Ralph Tavares: Family, Business, and Beaches
A look back (and forward) at the career of Ralph Tavares, MBI's 2022 Modular Construction Industry Hall of Fame inductee
Even before graduating from the Federal University of Rio de Janeiro in structural engineering, Ralph Tavares had found employment as a project and construction manager for high-rise condominium projects around Rio de Janeiro. One afternoon in 1978, he returned to the company office and found a newly hired trainee named Silvana sitting at his desk. He immediately asked her to marry him. Alas, she said no! (Fortunately, she later changed her mind.)
Both were hired onto the firm after receiving their college degrees. Ralph as an engineer, Silvana as an architect. When the Brazilian economy tanked in 1981, the company received some land as partial payment for the apartment buildings they sold. But they didn’t develop anything on it, so Ralph approached them and asked if he could build something on the land with materials they had left over from other projects. “They loved the idea and they were great clients. Silvana designed the houses, I did the engineering, and we built them. It’s much more common in Brazil than in the US to do design-build projects.” They built about two dozen single-family homes made with pre-fabricated concrete slabs, clay bricks, and pre-engineered wood roof trusses. “We quickly decided to fabricate the concrete slabs ourselves, and started a manufacturing business for forming the slabs and firing our own concrete masonry units for the walls,” Tavares says.
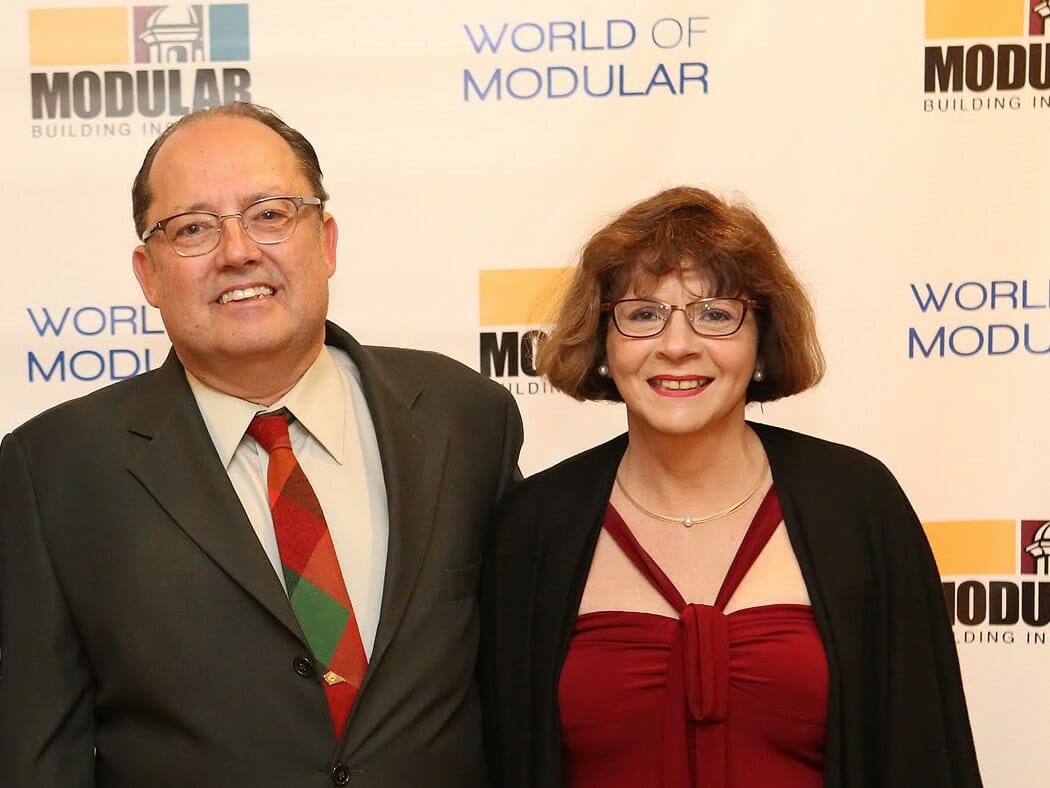
Ralph & Silvana Tavares, along many of their family members, are regular attendees of MBI's annual World of Modular conference and tradeshow.
