Modular Building Poised for Takeoff Globally
A report from Anirban Basu, chairman & CEO of Sage Policy Group and Chief Economist of the Modular Building Institute
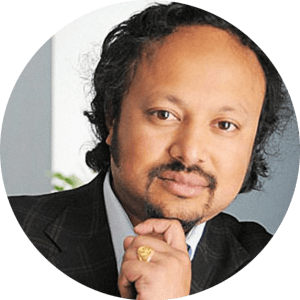
Anirban Basu is chairman & CEO of Sage Policy Group and Chief Economist of the Modular Building Institute
Limited Market Penetration to Date
Approximately two-and-a-half years ago, COVID undid the global economy. A period of progress associated with the development of just-in-time worldwide supply chains, diminished global poverty, rampant innovation, and a dearth of nation versus nation military conflict ended. It has been replaced by a period of disrupted supply, elevated inflation, food and energy crises, a brutal war in Eastern Europe, and rising geopolitical tensions between the world’s two leading superpowers, America and China.
Just-in-time has become “don’t hold your breath” as materials and worker shortages have conspired with elevated transportation costs to raise the price of virtually any manufactured good amidst lingering equipment and related shortages. Many Americans have left the labor force. Others insist on working from the comfort of their homes. This has further exacerbated supply, resulting not only in delays, but also in less consistent customer services. All of this has implications for modular building, and those implications are generally positive.
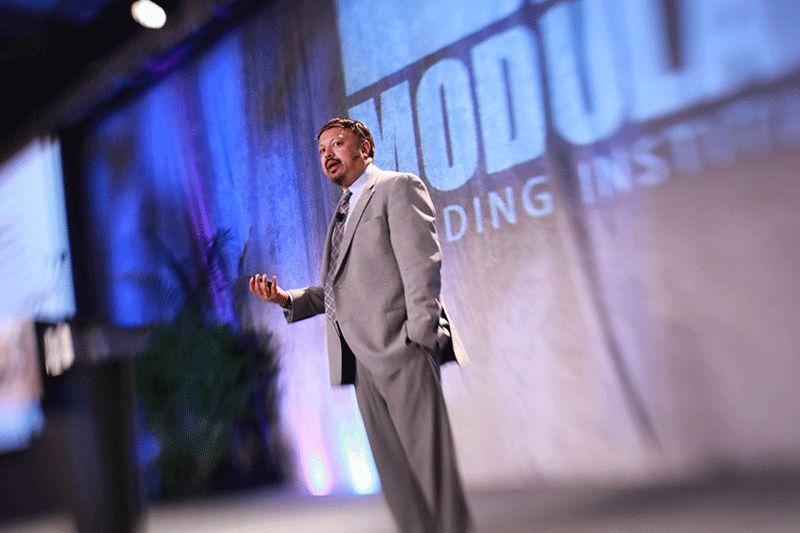
Anirban Basu speaks at the 2022 World of Modular conference and tradeshow.
That modular building hasn’t already gained more market share is a source of bewilderment to many. Though the technology has been around for more than 70 years, modular building in the U.S. has never gained as solid a foothold as it has in other societies. In Scandinavia, known for its commitment to efficiency and common sense, nearly half of all housing is manufactured and assembled off-site. In Japan, known for its scientific management of societal requirements, roughly 15 percent of housing is fabricated in a facility and transported to the project-site.
In the U.S., however, the technology remains far more niche, with only 3 percent of housing built in this fashion. Recent data from the Modular Building Institute indicate that modular construction still comprises only about 5 percent of commercial construction. As the balance of this article will indicate, modular building is about to takeoff globally and in America.
Workforce Considerations
The stereotypes are true – younger workers really are striving for work-life balance. A recent study conducted by PwC found that work-life balance is important for 95 percent of Millennials. This is far higher than recorded among prior generations. Many factors are at work, including the fact that 42 percent of workers stay connected at work even while on vacation. According to a Deloitte survey, Millennials and Gen Zers also measure success differently. Rather than focusing on owning tangible assets, many of these younger workers prioritize work-life balance when evaluating career opportunities.
These dynamics represent a significant opportunity for modular building. Traditional construction typically transpires during fixed hours. Because people often work in teams, they must be at jobsites at specified times. Opportunities to offer flexible hours are limited, particularly at a time when there is a general shortage of construction workers.
Moreover, those who work outdoors are subject to the vicissitudes of weather. Many workers are likely to prefer controlled settings. That is precisely what modular building offers. Because tasks are more easily separable (e.g., assembly line activities), opportunities for worker flexibility are greater.
Considerations of Climate
The world is presently amid an awkward transition from traditional fossil fuels to alternative energy like wind and solar power. That transition helps explain the elevated energy prices that Americans and others presently encounter. Obviously, the raging conflict between Russia and Ukraine hasn’t helped.
While some believe that the U.S. should recommit to fossil fuels, others remain concerned about global warming and increasingly violent weather. In short, the transition to alternative energy is likely to continue. In the meantime, energy prices are likely to remain higher than normal, even after the conflict in Eastern Europe ends.
Policymakers remain committed to climate. As of this writing, the U.S. Senate just passed a $700 billion package that embodies nearly $370 billion for climate related programs and initiatives. One of the bill’s primary goals is to reduce carbon emissions. The construction industry, with its reliance on heavy equipment and vehicles, is one of the largest producers of CO2 emissions. A United Nations Environmental Program report indicates that the industry produces “38 percent of total global energy related emissions”. To reach the 50 percent reduction in CO2 emissions goal by 2030, the global construction industry would have to cut emissions by 6 percent each year.
