Modular Research and Real World Results
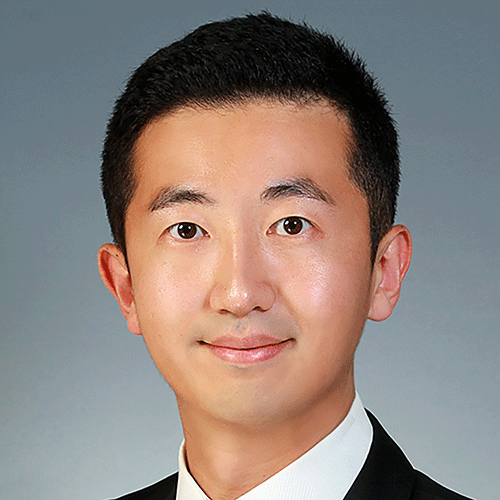
Dr. Jin Ouk Choi is an Assistant Professor of Civil & Environmental Engineering & Construction at the University of Nevada, Las Vegas (UNLV). He has research and industry experience in modular construction, standardization strategy, construction engineering, and construction management.
Dr. Jin Ouk Choi has published dozens of academic articles and conducted numerous research studies on modular construction. He’s an academic advisor for the Construction Industry Institute’s [CII] Modularization Community for Business Advancement.
Choi says many stakeholders don’t fully understand the differences between modular and conventional construction. “It sounds very simple and obvious. But, on a modular project, there are so many things that need to be planned and executed differently from conventional construction,” he says. “Many failed modular projects showed that they have failed to execute their modular projects differently or implement the critical success factors.”
Some of Choi’s research has investigated the links between “modularization Critical Success Factors and performance of industrial modular projects.” A Critical Success Factor (CSF) is defined as something necessary for achieving success on modular construction projects. Choi and his colleagues have identified 21 CSFs.
An article co-written by Choi, which appeared in the Journal of Construction Engineering and Management, describes the five most important CSFs as follows:
- Module Envelope Limitations: Preliminary transportation evaluation should result in understanding module envelope limitations.
- Alignment on Drivers: Owner, consultants, and critical stakeholders should be aligned on important project drivers as early as possible in order to establish the foundation for a modular approach.
- Owner’s Planning Resources & Processes: As a potentially viable option to conventional stick-building, early modular feasibility analysis is supported by owner’s front-end planning and decision support systems, work processes, and team resources support. Owner comfort zones are not limited to the stick-built approach.
- Timely Design Freeze: Owner and contractor are disciplined enough to effectively implement timely staged design freezes so that modularization can proceed as planned.
- Early Completion Recognition: Modularization business cases should recognize and incorporate the economic benefits from early project completion that result from modularization and those resulting from minimal site presence and reduction of risk of schedule overrun.
Choi says many stakeholders don’t fully understand the differences between modular and conventional construction. “It sounds very simple and obvious. But, on a modular project, there are so many things that need to be planned and executed differently from conventional construction,” he says. “Many failed modular projects showed that they have failed to execute their modular projects differently or implement the critical success factors.”
