Modular Building is (Almost) as Old as the Hills
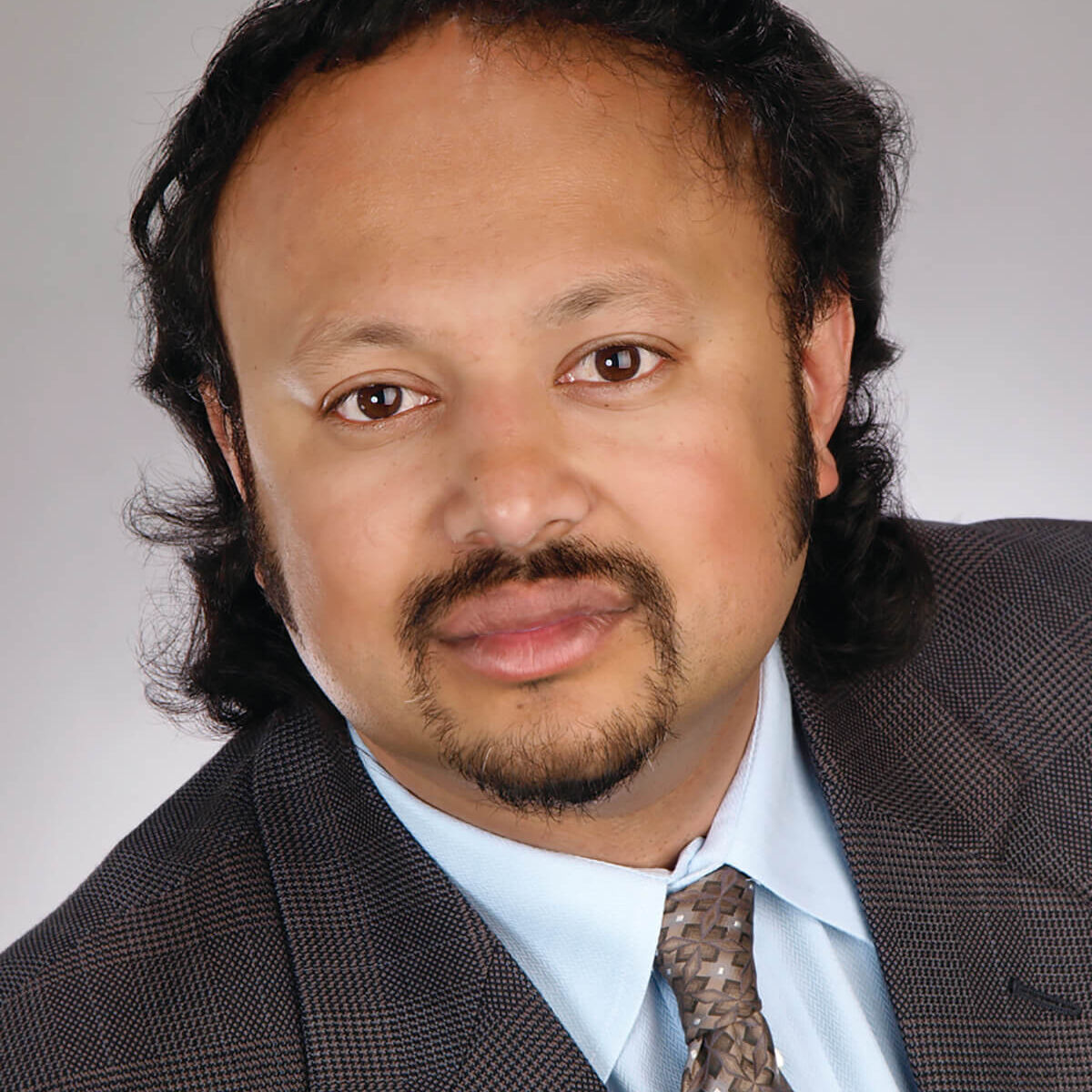
About the Author: Anirban Basu is the chairman & CEO of Sage Policy Group and chief economist of the Modular Building Institute.
Quite a History
Many view modular building as the emergent wave in construction. Controlled environments, precision manufacturing, and a highly trained workforce represent the cornerstones of the view that modular methods will continue to garner additional market share as time passes.
