The Rapid Rise of Affordable Modular Housing in Canada
In October 2020, the Government of Canada, through its Canadian Mortgage Housing Corporation (CMHC), launched the Rapid Housing Initiative (RHI) to address the urgent housing needs of vulnerable Canadians. The initial round of the RHI’s funding—all of which went toward modular buildings—was CN $1 billion, and in the immediate wake of COVID-19, it went quickly. And it was put to immediate use.
“The federal funding available through RHI set out to cover the construction of new rental housing units that would be available for occupancy within 12 months,” says Mark Becker, Chief Operating Officer at Dexterra Group and interim President, NRB Modular Solutions. “This is a very tight timeline to deliver on and it made modular construction an attractive choice to provide the fastest path to occupancy.”
In fact, the RHI exceeded its initial target of creating 3,000 new affordable housing units, and, in total, supported the construction of more than 4,700 units across Canada.
In 2021, the RHI was provided a second round of funding: an additional $1.5 billion toward the construction of new multifamily housing. And like the first round, these additional funds helped the RHI exceed its initial target of creating 4,500 new affordable units and is expected to create a total of over 5,400 new housing units across Canada.
These huge successes were followed by a pair of even bigger announcements in 2021. Two of the continent’s largest banks, Scotiabank and Bank of Montreal, each agreed to work with the CMHC and commit a combined $22 billion to create new affordable housing across Canada over the next 10 years.
As it has from the beginning, MBI is working closely with the CHMC to funnel as much of these committed funds as possible to the modular-focused RHI, which itself is currently working on the application guidelines for its expected third round of funding.
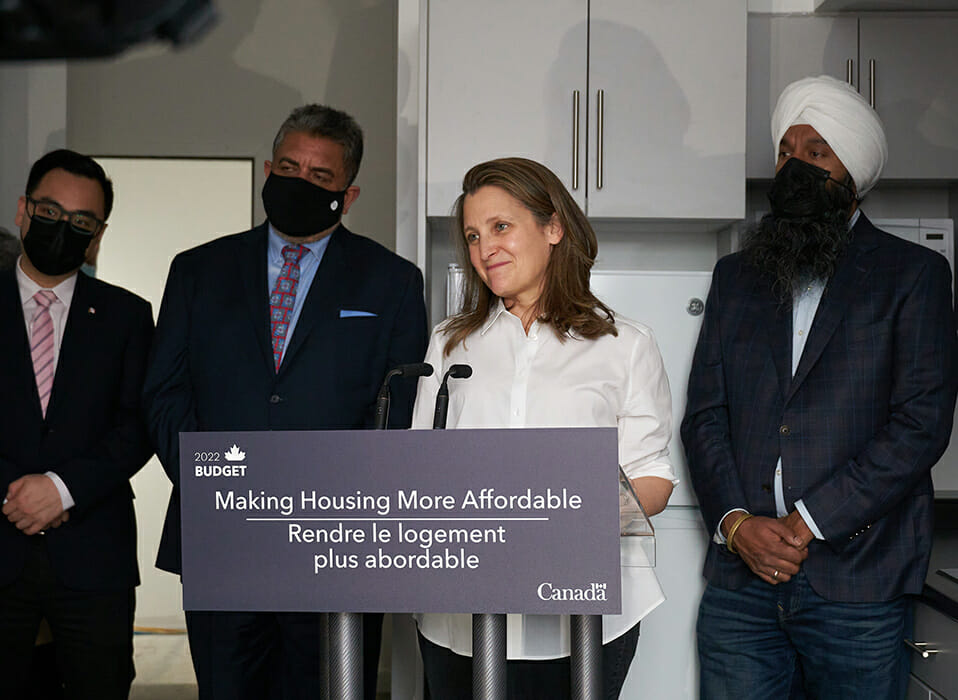
Canadian Deputy Prime Minister and Minister of Finance, Chrystia Freeland, speaks to the importance of addressing the affordable housing crisis in Canada during a visit to the site of Nomodic’s modular supportive housing complex for Atira Women’s Resource Society in Surrey, BC.
