Hacking Construction and Making it Greener at BOXY
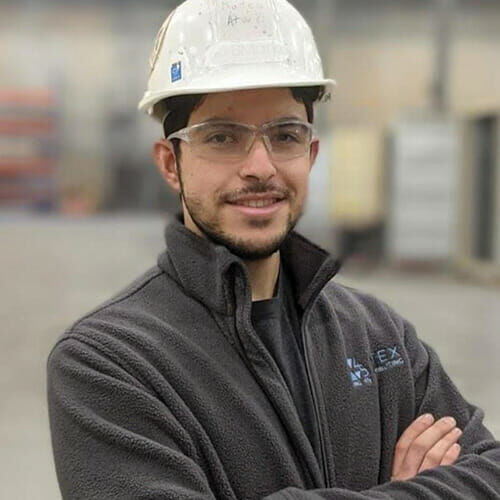
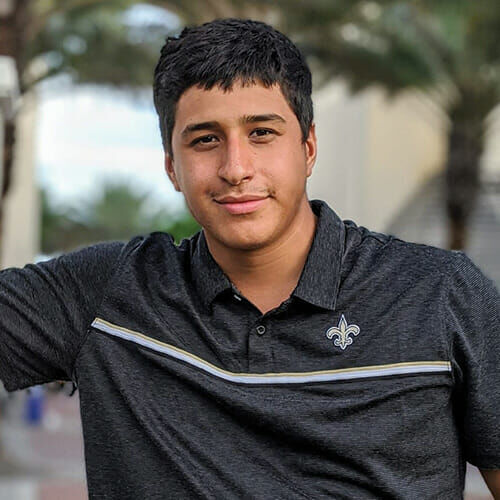
Mateo and Tiago Atwi are the CEO and COO, respectively, of Louisiana-based BOXY LLC.
Born and raised in Louisiana, young brothers, Mateo and Tiago Atwi, are eager to — as they put it — “hack the construction industry”. Not in the layperson’s sense of criminal hackers who exploit cyber-security weaknesses, but in the sense commonly used in the tech world: Overcoming obstacles in creative, non-standard ways in order to achieve surprising results.
They’re putting the hacker mentality into practice to come up with solutions to problems the construction industry may not have even realized were problems. “There are different ways to hack the sales cycle, designing, estimating, procurement, materials, labor — all the steps of a project,” Mateo says. “Instead of doing things the same way, let’s be creative and find new, sustainable ways to achieve better results both during construction and afterwards.”
The brothers founded BOXY just last year and the company is currently finishing a rural health clinic in Louisiana, built with cold-formed steel modules. It’s a five-room, 1500 square feet expansion of an existing clinic. “The design is a little different from what’s typical. In volumetric construction, you usually have a lot of redundant back-to-back walls,” says Mateo. “Instead, we put a panelized hallway between our pre-finished modules so that all the module walls are separated and useful. We’re building the roof on-site.”
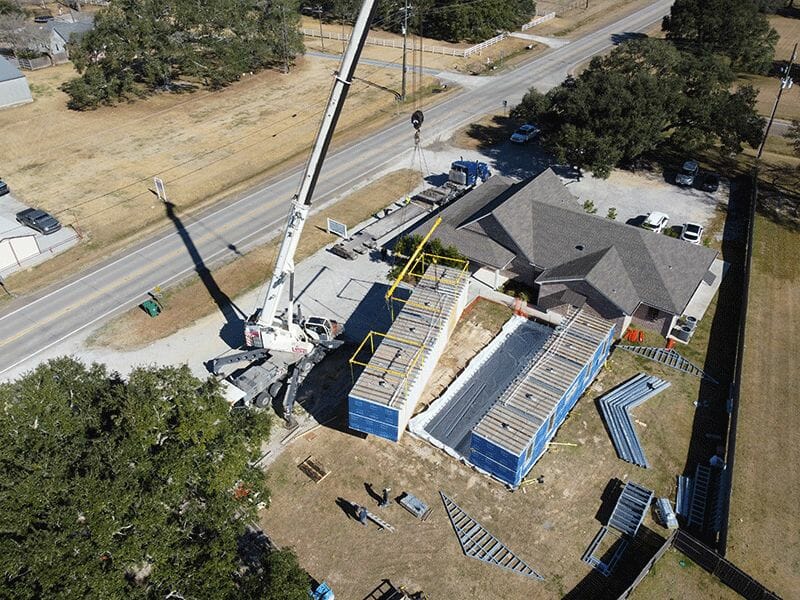
BOXY’s two-module rural health medical clinic project being set in Church Point, Louisiana. Since rural health clinics go to remote places, it makes sense to build them in metro areas and ship them.