But despite its status as an upstart, modular building has been around for centuries. In ancient Rome, armies constructed forts in prefabricated sections.1 They brought those sections with them on their campaigns in order to facilitate easy setup in order to quickly secure newly conquered territory. The Romans are associated with many things, including philosophers, emperors, aqueducts, and stadia. Modular construction forms part of the list.
Fast forward to the 1600s. In Europe, settlers prebuilt homes and fishing houses to be transported as they moved to America. This practice was not unique to America, however. There are reports of structures being shipped from Britain to Australia.
While contemporary modular structures are far more capable than those used by Americans before there was a United States, the basic premise remains the same. By eliminating variables such as temperature and moisture, construction conducted in a controlled setting eliminates many risks, including premature deterioration of construction materials and delays in building as weather systems wreak havoc on conditions.
What is perhaps most remarkable is that, despite these advantages and the realization over the course of centuries that they exist, modular construction continues to be in its infancy from the perspective of construction market share. The industry has been striving for years to attain 5 percent market share in many categories, whether in office or healthcare construction.
In the U.S., Sears, Roebuck, and Co. brought the idea into the 20th century (literally) by offering pre-built homes in its catalog starting in 1908. The idea didn’t take off immediately, but following the Second World War, millions of veterans returned home ready to start a family. Pre-built homes emerged as a major contributor to the rapid spread of household formation and homeownership across the countryside.
Enter the history of Levittown. Starting in 1947, Abraham Levitt commenced work on one of four planned communities, the first of which was situated in Nassau County, Long Island. His son, Alfred, had returned from serving in the war.2 He urged his father to take advantage of a utilitarian approach to construction that had become popular in the U.S. Navy. Serving as chief architect for his father, he designed a simple one-floor home supplemented with an unfinished expansion attic. By the following year, they were producing about 30 houses per day, using materials from their own factories located around the country. The homes were popular. Residents quickly inhabited them. Eventually, the town was used as an archetype of the American Dream, bolstering the popularity of America’s suburbs in the process.
Over the last roughly four decades during which the Modular Building Institute has been in existence (founded 1983), prefabricated construction and modular building have expanded beyond one-floor homes in the suburbs. Today, virtually all major developers are incorporating some element of pre-built units or modules into their projects across both residential and nonresidential segments.
By the 1970s, office buildings, schools, and healthcare facilities were taking advantage of off-site construction to reduce costs and speed up delivery. Prefabrication/modular building has become increasingly popular in other parts of the world as well, including in Australia where such techniques are often used in school construction. The government there has forecasted that the number of students will expand by nearly 59 percent, or by 4 million students by 2051. To match demand to capacity, the government is predictably taking advantage of the development of modular classrooms. Much like modular homes, the classrooms are built off-site, which allows contractors to work around the year without being impacted by weather.
Labor Market Logic
It is well known that the principal challenge faced by many contractors relates to a scarcity of skilled construction workers. With Baby Boomers retiring in larger numbers and many members of the labor force, including younger ones, embracing remote work or gig jobs like driving for Lyft or Uber, shortfalls of skilled workers will plague construction for the foreseeable future.
What’s more, at-the-jobsite construction often requires the participation of local labor forces. But in booming communities like Austin, Nashville, Phoenix, Charlotte, Tampa, and elsewhere, the local labor forces are seldom able to keep up with demand. The competition between project owners to secure the efforts of general and subcontractors drives up costs of construction, which may be good for many contractors, but limits housing and other forms of affordability.
Modular building is fundamentally different. In this instance, construction activity can be divorced from where units will ultimately be delivered. This means that construction can take advantage of the national labor force as opposed to local ones. Moreover, manufacturing facilities serving construction can benefit from enormous economies of scale, reducing costs further as modular techniques continue to acquire construction market share. In short, modular building will likely help solve America’s construction worker shortfall, reducing costs and speeding construction delivery in the process.
This is hardly theoretical. An article published by Construction Dive in 2020 noted that Chick-fil-A, one of the nation’s most popular fast-food establishments, built a restaurant in Roswell, GA in three months using modular techniques. This was significantly faster than the typical 23-week build the chain routinely endures.