Family Life
Tavares describes himself as an “army brat” growing up, frequently moving from place to place, following his father’s work as a high-ranking infantry army officer in the Brazilian military. When he and Silvana moved to the United States in 1987 with their two young children, he was not afraid to continue the habit of moving frequently. Although it was hard for their children at times, Tavares says that they now appreciate the perspective it gave them — they eventually came to feel confident that they could move anywhere and make new friends in a new place.
The Tavares family first lived on the east coast (including in New York and Connecticut all the way south to Florida) before eventually ending up on the west coast, in California — after a brief period in the Midwest. Speaking of when the family lived in Kansas City, Tavares says, “The drive to Galveston was over ten hours away. I didn’t realize until I lived in Kansas how much I loved the ocean.” He used to body surf and play soccer on the beach every day growing up. Now, he’s more likely to be found simply enjoying the fresh air, walking on the beach with Silvana, eating seafood, or lying in the shade with a book. “I like to travel, I love wine, and I enjoy cooking. I’m not a chef but I can handle a kitchen. My travel destinations are usually places where I can find great food and great wine.”
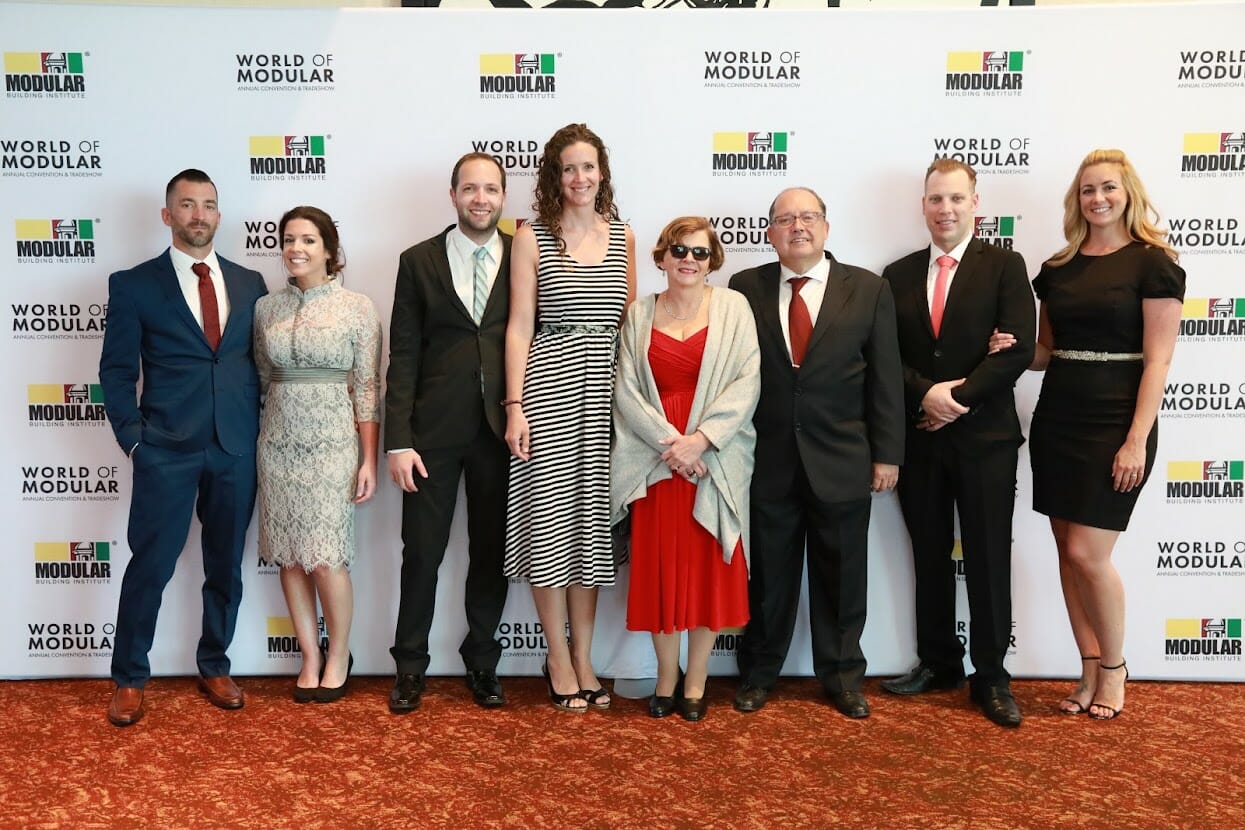
Ralph Tavares and his family at the 2022 World of Modular.