Photo credit: Nomodic and Martin Knowles Photo/Media
"Given its inherent benefits of speed, scalability, and reliability, modular construction should continue to be seen as the ideal solution to supply much-needed housing quickly during the third funding round for the Rapid Housing Initiative,” says Kevin Read, president and CEO at Nomodic, a Canadian provider of prefabricated construction solutions who has built several modular projects funded under the RHI.
“Modular building is integral to making an impact on the need for affordable and attainable housing across our country,” says Andrew Neill, president and CEO of ANC, an Ontario-based general contractor, construction management company, volumetric steel modular manufacturer, and winner of the 2021 Canadian Homebuilders Association National Housing Award for Modular Innovation. “Being able to start the manufacturing process before building permits are issued allows us to get ahead of schedules and provide ‘rapid housing’ which is not possible with conventional construction methods.”
“We fully expect modular adoption to continue to grow and likely accelerate as developers, architects, and their clients look for ways to leverage the unique benefits of modular construction,” concludes Dexterra Group’s Mark Becker.
MBI is proud to have helped make such an impact, not only on behalf of its members, but for those who have been directly helped through the creation of these new affordable homes.
What follows is a small selection of case studies—projects built by MBI members through the RHI—that we hope are but the tip of iceberg as the CMHC continues its efforts to provide safe, high-quality, affordable modular housing for residents across Canada.
Rapid Housing Initiative Case Studies
MBI members have quickly built a variety of multifamily buildings as part of the Rapid Housing Initiative. Below are case studies from three companies—ANC, Nomodic, and NRB Modular Solutions—but they represent just a sampling of the companies who have participated.
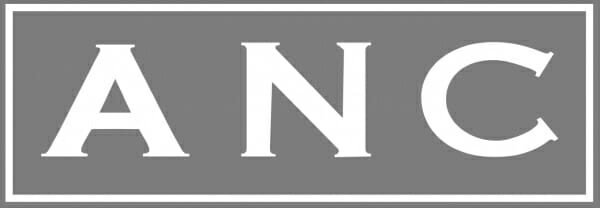
Case Studies Include:
- CASE Homes
- Brant Native Housing – Transitional Homes
- Six Nations Housing
“ANC has a ‘base’ modular ‘box’ design that was developed to be exceptionally fluid to many types of housing structures. Using our ‘base’ modular structure, we were able to design four very unique projects concurrently. A four-plex, a duplex, a townhome complex that had two one floor homes, and three two storey homes in one block, as well as a four-storey apartment building. All these projects used our base modular ‘box’ and ANC was able to configure them to each development’s needs.”
Andrew Neill, President and CEO, ANC
CASE Homes
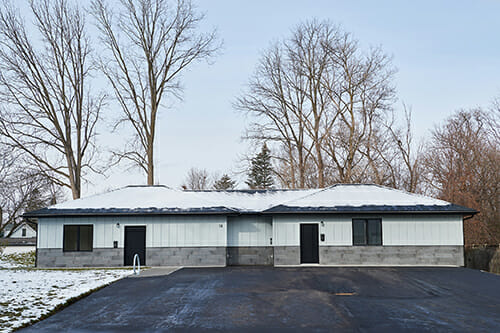
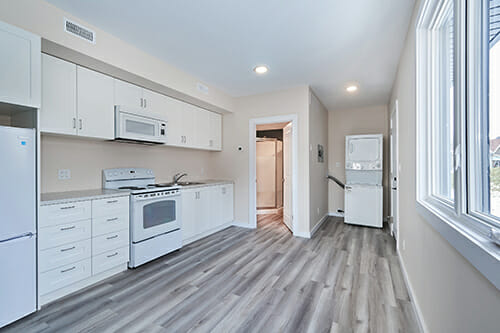
Through a design/build contract, ANC provided four (4) CSA-certified modular homes under the Government of Canada’s Rapid Housing Initiative.
ANC Modular fabricated three (3) standard and one (1) AODA/FADS-compliant bachelor units concurrently while completing site plan approvals and permit processes.
At issuance of permit, all four (4) homes were erected in three (3) hours, cladded and roofed within five (5) days.
