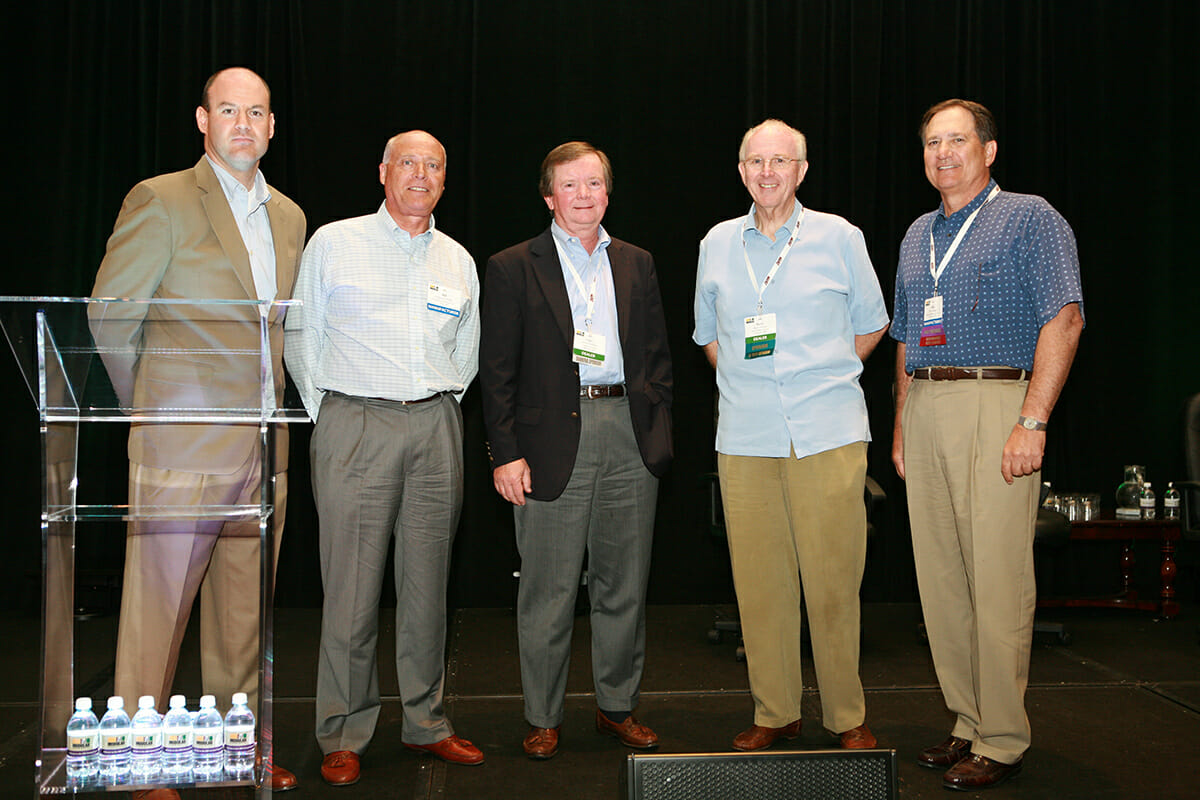
Barry Gossett (fourth from left) stands with then-newly-hired Tom Hardiman (left) and industry colleagues at one of MBI's annual convention and tradeshows.
Becoming MBI
The modular and relocatable buildings industry was evolving quickly in the late 80’s and early 90’s. Once single-unit leases accounted for a vast majority of the industry’s revenue, but now larger relocatable structures and permanent modular construction were starting to be recognized as a new and efficient way to provide commercial building space.
“I guess the excitement in those days was finding more and better uses for our products,” said Gossett. “We were graduating from suppling construction site trailers and moving to multi-unit buildings. Code-approved classrooms blossomed from coast to coast and larger modular buildings were being used by major corporations.”
Gossett then recalled an early project for Williams was a 20,000 sq. ft. building for IBM in Lexington, Kentucky. “After approval of the plans by IBM we were able to manufacture, transport and erect the building meeting the 90-day occupancy requirement. Quite a feat in those days!”
Not surprisingly, as the industry evolved, so too did the MMOA.
“Toni Sylvester left the industry and we hired Judy Smith as our new Executive Director,” recalled Gossett. “I think Toni served us the first 10 to 12 years then Judy for the next 8 years before Tom Hardiman became our Executive Director. Tom has taken the association to new levels of recognition and professionalism, hired a great staff, and leads an association that truly serves its members.
“At the same time,” Gossett continued, “modular buildings were becoming more widely accepted with improved design and marketing, and they were finally seen as more economical because of the time saved from design to occupancy. It was, ‘Oh, gosh, this doesn’t look like a trailer. Wait, it’s not a trailer, it’s a building.’”