Ralph and Silvana founded R & S Tavares Associates in California in 2002 and Tavares recalls that some of the early projects they worked on were schools and clinics — and a large training center for a military base in Arizona. “It was a really ugly building, with no windows, but very high tech and high security so they could play combat simulations inside. The quantity of fiber optics cables and computers was similar to what you’d see in a data center.” Tavares has no photos of the interior of the building because after it was installed, his firm didn’t have clearance to visit it because of the high security at the base.
Family Business
Growing up, the Tavares kids spent summers working at the family business and enjoyed it. “It meant my wife and I could keep them close, keep them on a short leash, and keep our eyes on them,” Ralph says with a laugh.
His son, Pedro, initially went to college to study computer graphics and animation. “But he came back to us and he now has a Master’s Degree in Real Estate Development for Architects and he’s in the process of getting his architectural license.” His daughter, Mariana, is a business major and worked for a number of different companies before deciding that she wanted to return to help out with the family firm too. “She said we didn’t even have to pay her,” Tavares says, “but of course we did!”
Tavares says he is a very calm person. “I'm not hard to work with. I give my son and daughter — all my employees — enough rope to hang themselves,” he jokes. “I don’t need to point out mistakes, because they can very quickly recognize their own mistakes themselves, which is the best way to avoid repeating them. We’re all learning every day how to do things better.” He adds that he’s constantly amazed by the number of family businesses among the MBI membership. “We fit in well and my family greatly enjoys the MBI family environment.”
Volunteerism
Tavares believes it’s important to share knowledge and to volunteer for organizations that help improve the industry for everyone. And his knowledge and experience in the industry is extensive. As well as being an engineer, Tavares is also a licensed building inspector and general contractor. A nice side effect of volunteering is that Tavares meets people in the industry who become clients or who refer clients to him. He’s been on the MBI board in the past, and is currently serving on the board again, and has volunteered for various Task Forces, taught courses, and helped to write regulations. He has been a Trustee of the MBI Educational Foundation for a long time. Recently, he worked with MBI and the International Code Council on the regulations for container-built structures and for two ICC Standards to be inserted in the code.
He's now part of the Task Force developing the Standard for Mechanical, Electrical, Plumbing Systems, Energy Efficiency and Water Conservation in Off-Site Construction, to be released in 2023-2024. Even when he didn’t have a lot of staff and was working long hours, he helped out. “Now I have a little bit more time, it’s easier to help,” Tavares says.
As well as volunteering with MBI, he’s also been volunteering with the Rotary Club for over twenty years. Every year — except during the pandemic — he and Silvana go to Mexico with a group of volunteers to do things like re-painting a school, repairing their HVAC system, or installing a playground. “In each school we work on, we organize a clinic for the needy neighborhood. We bring medical and veterinary staff to run the clinic for a few days.”
Success in Business
One of Tavares’ “secrets to success” in business is that his clients are more than clients — they’re friends. “They know they can call me and I’ll help them solve whatever problem they’re having.” His company gets repeat business because they are problem solvers, like a challenge, do good work, and have good relationships. “We don’t do much marketing. Most of our work comes through word-of-mouth and I meet people at the MBI conference every year.” Well, to be honest, he’s missed it twice in two decades — and one of those times was because the date conflicted with his daughter’s wedding.
“It’s also helped our business to have a wide reach. We’re licensed in almost every state in the US. Recessions don’t always hit every region to the same extent at the same time,” Tavares explains. “So when things are bad in California, they might be OK on the East Coast or vice versa.”