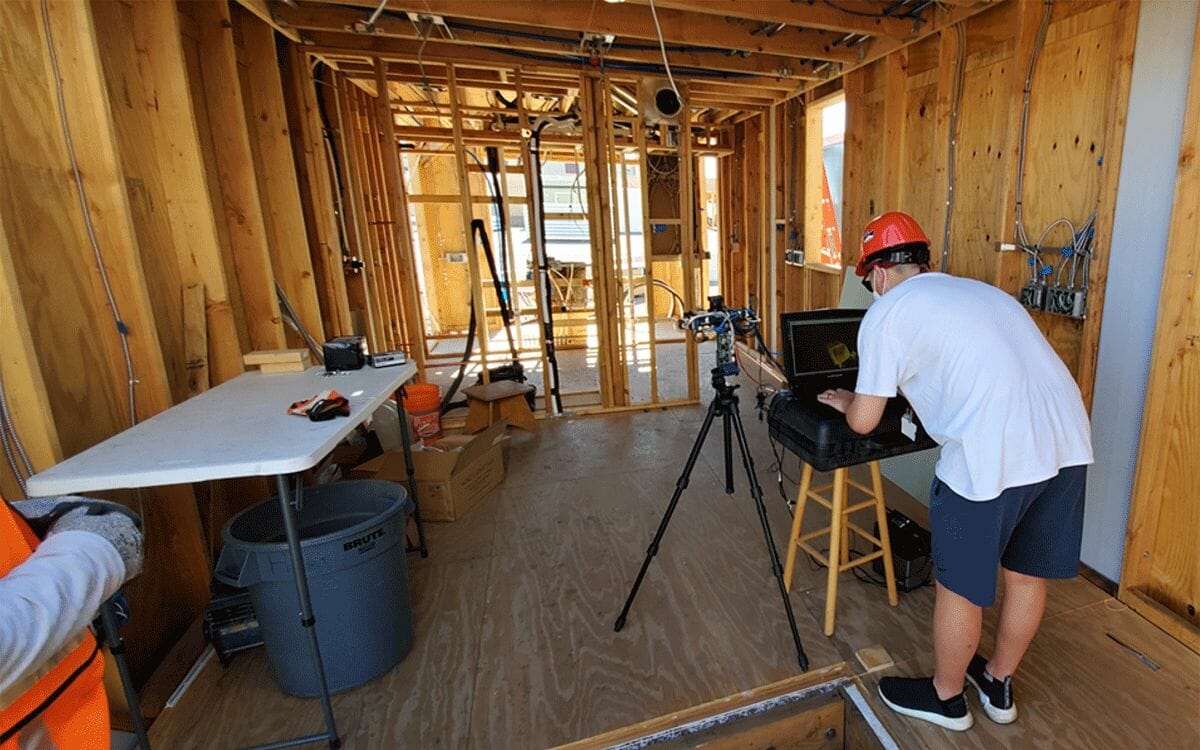
Dr. Choi partnered with students from University of Nevada, Las Vegas to design and construct a net-zero home for the 2020 Solar Decathlon. The team placed third in the nation. Read more about the team's solar-powered entry below.
Education
Everyone from homeowners to major property developers need educating about modular construction, Choi says. “The public having the wrong impression of modular buildings — as being poor quality and too similar to one another — is a major barrier to the industry.”
But, perhaps even more importantly, students in architecture, construction management, engineering, and so on need to be educated about modular construction so that future modular projects have a greater chance of success. “Barely any architecture or engineering programs have courses on modular construction. Very few professors in the United States can teach it,” Choi says. His view is that the education system will continue teaching conventional, stick-building approaches until there is enough industry influence and investment. “Currently, people don’t have the necessary education in modular construction, which means training staff at modular companies and executing projects will take more time and be more costly,” he says.
As well as teaching students about modular construction, Choi also maintains the importance of primary research and innovation, with collaboration between industry and academia. “In the past, studies have mostly been limited to surveys, which identify perceptions of risks and advantages,” Choi says. “But we really need more rigorous, systemic, evidence-based studies.”
He has a call-to-action, a request to MBI to facilitate alliances between the modular industry and academia. “Industry alliances — similar to those at the CII, based at the University of Texas at Austin — can lead future generations into the industry with a positive influence for businesses.”
Related Listening:
Exploring the Critical Success Factors of Modular Construction w/ UNLV's Dr. Jin Ouk Choi
In this episode of Inside Modular, Dr. Jin Ouk Choi, assistant professor at the University of Nevada, Las Vegas, discusses his research into the critical success factors (CSFs) of modular construction projects and identifies the key CSFs that modular stakeholders should be utilizing. Dr. Choi also discusses the benefits large modular companies are seeing from incorporating these CSFs into their projects.
The Greatest Potential
Choi believes the residential sector — both multi- and single-family buildings — has the most potential for modular construction. Lack of housing supply is driving prices up so there’s very little affordable housing available, and the problem is not going away soon. “The construction industry doesn’t have enough workers to deliver enough houses to meet the demand and the labor shortage problems will last for a while, or even become worse.”