Gossett mentioned one example from his own company. “In Williams’ case, we marketed our modular buildings as ‘concurrent construction’ since site work was being done at the same time buildings were manufactured in the factory. Delivery of the buildings was to a fully prepared site for final erection and occupancy.”
It was then time to address modular buildings, both permanent and relocatable, becoming the new standard and face of the industry. Should this be the association’s new direction? “As a senior (as in OLD) industry member,” laughed Gossett, “I encouraged change but urged everyone not to forget our roots, the money-making mobile office! Those buildings ushered in ‘modular’ as the new buzzword. There was a big change in the industry as permanent buildings became more popular.”
Looking Forward
In addition to MBI’s growing influence with code officials, regulators, and legislators, new initiatives were started to help grow not only the Association, but the modular construction industry at-large by focusing on leaders of the next generation.
“I’m really proud of the educational element of MBI’s mission,” said Gossett. “I know the MBI Foundations provide scholarships for students learning about the many parts of modular construction. In fact, some universities are involved as sponsors of classroom programs teaching about the industry.”
Gossett continued, “I finally got the University System of Maryland to become a member once they did their first permanent modular building. Now they’re believers, including modular construction along with conventional construction in their evaluation of building needs for the 12 University System. Time as well as cost is a major factor in their selection criteria. Going forward, the more we can provide opportunities for quality education about our industry, not just for participants, but for customers or potential users, the better off we’ll be.”
“You know” Gossett concluded, after a moment of reflection, “this is just a great industry.”
About the Author: John McMullen, PCM, is the marketing director for the Modular Building Institute. You can reach him directly at mcmullen@modular.org or on LinkedIn.
More from Modular Advantage
Oregon’s Prevailing Wage Proposal: A Wake-Up Call for Modular Construction
Should House Bill 2688A become law, building projects would increase in price, face longer completion timelines, and produce significantly more waste. The bill also incentivizes contract awards to out of state businesses who would not reinvest their earnings into the local Oregon economy.
Behind the Design of Bethany Senior Terraces, NYC’s First Modular Passive House Senior Housing Project
As more developers seek to meet new regulations for energy efficiency, the team at Murray Engineering has set a new record. With the Bethany Senior Terraces project, Murray Engineering has helped to develop NYC’s first modular structure that fully encompasses passive house principles — introducing a new era of energy efficiency in the energy-conscious city that never sleeps.
How LAMOD is Using Modular to Address Inefficiency, Sustainability, and the Future of Construction
As developers, designers, and contractors seek to understand the evolving needs of the modular industry, no one is as well-versed in the benefits of going modular as Mārcis Kreičmanis. As the co-founder and CBDO of LAMOD in Riga, Latvia, Mārcis has made it his ultimate goal to address the inefficiencies of traditional construction.
From Furniture Builder to ‘Activist Architect’: Stuart Emmons’ Unique Journey
Stuart Emmons was fascinated by buildings at a young age. He remembers building sand cities with his brother during trips to the Jersey shore. His father gave him his first drawing table at the age of ten. Today, he is an experienced architect who received his FAIA in June 2025. The road he took is unique, to say the least.
Forge Craft Architecture + Design: Codes, Contracts, and Intellectual Property
Founding Principal and Director of Modular Practice for Forge Craft Architecture + Design, Rommel Sulit, discusses the implications of codes, contracts, and intellectual property on
modular construction.
Eisa Lee, the “Bilingual” Architect
Now as the founder of XL
Architecture and Modular Design in Ontario, Canada, she applies not just her education as a traditional architect but an entire holistic view on modular design. It’s this expansive view that guides her work on being a true partner that bridges the gap between architects and modular factories as they collaborate on the design process.
Tamarack Grove Engineering: Designing for the Modular Sector
The role of a structural engineer is crucial to the success of a modular project, from initial analysis to construction administration. Tamarack Grove offers structural engineering services — project analysis, plan creation, design creation, and construction administration — for commercial, manufacturing, facilities, public services, and modular. Modular is only one market sector the company serves but it is an increasingly popular one.
Engineer Masters the Art of Listening to His Customers
Since founding Modular Structural Consultants, LLC. in 2014, Yurianto has established a steady following of modular and container-based construction clients, primarily manufacturers. His services often include providing engineering calculations, reviewing drawings, and engineering certification
Inside College Road: Engineering the Modules of One of the World’s Tallest Modular Buildings
College Road is a groundbreaking modular residential development in East Croydon, South London by offsite developer and contractor, Tide, its modular company Vision Volumetric (VV), and engineered by MJH Structural Engineers.
Design for Flow: The Overlooked Power of DfMA in Modular Construction
Unlocking higher throughput, lower costs, and fewer redesigns by aligning Lean production flow with design for manufacturing and assembly.