Thoughts on the Modular Construction Industry
More people are realizing that modular construction is much faster than conventional construction and that it’s high quality. “For example, hotel chains realize they can open new hotels faster. So even if the price per square foot is the same as conventional construction, they understand the financial benefits of speed — saving on general conditions and generating revenue sooner.”
Tavares says, “I’ve been in this industry for over 35 years, and I’ve seen it skyrocket lately. I’ve never seen before the level of interest we have now.” So the demand is there. However, he says persistent problems are labor and training and that the “building codes need to be more friendly to modular construction, and we’re trying to make that happen.”
The only negative thing Tavares has to say about the modular industry is, “It makes me sad when I see a modular company fail.” He explains that it’s frustrating to see a company have good intentions, hire lots of smart, talented people, get lots of investment money — but not apply that money correctly. “If they don’t understand construction, don’t do their homework, and don’t get good advice, they fail. And I like everyone in the industry to succeed because it makes all of us stronger.”
Final Thoughts
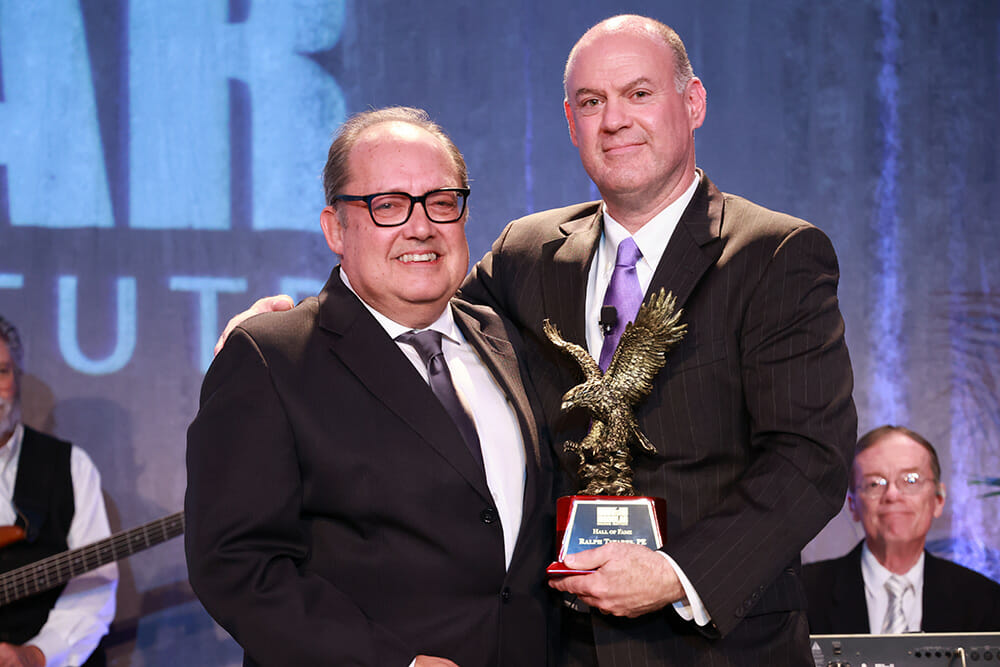
Ralph Tavares accepts MBI's 2022 Hall of Fame Award at the 2022 World of Modular.
