What’s Next: UNB OCRC Student Competition Previews the Future of Offsite Building
For the second year in a row, the University of New Brunswick’s Off-Site Construction Research Centre (OCRC), a research group dedicated to optimizing alternate solutions to on-site construction, presented its Off-site Construction Student Design Competition in partnership with the OSCO Construction Group. This competition—sponsored again by the Modular Building Institute—showcased student design innovation in modular, prefabricated, panelized, and other types of off-site construction and featured entries from dozens of interdisciplinary collegiate teams.
The objective of the competition was simple: to introduce students to offsite construction and to encourage interdisciplinary collaboration. It was also an opportunity to showcase how offsite construction’s many benefits, including reduced construction timelines, improved safety, and improved construction quality, can benefit the construction industry.
The Challenge
This year’s teams were challenged to design and present plans for a residence building for the University of New Brunswick (Fredericton) campus. The building needed to be at least 50% prefabricated, and the proposal needed to demonstrate how an offsite solution can address the project needs. Students were encouraged to consider pre-cast elements, sustainable, green technologies in their solutions.
Project Requirements:
- Design a new residential/commercial structure to replace an existing structure on campus, including 3D renderings, technical drawings, assembly diagrams, and more
- New structure should include a daycare facility and commercial space on the first floor
- Upper levels of the new structure to be living spaces
- Targeted to be a LEED Gold and net zero building
- Other aspects to consider:
o Demolition methods
o Parking lot
o Construction methods and sequencing, considering the nearby school zone
o Local bylaws and zoning
o Inclusiveness and accessibility in the design
o Incorporation of Indigenous art
Judging Criteria
The entries were judged using three criteria:
- 25% graphic presentation/design
- 50% creative demonstration of the potential of offsite construction
- 25% project feasibility/buildability
“OCRC is always innovating new ways to move away from the traditional “stick-built” construction into prefabricated and off-site construction. We work with many student researchers for our projects and know the kind of value they bring. We had ideated the Off-site Construction Student Design Competition to present students with a fun learning-based opportunity to help put their innovations in front of a larger audience, get expert feedback, and showcase their abilities simultaneously. The second year of doing this competition brought in many great ideas that showcased prefabricated and off-site focused mixed commercial and residential buildings that are sustainable and meet the need of the hour. We would like to thank MBI for their continued support of the competition.”
