Robots are the Future of Modular Construction
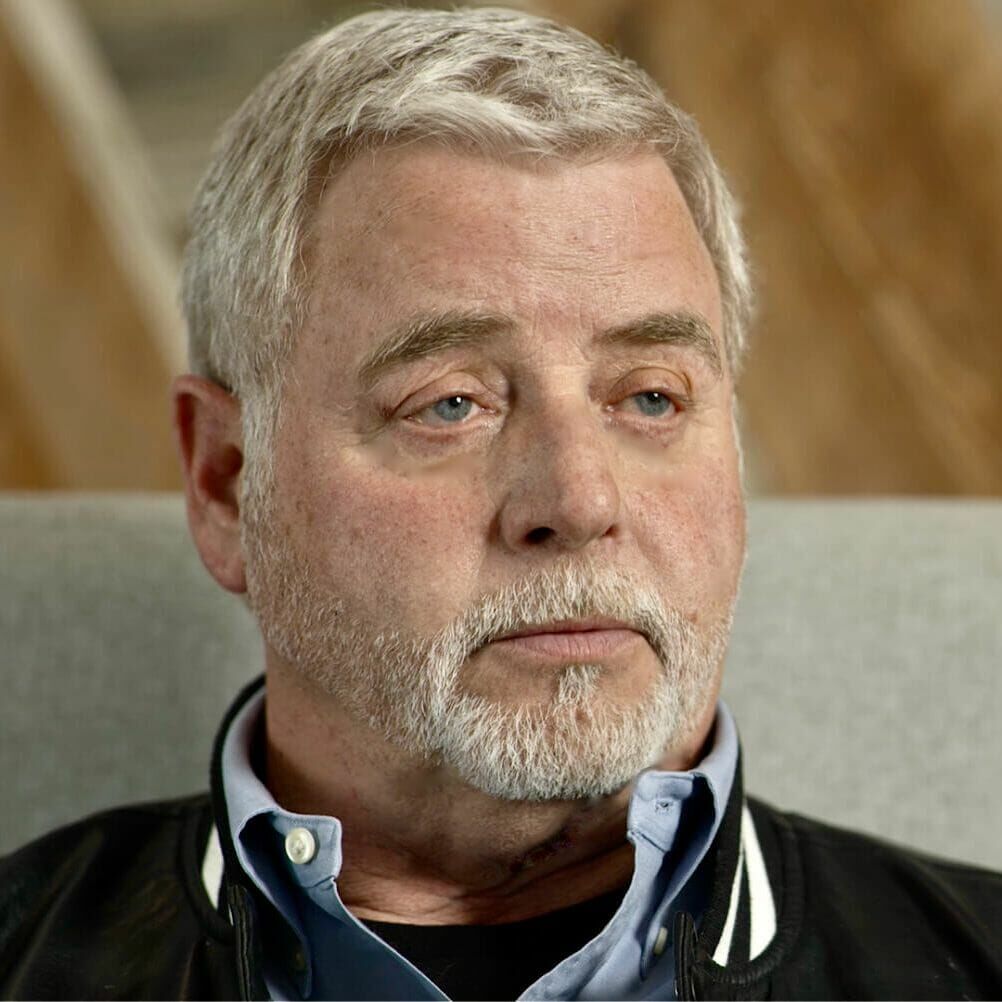
Rick Murdock is a building operations and manufacturing expert with 40 years of experience managing modular construction projects across the US and Canada. His experience includes serving most recently as a Founder and COO of Guerdon Enterprises, where he pioneered major innovations in large scale multi-story, multi-family modular manufacturing that made the company an award-winning industry leader. He has led operations for multiple manufacturing divisions, overseeing the execution a plethora of successful modular projects.
Autovol CEO and co-founder, Richard Murdock, has worked in the modular industry since he was 19 years old. “Back then, there wasn’t a lot of modular stuff going on. It was mostly mobile homes. I loved it from the first day, and have continued to love it.” Over the years, he’s worked on many different types of projects, including military camps, hotels, market-rate apartments, and affordable apartments. And he’s had experience in a number of different companies, across many different areas of operations.