In this regard, modular building offers massive advantages. For instance, academics from the University of Cambridge and Edinburgh Napier University found that carbon dioxide emissions from homebuilding could be slashed by up to 45 percent with a modular construction system.
What this really tells us is that onsite builds produce massive amounts of carbon. The Urban Developer points out that onsite builds are “constructed using materials, components, and products. All this material has to be extracted from the ground, transported to a facility to be processed, transported again to be fabricated into a product, transported to site, and craned into place.” These processes inevitably result in the emission of greenhouse gases, including from fuel used for deliveries, heat used to reshape raw materials, and releases from manufacturing processes. Offsite prefabrication, by contrast, allows for more efficient processes, particularly if it is conducted close to a development site. Additionally, equipment used to assemble modules tends to be more energy efficient than equivalent machinery used onsite.
Negrón says that more and more clients are turning to prefabricated modular cleanrooms “because of the high quality, cost certainty, predictable schedules, and the ability to deliver projects much faster than traditional construction.”
Another advantage of POD cleanrooms is that they can be used temporarily and then re-located. Clients can use the cleanrooms for as long as they need them and then re-deploy them for another use or sell them. With traditional stick-built cleanrooms, the building expenses are sunk costs because the cleanrooms can’t be moved or re-sold as independent units if they’re no longer needed. Also, a small manufacturer can begin operating with one cleanroom POD and add more as the company grows and requires additional capacity — because each POD is completely self-contained.
A Response to the Devastation of War
Rebuilding Ukraine will take in the range of $600 billion. It is conceivable that war will continue to be a part of the landscape even as rebuilding commences. Modular construction represents a logical way to rebuild a society that faces the potential to rebuild often and expeditiously. Some industry insiders are pointing to the rebuilding of Ukraine to highlight the industry’s capabilities, flexibility, and contributions to a resilient built environment.
This is not merely theoretical. The Governor George Pataki Leadership Center, headed by the former New York governor, has worked to build and deliver modular housing units to Ukraine to help with the ongoing conflict. Media reports indicate that 18 units were delivered to the Kyiv region to house specialists working to clear debris and search for survivors.
Looking Ahead
Modular building is poised to experience substantial increases in market share over the next few years. That will support a cleaner, greener global environment, provide safer workplaces for employees, and help to more rapidly rebuild battered societies.
More from Modular Advantage
Oregon’s Prevailing Wage Proposal: A Wake-Up Call for Modular Construction
In early February, 2024, the Massachusetts Board of Building Regulations and Standards (BBRS) released its proposed 10th Edition building codes. This draft included several amendments targeting modular construction that would have created an extremely difficult environment for the entire modular industry and could have eliminated the industry entirely in the state.
Behind the Design of Bethany Senior Terraces, NYC’s First Modular Passive House Senior Housing Project
As more developers seek to meet new regulations for energy efficiency, the team at Murray Engineering has set a new record. With the Bethany Senior Terraces project, Murray Engineering has helped to develop NYC’s first modular structure that fully encompasses passive house principles — introducing a new era of energy efficiency in the energy-conscious city that never sleeps.
How LAMOD is Using Modular to Address Inefficiency, Sustainability, and the Future of Construction
As developers, designers, and contractors seek to understand the evolving needs of the modular industry, no one is as well-versed in the benefits of going modular as Mārcis Kreičmanis. As the co-founder and CBDO of LAMOD in Riga, Latvia, Mārcis has made it his ultimate goal to address the inefficiencies of traditional construction.
From Furniture Builder to ‘Activist Architect’: Stuart Emmons’ Unique Journey
Stuart Emmons was fascinated by buildings at a young age. He remembers building sand cities with his brother during trips to the Jersey shore. His father gave him his first drawing table at the age of ten. Today, he is an experienced architect who received his FAIA in June 2025. The road he took is unique, to say the least.
Forge Craft Architecture + Design: Codes, Contracts, and Intellectual Property
Founding Principal and Director of Modular Practice for Forge Craft Architecture + Design, Rommel Sulit, discusses the implications of codes, contracts, and intellectual property on
modular construction.
Eisa Lee, the “Bilingual” Architect
Now as the founder of XL
Architecture and Modular Design in Ontario, Canada, she applies not just her education as a traditional architect but an entire holistic view on modular design. It’s this expansive view that guides her work on being a true partner that bridges the gap between architects and modular factories as they collaborate on the design process.
Tamarack Grove Engineering: Designing for the Modular Sector
The role of a structural engineer is crucial to the success of a modular project, from initial analysis to construction administration. Tamarack Grove offers structural engineering services — project analysis, plan creation, design creation, and construction administration — for commercial, manufacturing, facilities, public services, and modular. Modular is only one market sector the company serves but it is an increasingly popular one.
Engineer Masters the Art of Listening to His Customers
Since founding Modular Structural Consultants, LLC. in 2014, Yurianto has established a steady following of modular and container-based construction clients, primarily manufacturers. His services often include providing engineering calculations, reviewing drawings, and engineering certification
Inside College Road: Engineering the Modules of One of the World’s Tallest Modular Buildings
College Road is a groundbreaking modular residential development in East Croydon, South London by offsite developer and contractor, Tide, its modular company Vision Volumetric (VV), and engineered by MJH Structural Engineers.
Design for Flow: The Overlooked Power of DfMA in Modular Construction
Unlocking higher throughput, lower costs, and fewer redesigns by aligning Lean production flow with design for manufacturing and assembly.