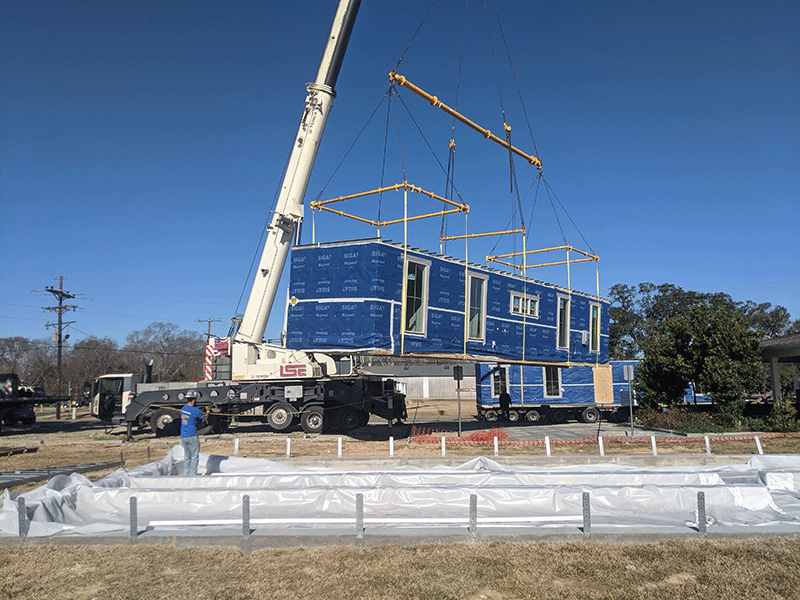
Elaborate rigging is required to minimize the bending in the modular cold formed steel units. This 52’ unit has five straps from a modular lift system manufactured by Modulift.
For this project, they had difficulty finding a general contractor who was knowledgeable about installing modules and who was interested in performing the relatively small project. So they acted as general contractors themselves, which also satisfied their desire to control the whole process from beginning to end.
First Tastes of Prefabricated Construction
Before founding BOXY, both brothers gained experience at BMarko Structures, a modular manufacturing company in Georgia. They also had experience with other kinds of prefabrication and manufacturing.
Mateo went to Georgia Tech to study mechanical engineering, graduating in 2019. He had two internships at NASA’s Johnson Space Center in Texas and also interned at a jewelry manufacturer in Louisiana. During this time, he was exposed to lots of R&D and manufacturing. After graduating, Mateo worked in various positions at BMarko, including Vice President of Operations.
Graduating in 2018, Tiago also studied mechanical engineering, along with math, at the University of Louisiana at Lafayette. His primary interest is sustainability, and he’s worked with renewable energy companies in Spain and in Texas. His first taste of prefabrication was as the Field Engineer for a wind farm project about two hours from Austin. “It was so fast and efficient. We stacked all the components for 110 wind turbines and assembled them on-site. It took four months to build a wind farm to generate enough power for 400,000 households,” Tiago says.
He then saw the work Mateo was doing with upcycled shipping containers at BMarko. “It was the same kind of idea. Taking factory-manufactured components and assembling them on-site. If you can figure out the logistics and the crane system, it’s such an efficient way to build.”
Tiago joined Mateo at BMarko for a few months before the pair decided to move back home to Louisiana to found their own modular company.