That experience includes having worked on the shop floor, so he has first-hand knowledge of the hard physical work that modular construction — like traditional construction — typically involves. “It’s hard labor to build floors and ceilings and walls. It involves handling very heavy materials, and it’s hard on the body to do that for long periods of time.”
Murdock says that when he was young, it was easy to find people willing to do that hard physical labor, but it’s much more difficult today. And not only is it hard to attract workers, it’s hard to keep them — and prevent their bodies from wearing out.
“Few young people are attracted to the construction industry — including the modular industry — and I think that’s largely because of the hard, heavy physical work on a day-to-day basis. So I thought that automation and robotics would take the heavy lifting off humans, and help attract young people who have grown up with technology.”
In addition to tackling the labor shortage, Murdock’s view is that by embracing automation, the modular industry also has a great opportunity to make a dent in the problem of supplying affordable housing. This insight led to the birth of Autovol in 2019, which makes extensive use of robots in its production lines.
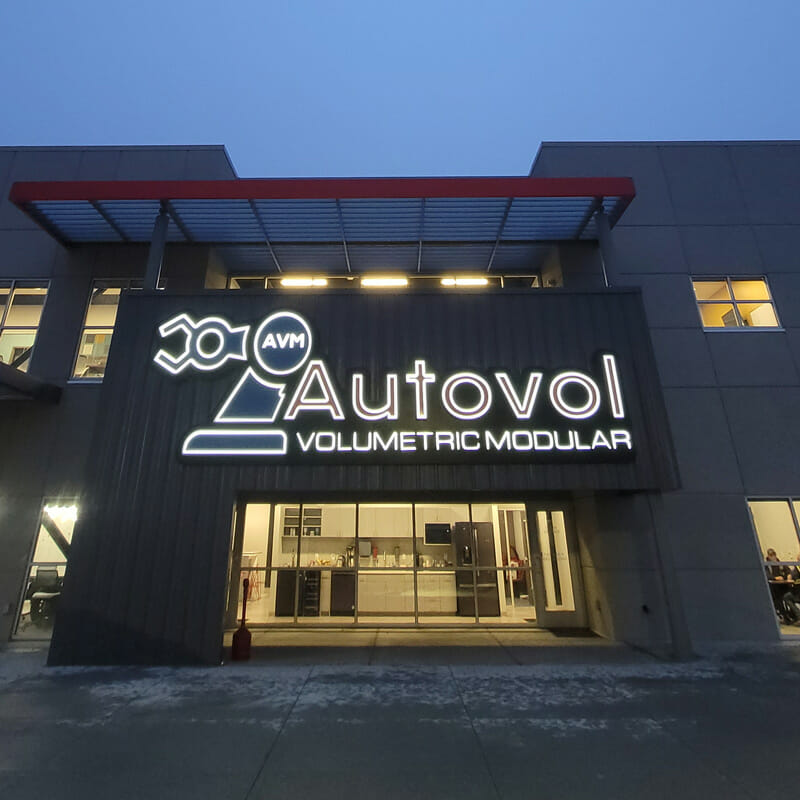
Autovol CEO Rick Murdock’s view is that by embracing automation, the modular industry also has a great opportunity to make a dent in the problem of supplying affordable housing.
Robots improve hiring, retention, and quality of work
Automation has made hiring easier for Autovol. In particular, they’ve been able to attract more young people and women — currently 31% of the company’s employees are women.
“We’ve seen a huge difference in hiring,” Murdock says. “The technology has attracted a wicked-smart group of young people. They’ve grown up with technology, and they enjoy it.”
By freeing people from heavy lifting work, Murdock says Autovol can make better use of employees’ brains, and “we’ve seen far less employee turnover and injuries in our automated areas because we’ve minimized the strenuous labor.”
He emphasizes the importance of the people in the plant. “At the end of the day, robots are nothing without people to program, schedule, and operate them. The robots are just tools.”

