A New Off-Site Standard in the Works: Energy Efficiency, Water Conservation and MEP Systems
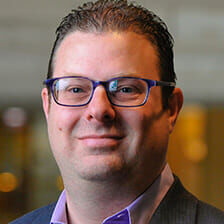
About the Author: Ryan Colker is the Vice President of Innovation at the International Code Council.
Buildings are the integration of multiple systems including mechanical, electrical and plumbing (MEP) to deliver an expected level of performance. These performance requirements include energy efficiency and water conservation. In the context of off-site construction, these systems can be considered at the level of panelized or volumetric modules. In some cases the off-site construction segment of projects can be solely focused on multi-trade mechanical racking.
Recognizing the value of standards in unlocking some of the benefits and efficiencies inherent in off-site construction, in September 2021 the International Code Council (ICC) and Modular Building Institute (MBI) released two new standards for off-site construction focusing on the design, fabrication and assembly and regulatory compliance for off-site construction in general. ICC/MBI Standard 1200-2021: Standard for Off-Site Construction: Planning, Design, Fabrication and Assembly and ICC/MBI Standard 1205-2021: Standard for Off-Site Construction: Inspection and Regulatory Compliance provide criteria to facilitate off-site construction project compliance with building code requirements and support consistency across jurisdictions on how off-site construction is regulated.

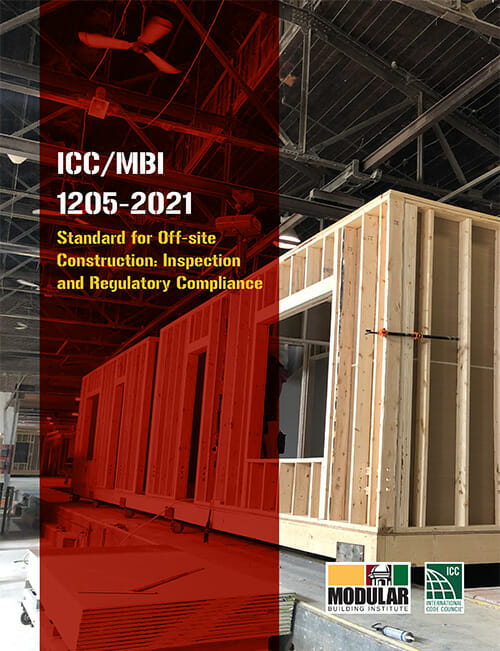
Building off these standards, ICC and MBI recognized needs or opportunities with respect to MEP systems and energy and water conservation in off-site construction. First, the factory environment presents an opportunity to test MEP systems in advance of assembly on-site. Second, the effective interconnection between panels or modules and with the site utilities is essential to achieving the benefits of off-site construction. Third, many off-site manufacturers, general contractors and trade subcontractors are focusing on delivering multi-trade mechanical systems assembled off-site. Finally, the U.S. Department of Energy’s National Renewable Energy Laboratory (NREL) has been doing research and testing to see how off-site construction can be leveraged to deliver both enhanced energy efficiency and reduced environmental impacts.
Introducing ICC/MBI 1210
In October 2021, ICC and MBI initiated work on a new standard—Standard 1210: Standard for Mechanical, Electrical, Plumbing Systems, Energy Efficiency and Water Conservation in Off-Site Construction. The standard’s development committee is made up of a diversity of interest categories including manufacturers, builders, government regulators, and designers. The committee meets frequently to identify provisions they feel should be covered by the standard. This content will be compiled into a draft document that is then open for public comment. The committee is assisted by working groups which include both committee and non-committee members.
The five current working groups mirror the main content of the standard’s scope—mechanical, electrical, plumbing, energy efficiency and water conservation. Anyone interested is encouraged to join the working groups.
To date, the committee has focused on construction documentation for MEP systems; the demonstration of compliance with existing code-related requirements including the International Building Code, International Plumbing Code, International Mechanical Code and the National Electrical Code; the identification, labeling and protection of system interconnections; and the provision of manufacturer installation instruction. With regard to energy conservation measures the continuity of air, vapor and water barriers and exterior insulation are of particular interest. The storage and staging of MEP off-site systems is also considered.
Building Off-Site Knowledge
One of the keys to expanding use of off-site construction is expanding familiarity within the building industry. The International Code Council has taken on the task of developing educational courses on off-site construction, not just for code officials but also for other members of the industry. The ICC Training Center features a specialty catalogue of classes with a specific focus on off-site construction.
The Introduction to Off-Site Construction course aims to demystify the many types of off-site construction from panelized systems like pre-cast concrete panels and structural insulated panel systems (SIPS) and volumetric systems like tiny houses, manufactured housing, pods, shipping containers and modules. With each system, the course includes information on where they are addressed in building codes, standards and other criteria.
Accompanying the release of ICC/MBI Standards 1200 and 1205 for off-site construction, a course introducing these standards and their content was developed. The course Introduction to Standards 1200 and 1205 provides a section-by-section discussion of the content of the standards to support their effective application by manufacturers, designers, code officials and third-party agencies.