Sustainability
Tiago notes that there are numerous factors influencing the carbon impact of construction, such as “the materials used, waste generated, subcontractors driving to the site” and so on. Over a building’s lifecycle, “the insulation and how air-tight it is makes a difference to how much energy the building uses. And the materials you use makes a difference to how long the building lasts. Offsite construction is effective for really optimizing the specifics to reduce buildings’ carbon impact,” Tiago says.
An important consideration is how durable a building is, and that can depend on where it’s located. “During construction, you may not see a big difference in carbon impact between building with wood and building with steel,” Mateo says. “But here in Louisiana, the base flood elevations are very high, so there are issues with termites and rot in wooden buildings. So, in this environment, steel buildings are more durable. Wooden buildings are more wasteful because they have to be demolished and re-built sooner.”
Part of BOXY’s agenda is to design to meet passive house standards, with better building envelopes and insulation, thus reducing energy usage over a building’s lifecycle.
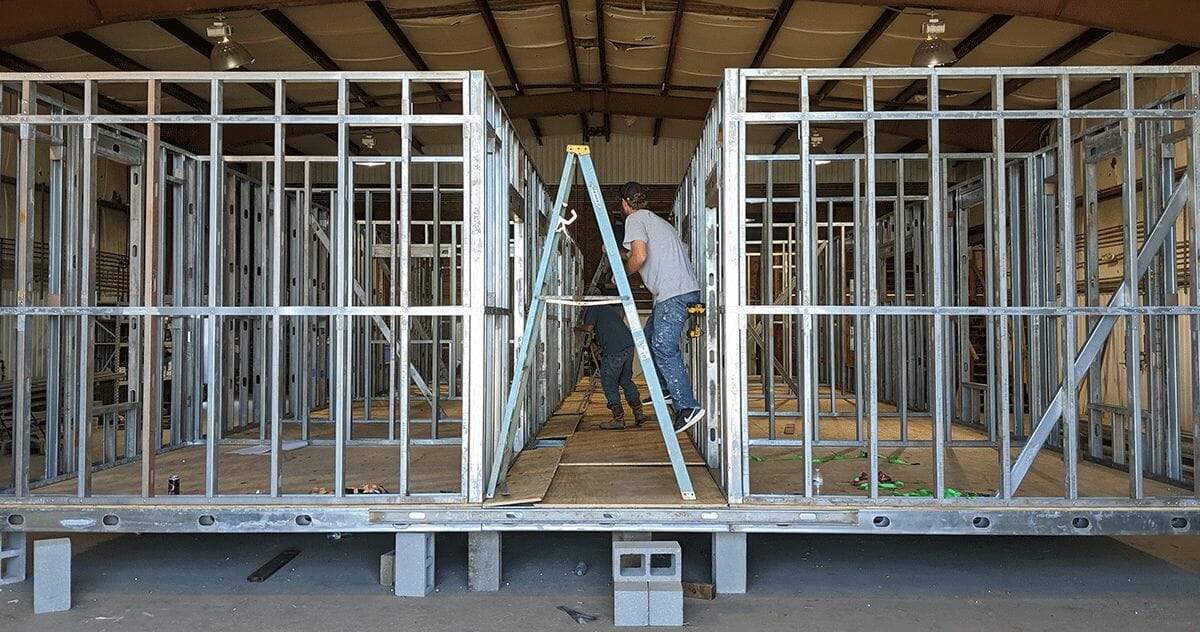
Construction as Manufacturing
At the broadest level, the Atwis’ goal for BOXY is “to have a big, positive impact for the people who work in the construction industry, now and in the future,” Mateo says. “And also for the people who live and work in the buildings.” To achieve these big goals, Mateo says their strategy is to “design buildings with repeatable systems, and bring manufacturable elements to construction.” They’re doing this in a number of ways:
- Using manufacturing processes like CNC roll-forming that are design-driven (in contrast with labor-driven on-site processes).
- Creating an engineering library of repeatable designs that have been tested through execution.
- Designing repeatable framing kits with a Revit plugin, AGACAD.
- Creating software and setting up a website, usframefactory.com, for stud and track sales where customers can get instant pricing and lead times on custom framing materials.