As a result, developers will be pushed to consider modular construction or even be forced to implement it, Choi says. “This will provide sufficient orders to GCs and fabricators to get the economies of scale that will really cut their prices. And that will be the tipping point for modular construction. I really hope all the stakeholders in the modular industry will be ready for that!”
Modular manufacturers “need to have sufficient knowledge and experience so they can provide the same or higher quality than stick-built homes at a lower price. They need the infrastructure, technology, and methods to mass-produce. And they also need to be able to provide sufficient variation or customization, especially for single-family homes,” Choi says. But he doesn’t think that’s too difficult for the industry to achieve. “In my view, just having some combinations of standardized designs, and being able to change the layouts, will deliver sufficient variation to the residential market. There are stick-building companies providing standardized but customizable designs.”
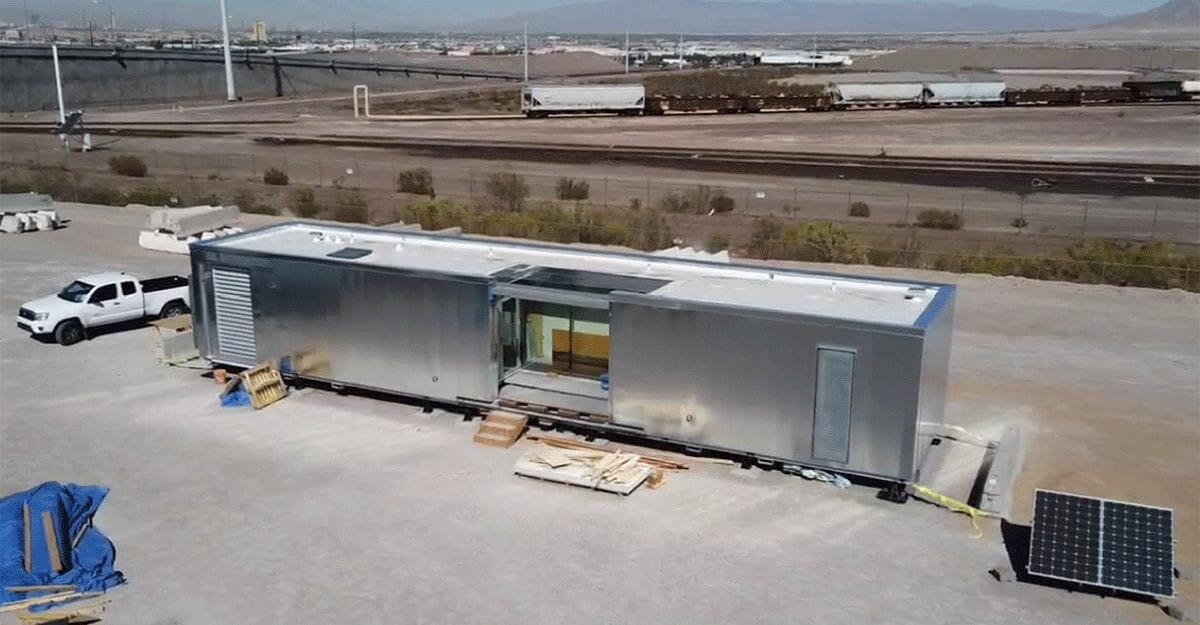
Seen here during its construction, "Mojave Bloom creates an oasis from the bustling downtown of Las Vegas and the Mojave Desert's harsh environment. Designed to be a place of healing for veterans suffering the effects of wartime trauma, the home connects the resident to their environment through a carefully orchestrated procession of sensory experiences," according to its website.
The Mojave Bloom Project
The Solar Decathlon is a two-year design-build competition run by the U.S. Department of Energy. First held in 2002, the collegiate competition involves 10 contests, challenging student teams to design and build high-performance, low-carbon buildings powered by renewable energy. In the United States alone, more than 25,000 students in 790+ collegiate teams have participated in the competition.
Choi was thrilled when the team from UNLV won third place for their entry, Mojave Bloom, a net-zero modular house. It was designed and fabricated from scratch by UNLV students at the Xtreme Cubes plant in Henderson.