Brandon Searle, Director, Innovation and Operations, OCRC, University of New Brunswick
The Winners
First Place: The Montgomery Complex
Team members: Anneliese Sirju, Luisa Prestes, Luz Almazan Martinez, Leslie Anne Bugayong, Julianne Brewer, Jiyoung Park, Hyoung Sik Yoon, and Ming Kai Tang (Southern Alberta Institute of Technology)
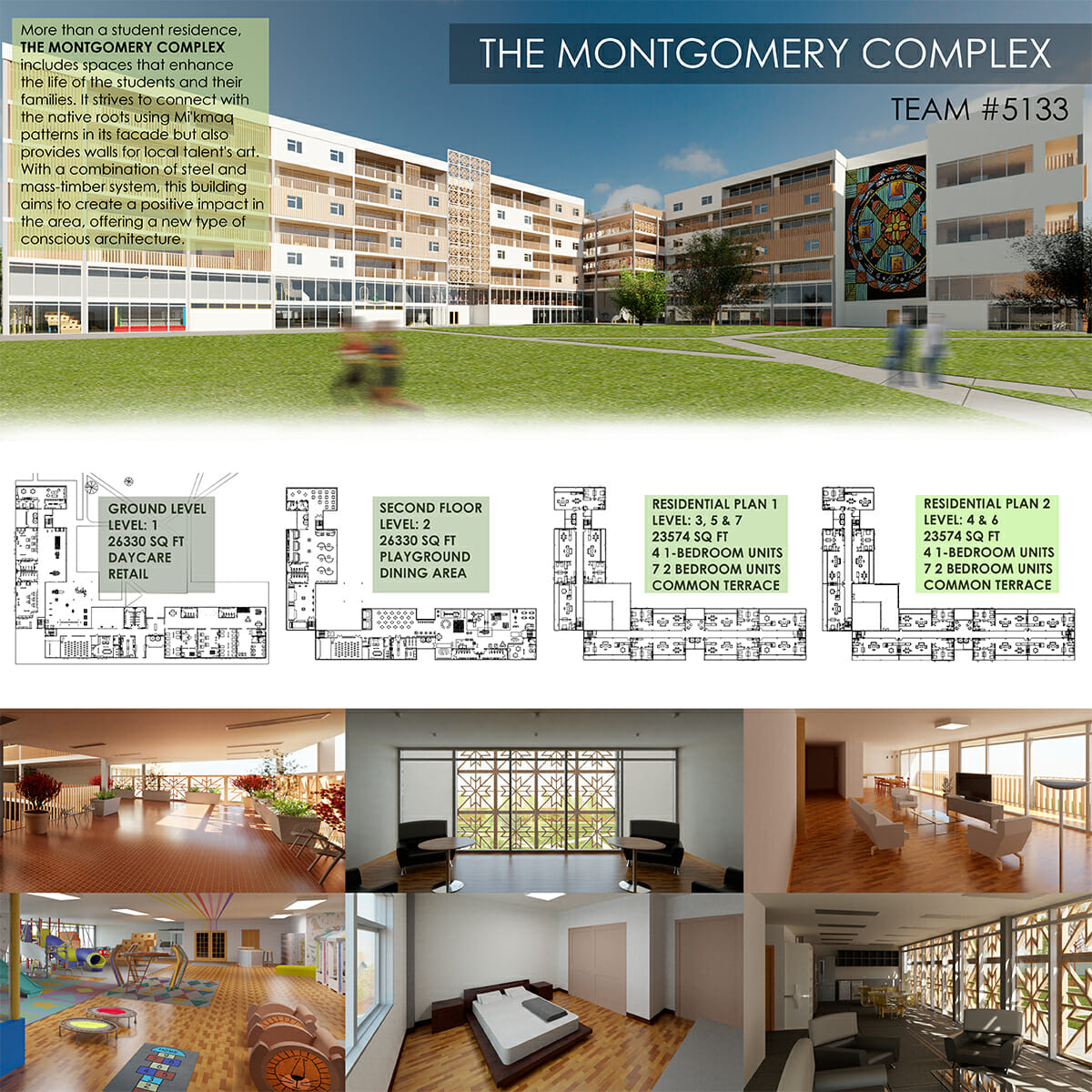
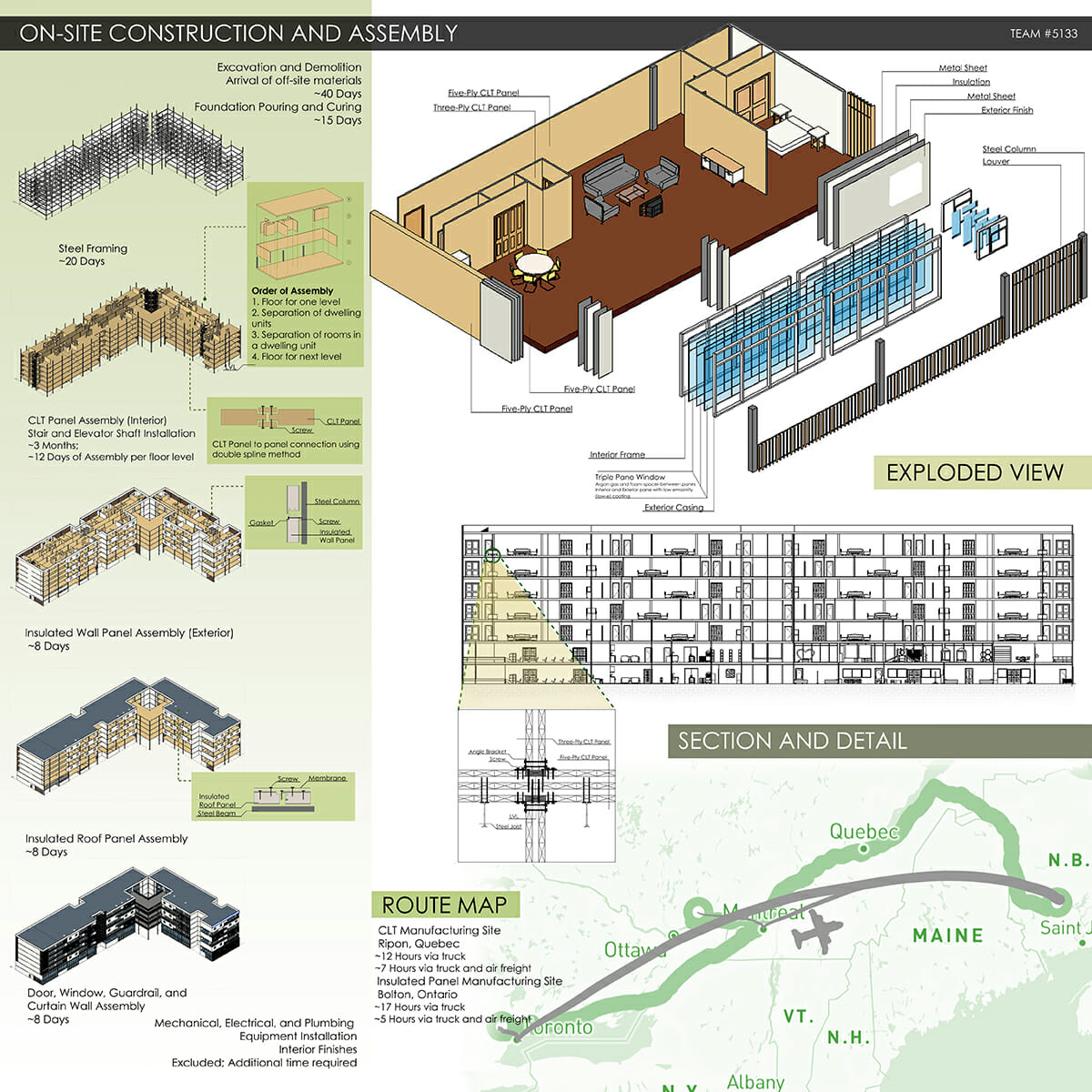
“More than student residence, The Montgomery Complex includes spaces that enhance the life of the students and their families. It strives to connect with native roots using Mi’kmaq patterns in its façade but also provides walls for local talent’s art. With a combination of steel and mass-timber, this building aims to create a positive impact in the area, offering a new type of conscious architecture.”
“We started developing the geometry of the design by using the existing buildings footprint as reference,” says team leader Luz Almazon. “Our first ideas leaned towards an L-shaped building which later evolved into two towers connected by terraces. This final itineration allowed us to stay within a scale that was not too overwhelming in terms of design.”
Teammate Leslie Bugayong added, “The majority of the walls would be built offsite. The interior CLT panels could be manufactured nearby while exterior walls would be insulated panels.”
“Construction would be efficient, more sustainable than using traditional methods, and could set the standard for a new type of architecture in the area,” concluded Almazon.