A Few Favorite Projects
Appalachian State University Dorms in Boone, NC
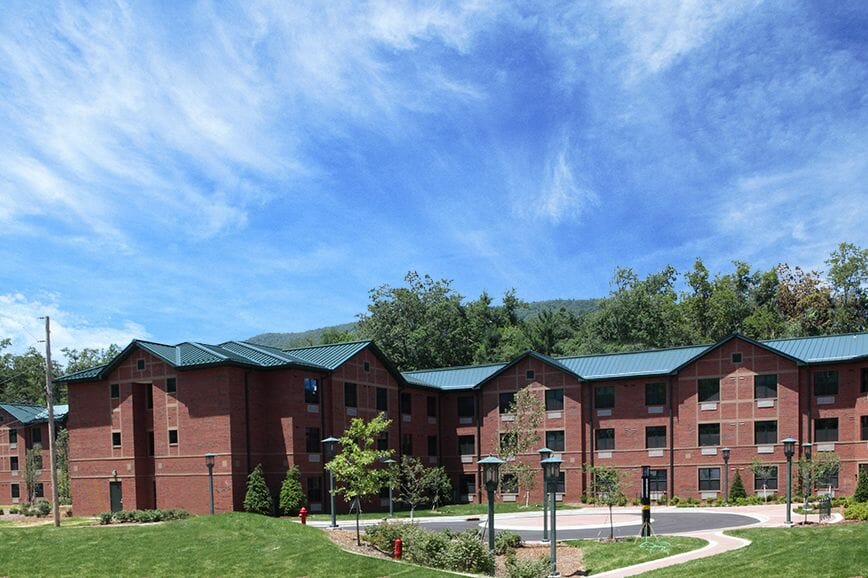
Four stories, 120,000 sq. ft., hybrid of site-built and off-site components, LEED Gold, accommodates 450+ students. Room modules were constructed by Clayton Homes. Significant site retaining walls, precast concrete foundations. Took three months from foundation excavation to roof installation on the modules.
Mercy Hospital in Joplin, MO
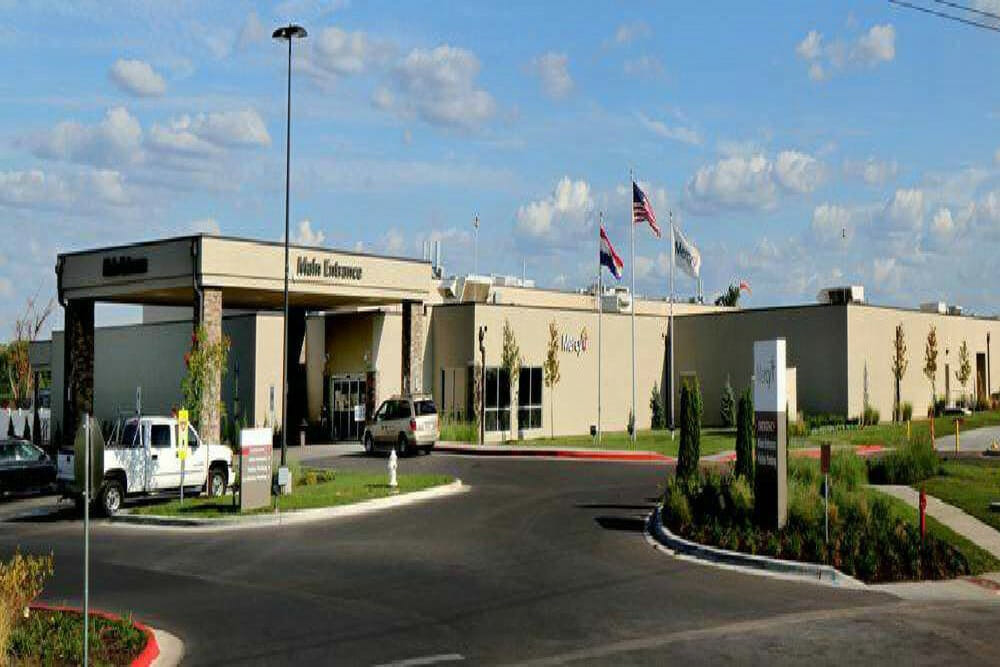
Two stories, 150,000 sq. ft. interim facility to replace hospital destroyed in a tornado in May, 2011. The goal was to build a new hospital within a year and it ended up being designed and built in 8.5 months — by using 224 steel modules manufactured in California. It was the quickest acute care hospital of its size to be constructed in the US — while of course meeting the strict requirements of the International Building Code.
