Offsight’s Value Add to Your Factory
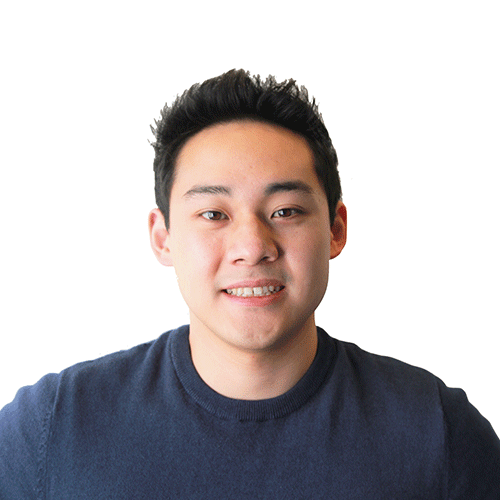
About the Author: Andrew Xue is the chief operating officer at Offsight, a developer of factory project management software for the offsite construction and building components industry.
The offsite and modular construction industry is booming. Over the coming 5 years analysts predict a fundamental shift in the construction industry, resulting in a new $256B annual profit pool up for grabs. This new demand has incentivized the founding of many new factories and the expansion of many currently operating modular businesses. These factories, which are at various stages of production maturity, face an important choice. When is the best time to implement technology and is technology needed to improve and manage quality reporting and operational processes?
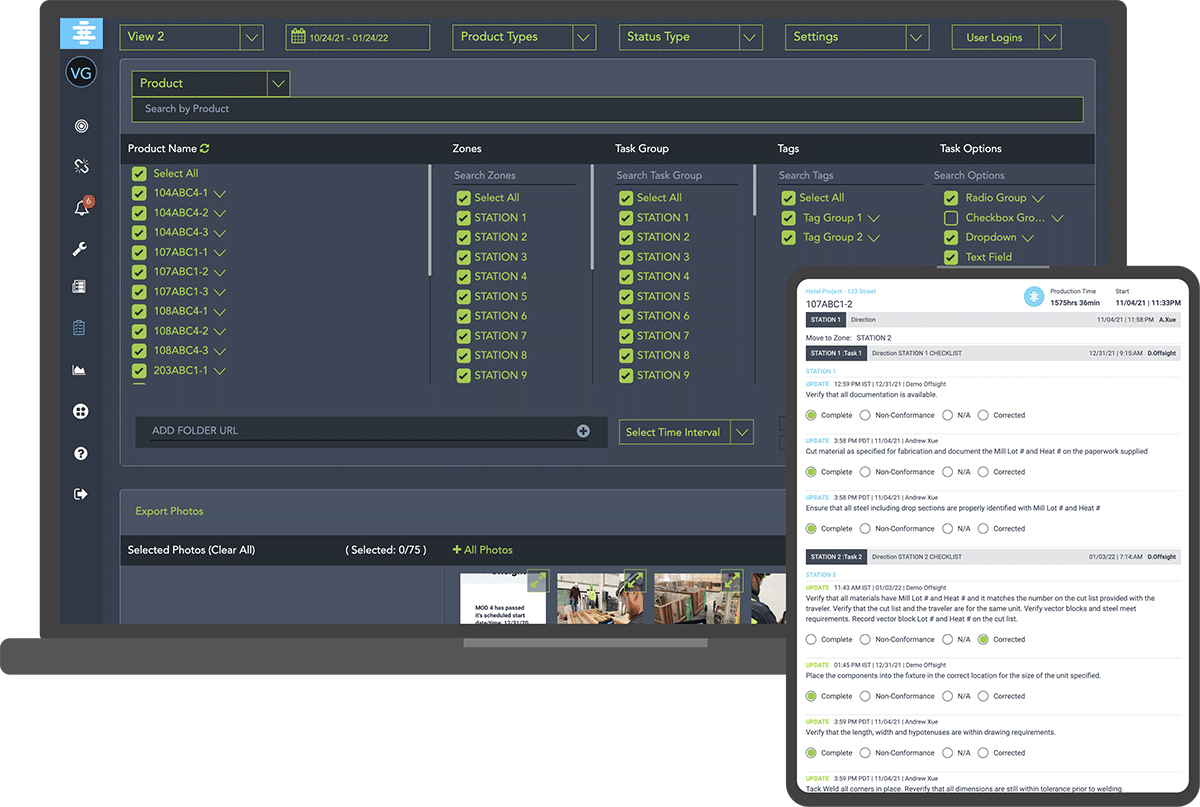
In this article, we outline the value of Offsight’s factory project management software across several clients that participated in case studies after implementing Offsight:
- Volumetric Building Companies (VBC) is a vertically integrated manufacturing and construction company that uses Offsight’s project management software to provide module-level visibility to all critical stakeholders and ensure every offsite project is successful. Offsight provides a multitude of customizable checklists to track production and quality of each module. After module delivery, Offsight digitally stores the entire history of the module and all relevant activity in the History tab. This includes all production interactions such as images taken on the factory floor, checklists completed and production data, which can be leveraged for future offsite projects.