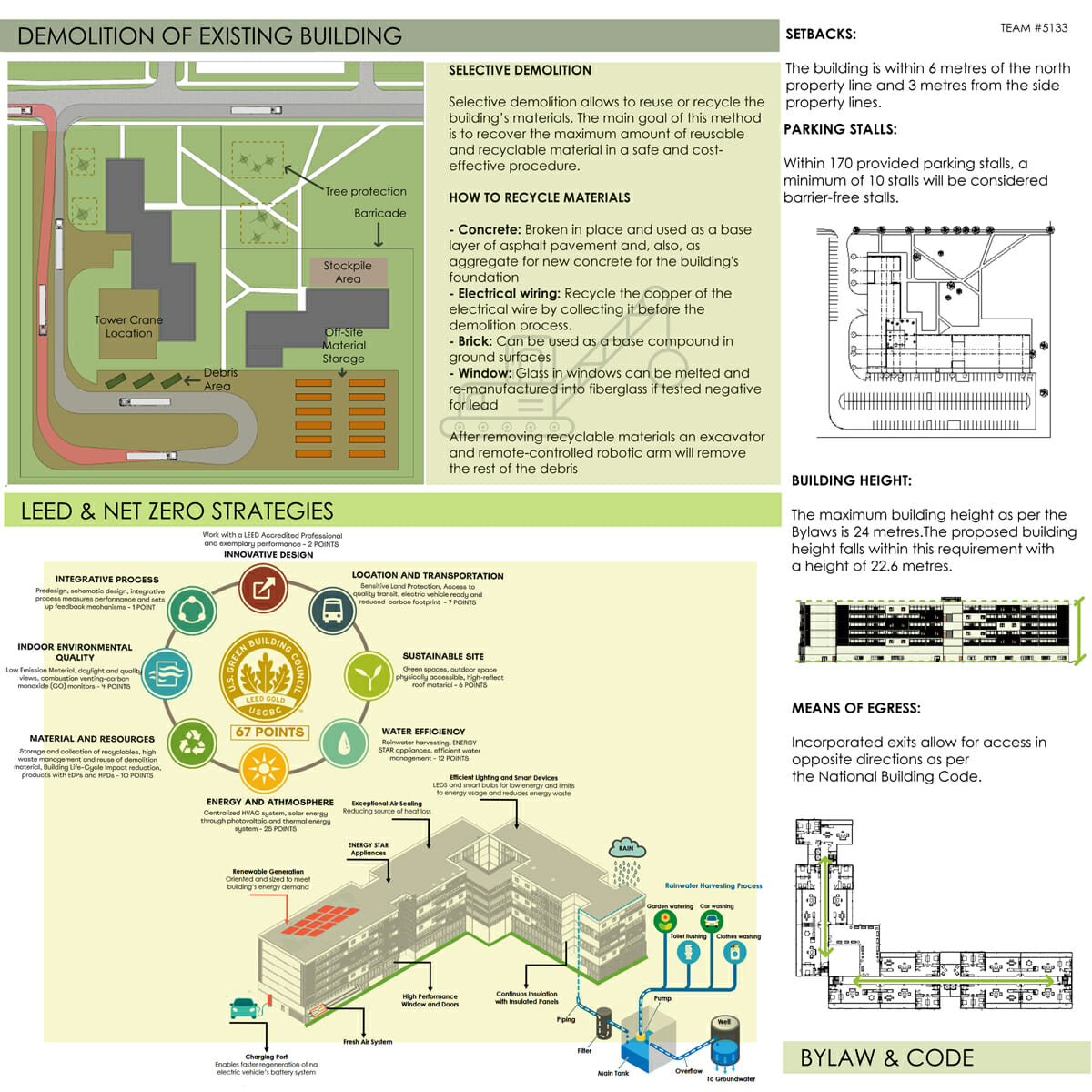
Second Place: The Magee-Mcloud Housing
Team members: Simon-Olivier Fortin, Sarah Samsoudin, and Charles-Emmanuel Lambert (Université du Québec à Montréal)
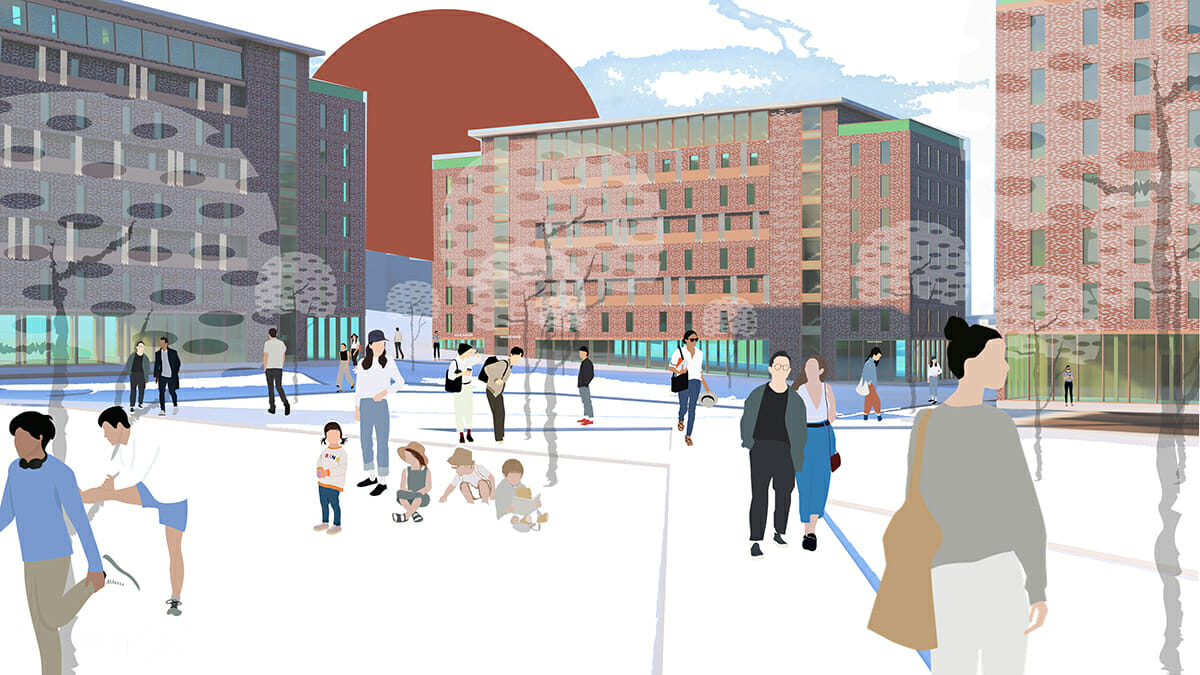
“We started working on the plans with a grid pretty early on in order to coordinate the structure and the layouts efficiently,” said team member Sarah Samsoudin. “We went through a lot of iterations while trying to figure out the best option. The goal was to offer large common spaces and smaller private rooms without compromising privacy and comfort, as well as avoiding waste and promoting a modular approach.
The rooftops, in a similar layout to the ground floors, each have two terraces and two co-working areas aligned with the vertical circulation blocs. At the heart of the floor is a mixed-use space, related to the commercial usage on the ground floor. On top of the market is a greenhouse, on top of the drugstore is a gym and of top of the daycare is a reception hall. These amenities would be available to all students, not only those living in the residences, to create a stronger sense of community.”