Choi was asked to join the team as a subject matter expert in modular construction and construction management. He was co-principal investigator and co-engineering advisor for the team. “At any given time during the 2-year competition, we had more than 50 students working on the project. They were from different majors, including civil engineering, mechanical engineering, architecture, construction management, and computer science.”
On the Mojave Bloom project, Choi “implemented many new technologies, such as 4D scheduling with Procore, sensors, a drone, immersive virtual reality, 3D point clouds, LiDAR, and so on.”
The entire project was closely monitored and documented, and in his presentation at the 2022 World of Modular Choi will present the lessons learned, focusing on the results obtained from the innovative technologies. “The students did an excellent job, but I will talk about where the team made mistakes. New or inexperienced modular companies can learn from our failures and avoid them,” Choi says. “I think these stories will entertain the conference participants.”
About the Author: Zena Ryder is a freelance writer, specializing in writing about construction and for construction companies. You can find her at Zena, Freelance Writer or on LinkedIn.
More from Modular Advantage
Oregon’s Prevailing Wage Proposal: A Wake-Up Call for Modular Construction
In early February, 2024, the Massachusetts Board of Building Regulations and Standards (BBRS) released its proposed 10th Edition building codes. This draft included several amendments targeting modular construction that would have created an extremely difficult environment for the entire modular industry and could have eliminated the industry entirely in the state.
Behind the Design of Bethany Senior Terraces, NYC’s First Modular Passive House Senior Housing Project
As more developers seek to meet new regulations for energy efficiency, the team at Murray Engineering has set a new record. With the Bethany Senior Terraces project, Murray Engineering has helped to develop NYC’s first modular structure that fully encompasses passive house principles — introducing a new era of energy efficiency in the energy-conscious city that never sleeps.
How LAMOD is Using Modular to Address Inefficiency, Sustainability, and the Future of Construction
As developers, designers, and contractors seek to understand the evolving needs of the modular industry, no one is as well-versed in the benefits of going modular as Mārcis Kreičmanis. As the co-founder and CBDO of LAMOD in Riga, Latvia, Mārcis has made it his ultimate goal to address the inefficiencies of traditional construction.
From Furniture Builder to ‘Activist Architect’: Stuart Emmons’ Unique Journey
Stuart Emmons was fascinated by buildings at a young age. He remembers building sand cities with his brother during trips to the Jersey shore. His father gave him his first drawing table at the age of ten. Today, he is an experienced architect who received his FAIA in June 2025. The road he took is unique, to say the least.
Forge Craft Architecture + Design: Codes, Contracts, and Intellectual Property
Founding Principal and Director of Modular Practice for Forge Craft Architecture + Design, Rommel Sulit, discusses the implications of codes, contracts, and intellectual property on
modular construction.
Eisa Lee, the “Bilingual” Architect
Now as the founder of XL
Architecture and Modular Design in Ontario, Canada, she applies not just her education as a traditional architect but an entire holistic view on modular design. It’s this expansive view that guides her work on being a true partner that bridges the gap between architects and modular factories as they collaborate on the design process.
Tamarack Grove Engineering: Designing for the Modular Sector
The role of a structural engineer is crucial to the success of a modular project, from initial analysis to construction administration. Tamarack Grove offers structural engineering services — project analysis, plan creation, design creation, and construction administration — for commercial, manufacturing, facilities, public services, and modular. Modular is only one market sector the company serves but it is an increasingly popular one.
Engineer Masters the Art of Listening to His Customers
Since founding Modular Structural Consultants, LLC. in 2014, Yurianto has established a steady following of modular and container-based construction clients, primarily manufacturers. His services often include providing engineering calculations, reviewing drawings, and engineering certification
Inside College Road: Engineering the Modules of One of the World’s Tallest Modular Buildings
College Road is a groundbreaking modular residential development in East Croydon, South London by offsite developer and contractor, Tide, its modular company Vision Volumetric (VV), and engineered by MJH Structural Engineers.
Design for Flow: The Overlooked Power of DfMA in Modular Construction
Unlocking higher throughput, lower costs, and fewer redesigns by aligning Lean production flow with design for manufacturing and assembly.