Brant Native Housing – Transitional Homes
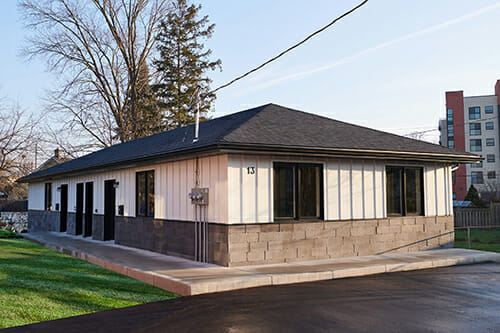
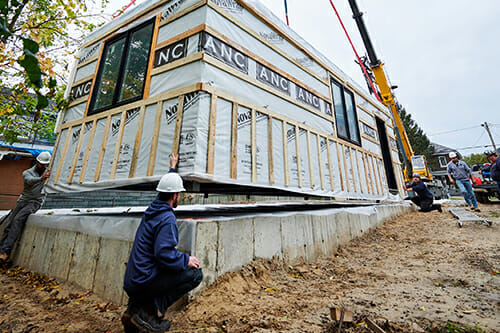
Through a design/build contract, ANC provided four (4) CSA-certified mods configured into two (2) 2-bedroom semi-detached homes under the Government of Canada’s Rapid Housing Initiative.
Site setback constraints made for minimum neighborhood impact and disruption.
At issuance of permit, all four (4) mods were erected in three (3) hours, then cladded and roofed in five (5) days.
Six Nations Housing
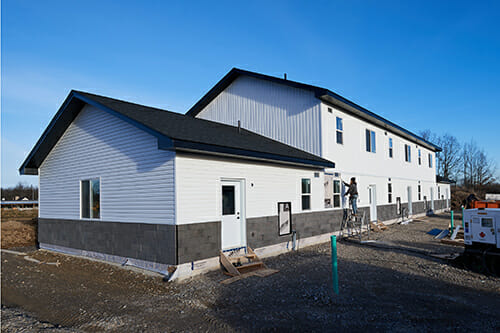
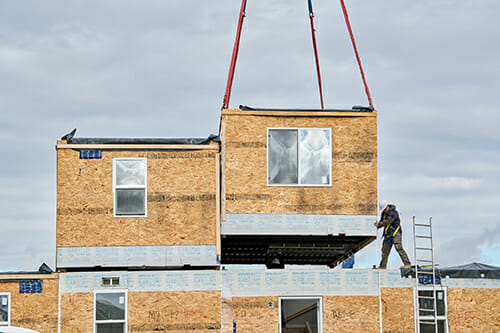
Through a design/build contract, ANC provided sixteen (16) CSA-certified mods configured in to two (2) 2-bedroom single storey and three (3) 3-bedroom 2-storey townhomes. These buildings were completed under the Government of Canada’s Rapid Housing Initiative.
Three (3) months from approved design plans, ANC landed all sixteen (16) modular units in a single day. Townhomes were roofed and cladded within ten (10) days of erection. Tie-ins and ready for occupancy permits were complete within four (4) weeks of landing.
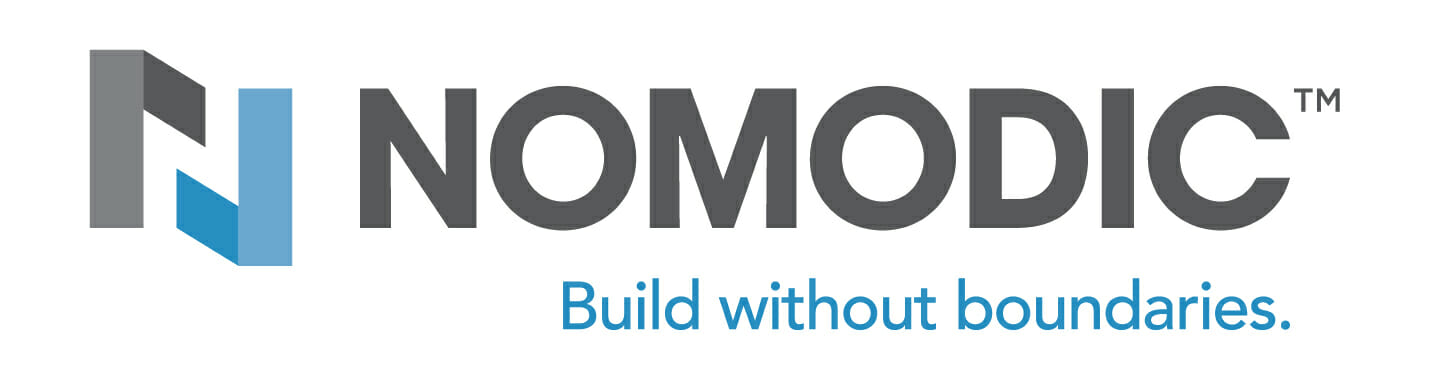
Case Studies Include:
- Indigenous Supportive Housing Complex
- ‘Little’s Too’ Supportive Housing Complex
“We’ve seen firsthand how these projects have made a difference. By giving people a key to the first front door they’ve had in years, it gives them a sense of ownership and a sense of pride. As programs such as the RHI continue to be implemented, Nomodic and its partners remain well-equipped to adapt to the growing demand and deliver sustainable, community-focused housing within government-prescribed timelines.”