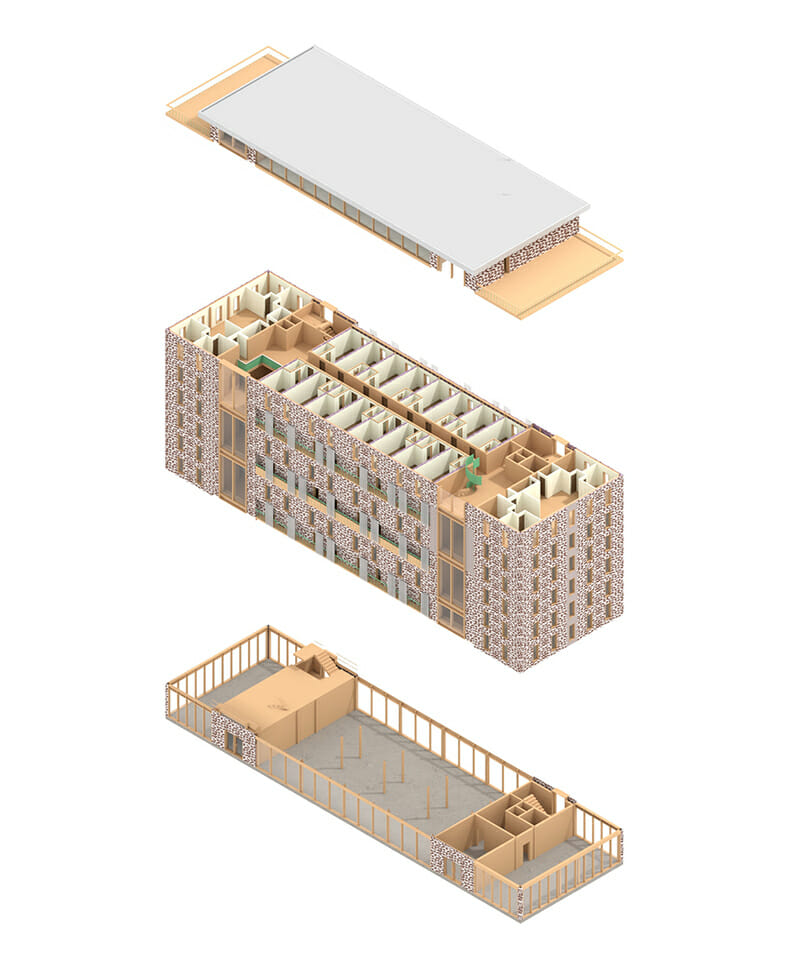
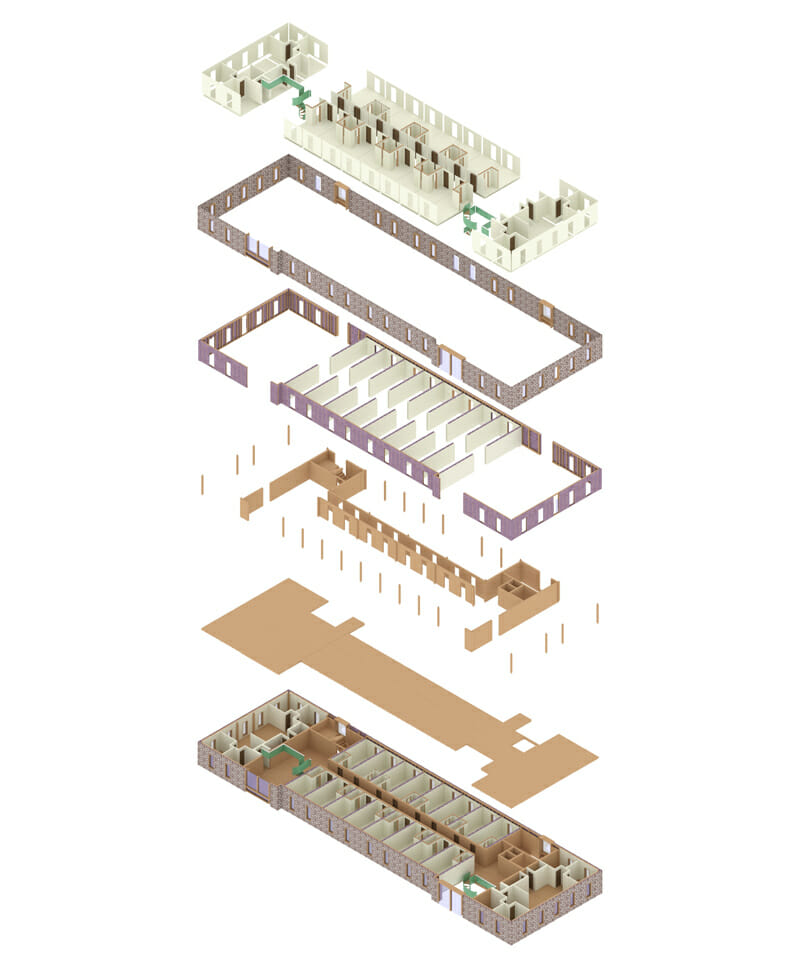
“I love that offsite construction and modular design, through architecture, is a way to express the celebration of modernity and technological advancements. A very large portion of the world’s carbon emissions comes from construction, and it is our duty, as designers of tomorrow, to act
ethically towards our planet and its occupants.”