Hacking the Sales Cycle is Greener
One example of hacking the construction industry is re-thinking how buildings are sold. “The sales cycle doesn’t have to mean a lot of time spent on the phone or emailing. We’re hacking the sales cycle by selling materials, such as metal track and studs, and frame kits online,” Mateo says.
Not only does this online ordering system save customers’ time, it also reduces waste. Because BOXY doesn’t charge any additional fees for ordering custom lengths, customers can order the exact amount they need. “This means subcontractors can remove the normal 10-15% waste factor they typically include,” Mateo explains. “There’s a significant amount of embodied carbon in wasted materials, so reducing waste helps reduce the carbon impact of the building. At the end of the day, it also saves the subcontractor and their client money.”
World of Modular Presentation
In their World of Modular presentation, Mateo and Tiago Atwi will delve into more detail about how the construction industry can learn from the software industry and apply some of its practices
About the Author: Zena Ryder is a freelance writer, specializing in writing about construction and for construction companies. You can find her at Zena, Freelance Writer or on LinkedIn.
More from Modular Advantage
Oregon’s Prevailing Wage Proposal: A Wake-Up Call for Modular Construction
Should House Bill 2688A become law, building projects would increase in price, face longer completion timelines, and produce significantly more waste. The bill also incentivizes contract awards to out of state businesses who would not reinvest their earnings into the local Oregon economy.
Behind the Design of Bethany Senior Terraces, NYC’s First Modular Passive House Senior Housing Project
As more developers seek to meet new regulations for energy efficiency, the team at Murray Engineering has set a new record. With the Bethany Senior Terraces project, Murray Engineering has helped to develop NYC’s first modular structure that fully encompasses passive house principles — introducing a new era of energy efficiency in the energy-conscious city that never sleeps.
How LAMOD is Using Modular to Address Inefficiency, Sustainability, and the Future of Construction
As developers, designers, and contractors seek to understand the evolving needs of the modular industry, no one is as well-versed in the benefits of going modular as Mārcis Kreičmanis. As the co-founder and CBDO of LAMOD in Riga, Latvia, Mārcis has made it his ultimate goal to address the inefficiencies of traditional construction.
From Furniture Builder to ‘Activist Architect’: Stuart Emmons’ Unique Journey
Stuart Emmons was fascinated by buildings at a young age. He remembers building sand cities with his brother during trips to the Jersey shore. His father gave him his first drawing table at the age of ten. Today, he is an experienced architect who received his FAIA in June 2025. The road he took is unique, to say the least.
Forge Craft Architecture + Design: Codes, Contracts, and Intellectual Property
Founding Principal and Director of Modular Practice for Forge Craft Architecture + Design, Rommel Sulit, discusses the implications of codes, contracts, and intellectual property on
modular construction.
Eisa Lee, the “Bilingual” Architect
Now as the founder of XL
Architecture and Modular Design in Ontario, Canada, she applies not just her education as a traditional architect but an entire holistic view on modular design. It’s this expansive view that guides her work on being a true partner that bridges the gap between architects and modular factories as they collaborate on the design process.
Tamarack Grove Engineering: Designing for the Modular Sector
The role of a structural engineer is crucial to the success of a modular project, from initial analysis to construction administration. Tamarack Grove offers structural engineering services — project analysis, plan creation, design creation, and construction administration — for commercial, manufacturing, facilities, public services, and modular. Modular is only one market sector the company serves but it is an increasingly popular one.
Engineer Masters the Art of Listening to His Customers
Since founding Modular Structural Consultants, LLC. in 2014, Yurianto has established a steady following of modular and container-based construction clients, primarily manufacturers. His services often include providing engineering calculations, reviewing drawings, and engineering certification
Inside College Road: Engineering the Modules of One of the World’s Tallest Modular Buildings
College Road is a groundbreaking modular residential development in East Croydon, South London by offsite developer and contractor, Tide, its modular company Vision Volumetric (VV), and engineered by MJH Structural Engineers.
Design for Flow: The Overlooked Power of DfMA in Modular Construction
Unlocking higher throughput, lower costs, and fewer redesigns by aligning Lean production flow with design for manufacturing and assembly.