Kevin Read, President and CEO, Nomodic
Indiginous Supportive Housing Complex
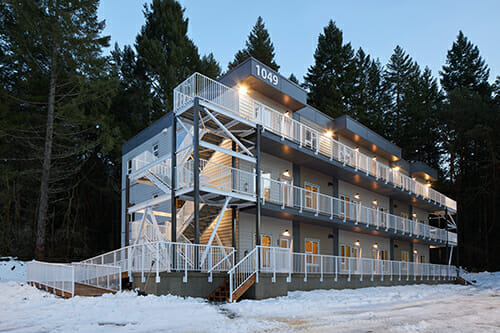
Photo credit: Nomodic and Martin Knowles Photo/Media
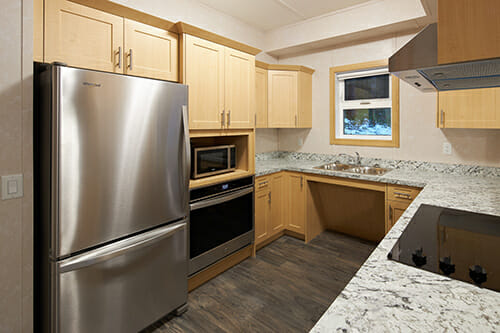
Location: North Saanich, British Columbia
Building Type: Volumetric Modular
Completed: January 2022
Size: 12,000 sq.ft.
Levels: 3
Suites: 12
Onsite duration: 181 days
Key features:
• Six 3-bedroom suites, six 1-bedroom suites
• Full kitchens with energy efficient appliances
• High quality, premium finishes
• Large private bathrooms with walk-in showers
• Accessible features including wheelchair ramps
Built with the support of CMHC’s Rapid Housing Initiative, this building helps address the urgent need for affordable housing for residents of Pauquachin First Nation in North Saanich, BC. This project was designed and constructed in less than twelve months.
"Little's Too" Supportive Housing Complex
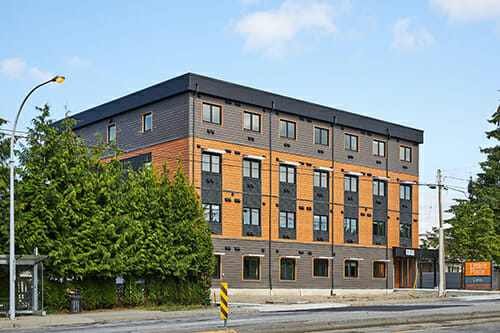
Photo credit: Nomodic and Martin Knowles Photo/Media
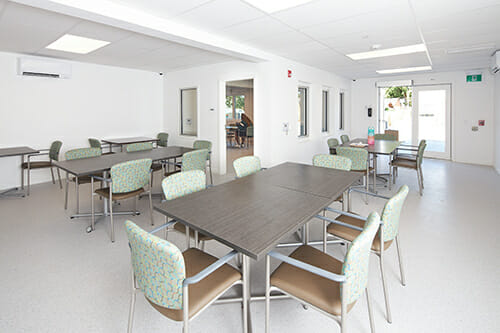
Location: Surrey, British Columbia
Building Type: Volumetric Modular
Completed: August 2022
Size: 24,095 sq. ft.