—Sarah Samsoudin, part of this year’s second place-winning team from Université du Québec à Montréal
About the Author: John McMullen, PCM, is the marketing director for the Modular Building Institute. You can reach him directly at mcmullen@modular.org or on LinkedIn.
More from Modular Advantage
AI, Faster Sets, and Automation: The Future of Modular is at World of Modular
While the modular building industry has long known that it can be an effective solution to increase affordable housing, the word is slowly spreading to more mainstream audiences. Three presentations at this year’s World of Modular in Las Vegas hope to provide insight and direction for those seeking a real solution to the crisis.
An Insider’s Guide to the 2025 World of Modular
The Modular Building Institute is bringing its global World of Modular (WOM) event back to Las Vegas, and with it comes some of the industry’s best opportunities for networking, business development, and education. Over the course of the conference’s four days, there will be numerous opportunities for attendees to connect, learn, and leverage event resources to get the most out of the conference.
Affordable Housing Now: The Industry’s Best Bring New Solutions to World of Modular
While the modular building industry has long known that it can be an effective solution to increase affordable housing, the word is slowly spreading to more mainstream audiences. Three presentations at this year’s World of Modular in Las Vegas hope to provide insight and direction for those seeking a real solution to the crisis.
Opportunities for Innovation in Modular Offsite Construction
Modular Offsite Construction has already shattered the myth that it only produces uninspired, box-like designs. Architectural innovations in module geometry, configurations, materials, and products make it possible to create visually stunning buildings without sacrificing functionality or efficiency.
Safe Modular Construction with Aerofilm Air Caster Transport
In collaboration with Aerofilm Systems, Heijmans developed innovative skids using air caster technology for moving modules easily and safely. These pallets are equipped with an auto-flow system, making operation extremely simple.
Miles, Modules, and Memes: Building a Modular Network One Flight at a Time
At the end of the day, social media is just another tool for building connections, and like any other tool, needs to be used skillfully to work properly. Use social media thoughtfully, and it will open doors to real opportunities and relationships you didn’t even see coming.
Falcon Structures: Thinking Inside the Box
Some of Falcon’s latest projects include creating container solutions for New York’s Central Park and an East Coast professional baseball team. More and more, Falcon is shipping out container bathrooms and locker rooms to improve traditionally difficult work environments, like those in oil and gas or construction.
UrbanBloc—From Passion to Industry Leader
UrbanBloc specializes in three main categories or markets – what they call “Phase 0” projects, amenities, and urban infill. Clients are often attracted to shipping containers because from a real estate perspective they are considered an asset. Having the flexibility to move and transport these assets allows owners to respond to different circumstances in a fluid manner that they can’t get with standard construction.
The Hospitality Game-Changer
“Hospitality is about more than just providing a service – it’s about delivering an experience,” says Anthony Halsch, CEO of ROXBOX. “And that’s where containers thrive. They allow us to create spaces that are unique, efficient, and sustainable.”
Container Conversions Counts on Simplicity to Provide Critical Solutions
Container Conversions has fabricated and developed thousands of containers for varied projects, including rental refrigeration options, offices, kitchens, temporary workplace housing, and mobile health clinics.