- Z Modular, a subsidiary of industry steel giant Zekelman Industries, has implemented Offsight’s project management software at their Chandler, AZ and Killeen, TX modular manufacturing facilities to streamline product quality and production progress tracking. Offsight’s software helps manufacturers maximize scalability in their process, coordinate with many internal and external project stakeholders and provides a level of flexibility necessary to accommodate a wide variety of commercial modular projects.
See our Online Case Studies
The rapid rise of offsite and modular construction across multifamily, commercial, affordable housing, workforce housing and hospitality projects have shifted work from the traditional construction jobsite to the factory. With this process shift and move to modular, owners and project stakeholders are increasing their expectations around managing production quality and reporting at the factory level. In this case study, we walk through how industry leaders leverage Offsight to track factory quality and manage crucial internal and third-party reporting.
The global modular construction market is booming and expected to exceed $100B by 2025 with steel modular construction expected to be the fastest growing segment over the next 5 years. This bodes well for many steel modular manufacturers, including Offsight’s customer Z Modular.
Check us out at the 2022 World of Modular
Implementing Offsight’s technology, even at the early stages of your factory’s prototyping and design production stage, helps you avoid rising operational costs and position your business as an innovative and thought leading brand for operational and quality excellence from day one. If you’re interested in learning more, we encourage you to visit our booth at the 2022 World of Modular Conference. You can check out our product in action or reach out to our team directly at sales@offsight.com to schedule your private demo.
More from Modular Advantage
AI, Faster Sets, and Automation: The Future of Modular is at World of Modular
While the modular building industry has long known that it can be an effective solution to increase affordable housing, the word is slowly spreading to more mainstream audiences. Three presentations at this year’s World of Modular in Las Vegas hope to provide insight and direction for those seeking a real solution to the crisis.
An Insider’s Guide to the 2025 World of Modular
The Modular Building Institute is bringing its global World of Modular (WOM) event back to Las Vegas, and with it comes some of the industry’s best opportunities for networking, business development, and education. Over the course of the conference’s four days, there will be numerous opportunities for attendees to connect, learn, and leverage event resources to get the most out of the conference.
Affordable Housing Now: The Industry’s Best Bring New Solutions to World of Modular
While the modular building industry has long known that it can be an effective solution to increase affordable housing, the word is slowly spreading to more mainstream audiences. Three presentations at this year’s World of Modular in Las Vegas hope to provide insight and direction for those seeking a real solution to the crisis.
Opportunities for Innovation in Modular Offsite Construction
Modular Offsite Construction has already shattered the myth that it only produces uninspired, box-like designs. Architectural innovations in module geometry, configurations, materials, and products make it possible to create visually stunning buildings without sacrificing functionality or efficiency.
Safe Modular Construction with Aerofilm Air Caster Transport
In collaboration with Aerofilm Systems, Heijmans developed innovative skids using air caster technology for moving modules easily and safely. These pallets are equipped with an auto-flow system, making operation extremely simple.
Miles, Modules, and Memes: Building a Modular Network One Flight at a Time
At the end of the day, social media is just another tool for building connections, and like any other tool, needs to be used skillfully to work properly. Use social media thoughtfully, and it will open doors to real opportunities and relationships you didn’t even see coming.
Falcon Structures: Thinking Inside the Box
Some of Falcon’s latest projects include creating container solutions for New York’s Central Park and an East Coast professional baseball team. More and more, Falcon is shipping out container bathrooms and locker rooms to improve traditionally difficult work environments, like those in oil and gas or construction.
UrbanBloc—From Passion to Industry Leader
UrbanBloc specializes in three main categories or markets – what they call “Phase 0” projects, amenities, and urban infill. Clients are often attracted to shipping containers because from a real estate perspective they are considered an asset. Having the flexibility to move and transport these assets allows owners to respond to different circumstances in a fluid manner that they can’t get with standard construction.
The Hospitality Game-Changer
“Hospitality is about more than just providing a service – it’s about delivering an experience,” says Anthony Halsch, CEO of ROXBOX. “And that’s where containers thrive. They allow us to create spaces that are unique, efficient, and sustainable.”
Container Conversions Counts on Simplicity to Provide Critical Solutions
Container Conversions has fabricated and developed thousands of containers for varied projects, including rental refrigeration options, offices, kitchens, temporary workplace housing, and mobile health clinics.