Levels: 4
Suites: 44
Key features:
• 44 self-contained suites, each with kitchenette/washroom
• Commercial kitchen, dining and lounge areas, storage, laundry, and tenant support rooms
• Accessible features including walk-in showers
• Meets BC Energy Step Code 4
Built with funding from CMHC’s Rapid Housing Initiative and in cooperation with Turnbull Construction Project Managers, this new complex for Atira Women’s Resource Society serves women who are homeless or at risk of homelessness. The facility provides wrap-around services, integrated health supports, and daily meals for residents. The building was craned in only five days, minimizing traffic and disruption to the community.
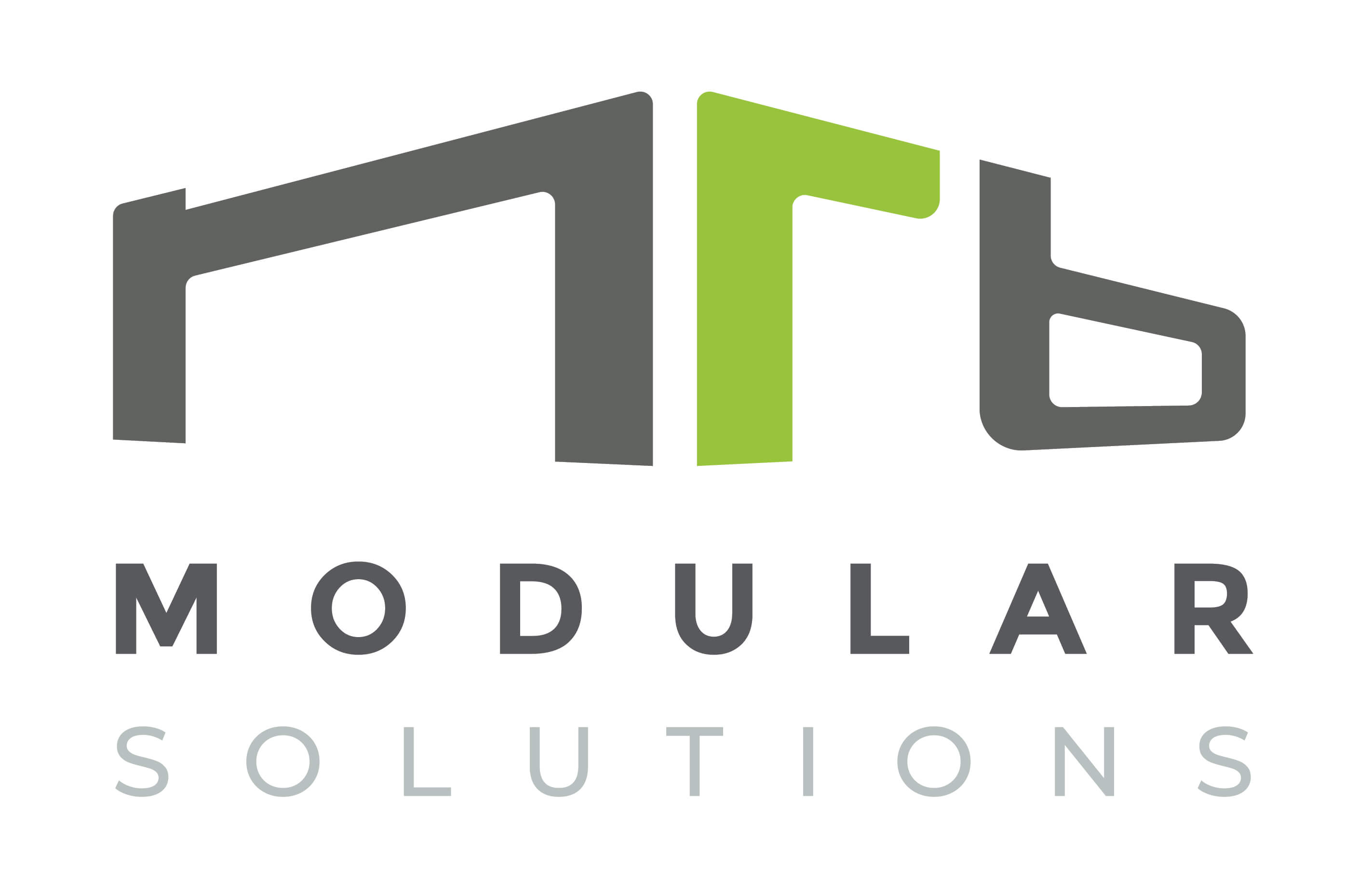
Case Studies Include:
- Tyee Seniors Housing
- City of Toronto Supportive Housing
“We wanted to challenge the perception that modular buildings couldn’t seamlessly integrate within a community. To combat the stigma associated with homelessness, one of our key goals with the 11 Macey Ave and 150 Harrison St project was to foster inclusion and create a well-integrated, welcoming space.”