The company states that the modular approach “improved efficiency and time savings”, while allowing for “consistency and quality in the fast-food chain’s building across the country.” The article also notes that less waste is produced and that there is less disruption in the surrounding community, which helps to reinforce brand loyalty.
Prefabricated facilities can also limit exposure of harmful chemicals and minimize excess waste. As the world seeks to solve the problem of global warming and to improve public health outcomes, modular techniques represent part of the solution. In the final analysis, modular building has quite a history, but it has an even more spectacular future.
Endnotes
1 Gasc, Marco. “A Brief History on Modular Architecture”. GKV Architects.
2 Jackson, Kenneth T. “The Baby Boom and the Age of the Subdivision”. Ch. 13 from Crabgrass Frontier: The Suburbanization of the United States (New York: Oxford University Press, 1982), 231-245.
More from Modular Advantage
Oregon’s Prevailing Wage Proposal: A Wake-Up Call for Modular Construction
In early February, 2024, the Massachusetts Board of Building Regulations and Standards (BBRS) released its proposed 10th Edition building codes. This draft included several amendments targeting modular construction that would have created an extremely difficult environment for the entire modular industry and could have eliminated the industry entirely in the state.
Behind the Design of Bethany Senior Terraces, NYC’s First Modular Passive House Senior Housing Project
As more developers seek to meet new regulations for energy efficiency, the team at Murray Engineering has set a new record. With the Bethany Senior Terraces project, Murray Engineering has helped to develop NYC’s first modular structure that fully encompasses passive house principles — introducing a new era of energy efficiency in the energy-conscious city that never sleeps.
How LAMOD is Using Modular to Address Inefficiency, Sustainability, and the Future of Construction
As developers, designers, and contractors seek to understand the evolving needs of the modular industry, no one is as well-versed in the benefits of going modular as Mārcis Kreičmanis. As the co-founder and CBDO of LAMOD in Riga, Latvia, Mārcis has made it his ultimate goal to address the inefficiencies of traditional construction.
From Furniture Builder to ‘Activist Architect’: Stuart Emmons’ Unique Journey
Stuart Emmons was fascinated by buildings at a young age. He remembers building sand cities with his brother during trips to the Jersey shore. His father gave him his first drawing table at the age of ten. Today, he is an experienced architect who received his FAIA in June 2025. The road he took is unique, to say the least.
Forge Craft Architecture + Design: Codes, Contracts, and Intellectual Property
Founding Principal and Director of Modular Practice for Forge Craft Architecture + Design, Rommel Sulit, discusses the implications of codes, contracts, and intellectual property on
modular construction.
Eisa Lee, the “Bilingual” Architect
Now as the founder of XL
Architecture and Modular Design in Ontario, Canada, she applies not just her education as a traditional architect but an entire holistic view on modular design. It’s this expansive view that guides her work on being a true partner that bridges the gap between architects and modular factories as they collaborate on the design process.
Tamarack Grove Engineering: Designing for the Modular Sector
The role of a structural engineer is crucial to the success of a modular project, from initial analysis to construction administration. Tamarack Grove offers structural engineering services — project analysis, plan creation, design creation, and construction administration — for commercial, manufacturing, facilities, public services, and modular. Modular is only one market sector the company serves but it is an increasingly popular one.
Engineer Masters the Art of Listening to His Customers
Since founding Modular Structural Consultants, LLC. in 2014, Yurianto has established a steady following of modular and container-based construction clients, primarily manufacturers. His services often include providing engineering calculations, reviewing drawings, and engineering certification
Inside College Road: Engineering the Modules of One of the World’s Tallest Modular Buildings
College Road is a groundbreaking modular residential development in East Croydon, South London by offsite developer and contractor, Tide, its modular company Vision Volumetric (VV), and engineered by MJH Structural Engineers.
Design for Flow: The Overlooked Power of DfMA in Modular Construction
Unlocking higher throughput, lower costs, and fewer redesigns by aligning Lean production flow with design for manufacturing and assembly.