Hope on Alvarado in Los Angeles, CA
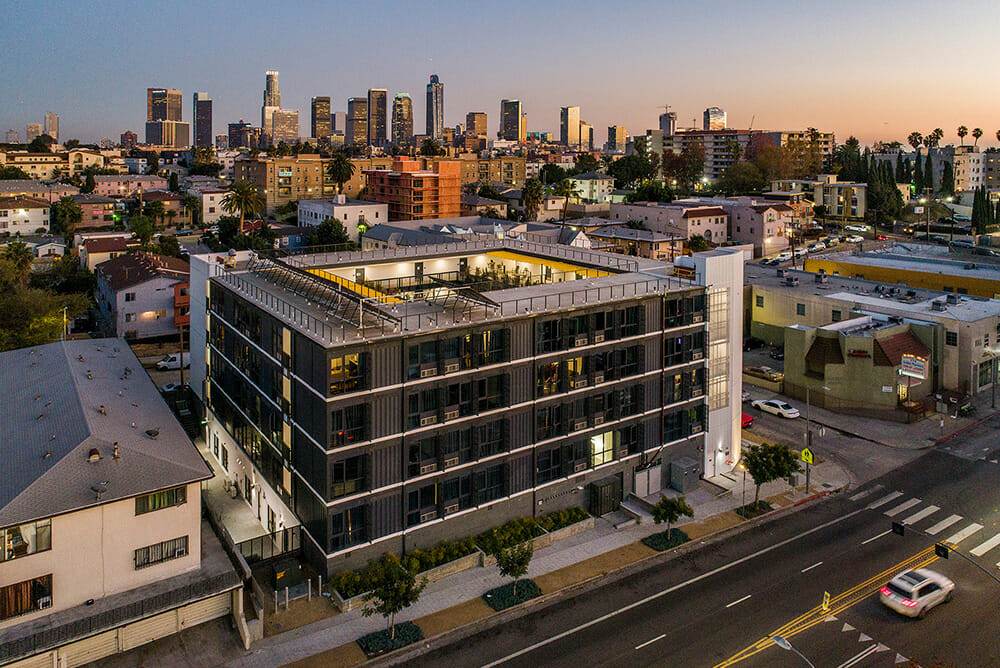
Five stories, 84 self-contained 400 to 480 sq. ft. micro-apartments complete with kitchens and bathrooms. Initially designed to be made from shipping containers, it switched to purpose-built steel modules. It provides permanent supportive housing for those transitioning from homelessness, plus offices for onsite support staff. Includes shared outdoor and indoor spaces for cooking and eating together, watching TV, and playing foosball.
Three on Abbott in San Diego, CA
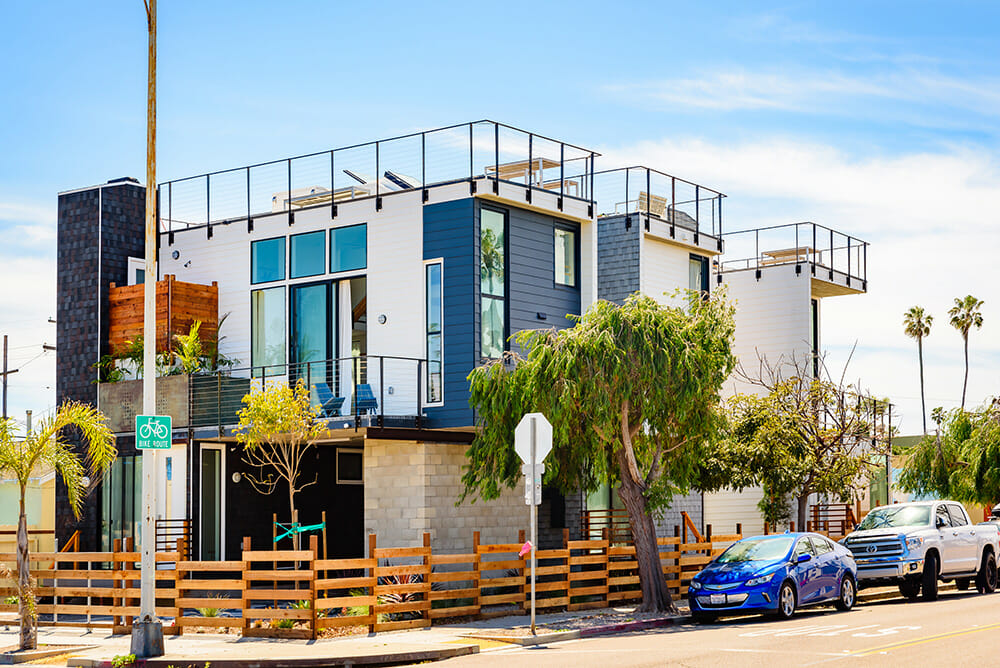
Three detached prefabricated home development a block from the beach in San Diego. Ralph and Pedro’s first effort at developing a project after Pedro completed his Master’s Degree in Real Estate Development for Architects. The project includes modules with balloon-framed lofts, which had to be shipped on special trailers due to being over 15 ft. high. Ralph and Pedro still own the homes as short-term rentals.