Mark Becker, Chief Operating Officer at Dexterra Group and interim President, NRB Modular Solutions
Tyee Seniors Housing
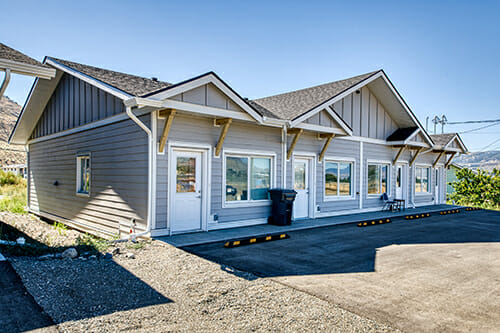
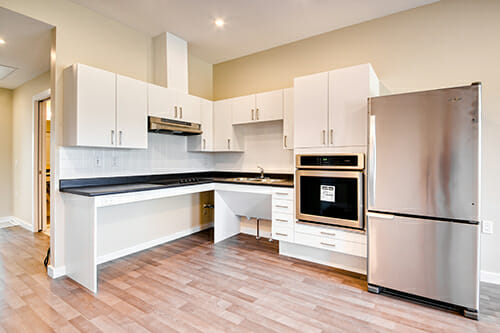
Building Application: Affordable Seniors Housing
Building Type: Volumetric Modules
Project Location: Kamloops, British Columbia
Building Size: 2 Bldgs at 2,404 SF/
1 Bldg at 2,204 SF
Project Timeline: 11 Months
Background
The Tk’emlúps te Secwépemc Indian Band (TteS) in Kamloops, British Columbia received 10 suites of affordable housing, built on its lands at Tyee Park.
This project was funded as part of the Canada Rapid Housing Initiative (RHI) to create new, affordable housing for elders in the local community.
The manufacturing was completed at NRB’s largest manufacturing plant in Kamloops which is also located on Tk’emlúps te Secwépemc land base, with both the land and building under long‐term lease.
Our successful collaboration with TteS to develop the design resulted in culturally sensitive housing units providing TteS with certainty of cost, schedule, and quality.
Challenge
Under the criteria guidelines in place from the RHI program, NRB was awarded the contract to build two 1-storey four-plexes and one 1-storey duplex in May of 2021 with a planned completion of December 2021.
Due to wildfires in the area escalating surrounding priorities for BC Hydro, a pole removal caused the installations to see a delay in building completion until early April 2022.
Results at a Glance
The supply and Installation of Seniors Housing included the following:
• Two four-plex units and one 2-bedroom duplex.
• Total of 10 suites.
City of Toronto Supportive Housing
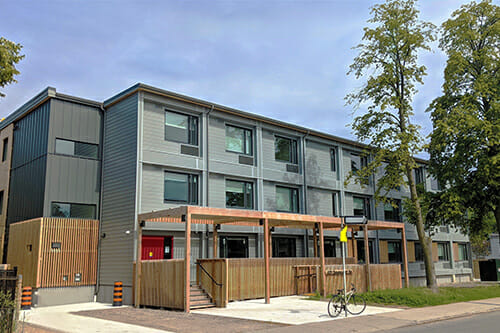
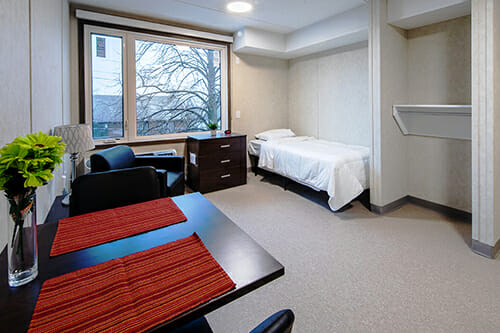
Building Application: Affordable Housing
Building Type: Volumetric Modules
Project Location: Toronto, Ontario
Building Size: Two Buildings — 27,000 Sq.ft. Each
Project Timeline: 10 Months
Background
As part of the Housing Now initiative implemented by the City of Toronto in 2019, 11 City-owned sites were identified for the development of affordable housing. In May 2020, the City chose NRB to design, manufacture, and install 100 modular units of permanent supportive housing as Phase I of a pilot project.