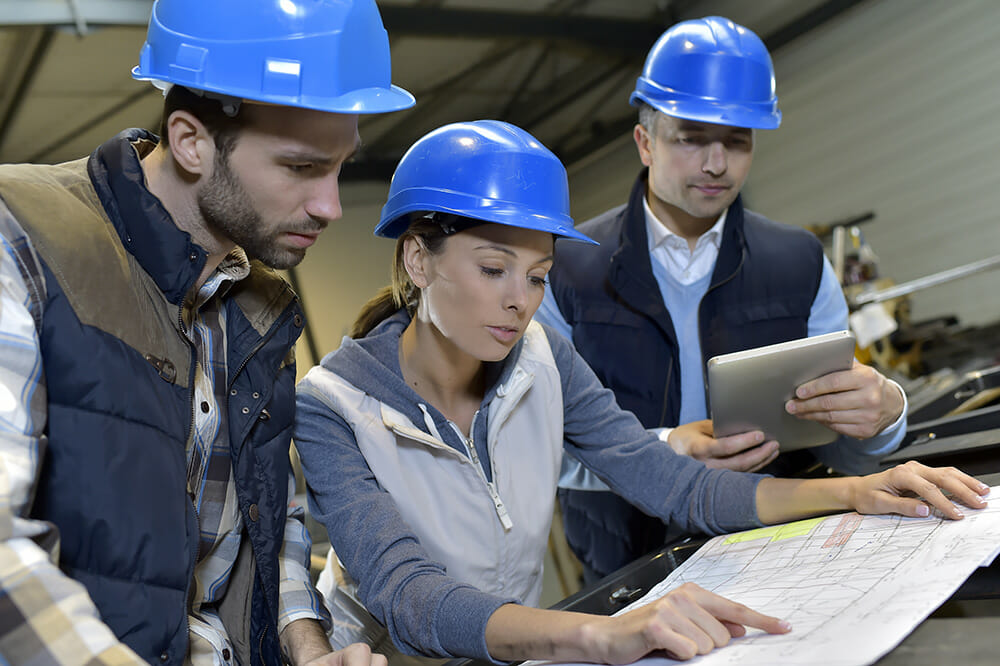
The Code Council and Modular Building Institute are in the process of creating a Credential of Learning Achievement (CLA) based on the introduction courses. By achieving the CLA, based on completing the courses and passing an exam, successful candidates will demonstrate their knowledge of the standards. The CLA is open to anyone, but may be of particular interest to code officials, third party agencies and manufacturers’ quality assurance personnel. It will be available by the end of 2022.
Additional courses are in development and will be added to the Training Center as they become available.
More from Modular Advantage
An Insider’s Guide to the 2025 World of Modular
The Modular Building Institute is bringing its global World of Modular (WOM) event back to Las Vegas, and with it comes some of the industry’s best opportunities for networking, business development, and education. Over the course of the conference’s four days, there will be numerous opportunities for attendees to connect, learn, and leverage event resources to get the most out of the conference.
Affordable Housing Now: The Industry’s Best Bring New Solutions to World of Modular
While the modular building industry has long known that it can be an effective solution to increase affordable housing, the word is slowly spreading to more mainstream audiences. Three presentations at this year’s World of Modular in Las Vegas hope to provide insight and direction for those seeking a real solution to the crisis.
Opportunities for Innovation in Modular Offsite Construction
Modular Offsite Construction has already shattered the myth that it only produces uninspired, box-like designs. Architectural innovations in module geometry, configurations, materials, and products make it possible to create visually stunning buildings without sacrificing functionality or efficiency.
Safe Modular Construction with Aerofilm Air Caster Transport
In collaboration with Aerofilm Systems, Heijmans developed innovative skids using air caster technology for moving modules easily and safely. These pallets are equipped with an auto-flow system, making operation extremely simple.
Miles, Modules, and Memes: Building a Modular Network One Flight at a Time
At the end of the day, social media is just another tool for building connections, and like any other tool, needs to be used skillfully to work properly. Use social media thoughtfully, and it will open doors to real opportunities and relationships you didn’t even see coming.
Falcon Structures: Thinking Inside the Box
Some of Falcon’s latest projects include creating container solutions for New York’s Central Park and an East Coast professional baseball team. More and more, Falcon is shipping out container bathrooms and locker rooms to improve traditionally difficult work environments, like those in oil and gas or construction.
UrbanBloc—From Passion to Industry Leader
UrbanBloc specializes in three main categories or markets – what they call “Phase 0” projects, amenities, and urban infill. Clients are often attracted to shipping containers because from a real estate perspective they are considered an asset. Having the flexibility to move and transport these assets allows owners to respond to different circumstances in a fluid manner that they can’t get with standard construction.
The Hospitality Game-Changer
“Hospitality is about more than just providing a service – it’s about delivering an experience,” says Anthony Halsch, CEO of ROXBOX. “And that’s where containers thrive. They allow us to create spaces that are unique, efficient, and sustainable.”
Container Conversions Counts on Simplicity to Provide Critical Solutions
Container Conversions has fabricated and developed thousands of containers for varied projects, including rental refrigeration options, offices, kitchens, temporary workplace housing, and mobile health clinics.
Revelution Containers and S. I. Container Builds: On a Mission to Revelutionize Housing
Rory Rubun and Pam Bardhi are on a mission to create more housing. Together, they plan to build shipping container eco communities similar to single-family subdivisions, and mixed-use buildings in urban settings. They also want to expand the footprint of ADUs across the nation.