“To be inducted into the MBI Hall of Fame is a great honor. I feel like I can retire now and not do anything else,” Tavares says with a smile, knowing that’s not going to happen. More seriously, he adds, “Receiving this award really brings me joy. I have to thank my wife, my family, and my staff who always supported me and worked by my side, and the awesome friends that I have in this industry.”
About the Author: Zena Ryder is a freelance writer, specializing in writing about construction and for construction companies. You can find her at Zena, Freelance Writer or on LinkedIn.
More from Modular Advantage
Oregon’s Prevailing Wage Proposal: A Wake-Up Call for Modular Construction
Should House Bill 2688A become law, building projects would increase in price, face longer completion timelines, and produce significantly more waste. The bill also incentivizes contract awards to out of state businesses who would not reinvest their earnings into the local Oregon economy.
Behind the Design of Bethany Senior Terraces, NYC’s First Modular Passive House Senior Housing Project
As more developers seek to meet new regulations for energy efficiency, the team at Murray Engineering has set a new record. With the Bethany Senior Terraces project, Murray Engineering has helped to develop NYC’s first modular structure that fully encompasses passive house principles — introducing a new era of energy efficiency in the energy-conscious city that never sleeps.
How LAMOD is Using Modular to Address Inefficiency, Sustainability, and the Future of Construction
As developers, designers, and contractors seek to understand the evolving needs of the modular industry, no one is as well-versed in the benefits of going modular as Mārcis Kreičmanis. As the co-founder and CBDO of LAMOD in Riga, Latvia, Mārcis has made it his ultimate goal to address the inefficiencies of traditional construction.
From Furniture Builder to ‘Activist Architect’: Stuart Emmons’ Unique Journey
Stuart Emmons was fascinated by buildings at a young age. He remembers building sand cities with his brother during trips to the Jersey shore. His father gave him his first drawing table at the age of ten. Today, he is an experienced architect who received his FAIA in June 2025. The road he took is unique, to say the least.
Forge Craft Architecture + Design: Codes, Contracts, and Intellectual Property
Founding Principal and Director of Modular Practice for Forge Craft Architecture + Design, Rommel Sulit, discusses the implications of codes, contracts, and intellectual property on
modular construction.
Eisa Lee, the “Bilingual” Architect
Now as the founder of XL
Architecture and Modular Design in Ontario, Canada, she applies not just her education as a traditional architect but an entire holistic view on modular design. It’s this expansive view that guides her work on being a true partner that bridges the gap between architects and modular factories as they collaborate on the design process.
Tamarack Grove Engineering: Designing for the Modular Sector
The role of a structural engineer is crucial to the success of a modular project, from initial analysis to construction administration. Tamarack Grove offers structural engineering services — project analysis, plan creation, design creation, and construction administration — for commercial, manufacturing, facilities, public services, and modular. Modular is only one market sector the company serves but it is an increasingly popular one.
Engineer Masters the Art of Listening to His Customers
Since founding Modular Structural Consultants, LLC. in 2014, Yurianto has established a steady following of modular and container-based construction clients, primarily manufacturers. His services often include providing engineering calculations, reviewing drawings, and engineering certification
Inside College Road: Engineering the Modules of One of the World’s Tallest Modular Buildings
College Road is a groundbreaking modular residential development in East Croydon, South London by offsite developer and contractor, Tide, its modular company Vision Volumetric (VV), and engineered by MJH Structural Engineers.
Design for Flow: The Overlooked Power of DfMA in Modular Construction
Unlocking higher throughput, lower costs, and fewer redesigns by aligning Lean production flow with design for manufacturing and assembly.