Challenge
We were tasked with the design, manufacturing, transportation, and installation of two affordable housing complexes in a timely manner to accommodate the rapid need for housing for the residents who are struggling to find a home in the City.
The first building, located on Macey Avenue in the area of Pharmacy and Danforth avenues, has 56 suites. The second building is located on Harrison Street near Dovercourt Road and Dundas Street and has 44 suites.
Results at a Glance
The two buildings feature 100 single occupancy suites, with self-contained bathrooms and kitchens, individual climate control and a private living space. The central building has an indoor and outdoor amenity space, central laundry, commercial kitchen and dining area 25% of the buildings’ suites are accessible and Gold Certified by the Rick Hansen Foundation Accessibility Certification. The structures also come equipped with a CCTV camera monitoring system, an in-suite intercom network, and exterior solar
About the Author: John McMullen, PCM, is the marketing director for the Modular Building Institute. You can reach him directly at mcmullen@modular.org or on LinkedIn.
More from Modular Advantage
AI, Faster Sets, and Automation: The Future of Modular is at World of Modular
While the modular building industry has long known that it can be an effective solution to increase affordable housing, the word is slowly spreading to more mainstream audiences. Three presentations at this year’s World of Modular in Las Vegas hope to provide insight and direction for those seeking a real solution to the crisis.
An Insider’s Guide to the 2025 World of Modular
The Modular Building Institute is bringing its global World of Modular (WOM) event back to Las Vegas, and with it comes some of the industry’s best opportunities for networking, business development, and education. Over the course of the conference’s four days, there will be numerous opportunities for attendees to connect, learn, and leverage event resources to get the most out of the conference.
Affordable Housing Now: The Industry’s Best Bring New Solutions to World of Modular
While the modular building industry has long known that it can be an effective solution to increase affordable housing, the word is slowly spreading to more mainstream audiences. Three presentations at this year’s World of Modular in Las Vegas hope to provide insight and direction for those seeking a real solution to the crisis.
Opportunities for Innovation in Modular Offsite Construction
Modular Offsite Construction has already shattered the myth that it only produces uninspired, box-like designs. Architectural innovations in module geometry, configurations, materials, and products make it possible to create visually stunning buildings without sacrificing functionality or efficiency.
Safe Modular Construction with Aerofilm Air Caster Transport
In collaboration with Aerofilm Systems, Heijmans developed innovative skids using air caster technology for moving modules easily and safely. These pallets are equipped with an auto-flow system, making operation extremely simple.
Miles, Modules, and Memes: Building a Modular Network One Flight at a Time
At the end of the day, social media is just another tool for building connections, and like any other tool, needs to be used skillfully to work properly. Use social media thoughtfully, and it will open doors to real opportunities and relationships you didn’t even see coming.
Falcon Structures: Thinking Inside the Box
Some of Falcon’s latest projects include creating container solutions for New York’s Central Park and an East Coast professional baseball team. More and more, Falcon is shipping out container bathrooms and locker rooms to improve traditionally difficult work environments, like those in oil and gas or construction.
UrbanBloc—From Passion to Industry Leader
UrbanBloc specializes in three main categories or markets – what they call “Phase 0” projects, amenities, and urban infill. Clients are often attracted to shipping containers because from a real estate perspective they are considered an asset. Having the flexibility to move and transport these assets allows owners to respond to different circumstances in a fluid manner that they can’t get with standard construction.
The Hospitality Game-Changer
“Hospitality is about more than just providing a service – it’s about delivering an experience,” says Anthony Halsch, CEO of ROXBOX. “And that’s where containers thrive. They allow us to create spaces that are unique, efficient, and sustainable.”
Container Conversions Counts on Simplicity to Provide Critical Solutions
Container Conversions has fabricated and developed thousands of containers for varied projects, including rental refrigeration options, offices, kitchens, temporary workplace housing, and mobile health clinics.