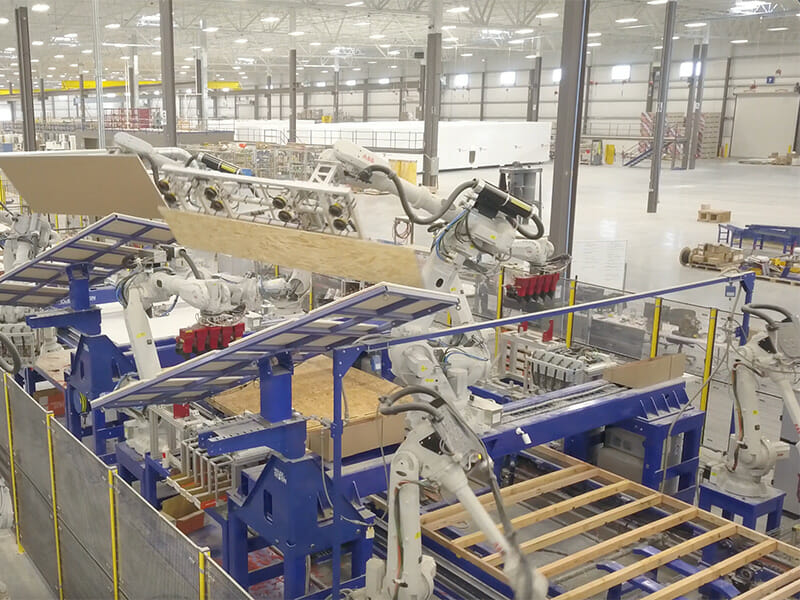
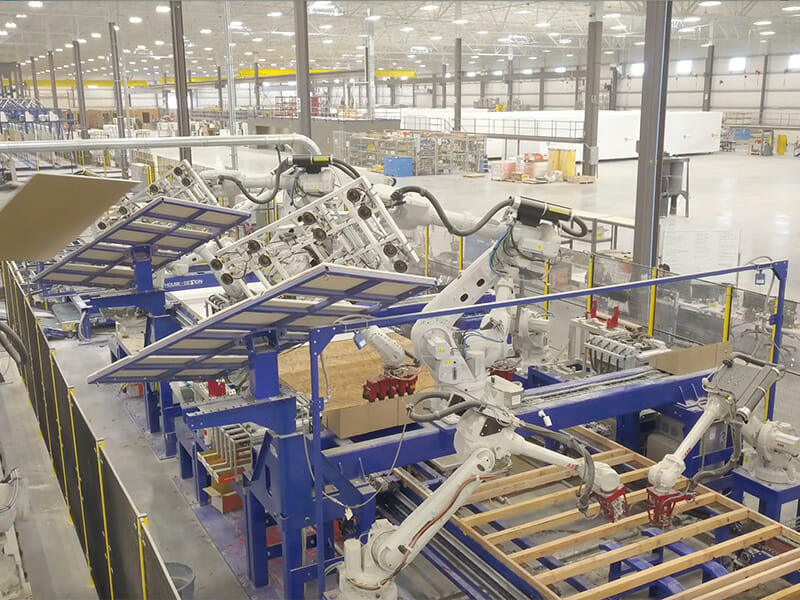
They’re tools that result in a higher quality product that’s produced more quickly. “Without automation, you’d need a lot more labor to produce modules at the same rate,” Murdock says. “And even if you had that labor, you wouldn’t have the precision. People get tired, they make mistakes. After working with heavy tools for a few hours, there’s more variation in placement. Robot arms never get tired, sluggish, or inaccurate.”
The precision robots can eliminate re-work — which is a time-consuming expense. “The more square you can make a building, the more exact the placement of fasteners is. The more exact you can make each component of a building, the better the building goes together, the better all the finishes end up,” Murdock says. “When all the pieces come together, you get a nice, crisp product. You have less drywall cracking, things like that. Less re-work means lower costs.”
“Without automation, you’d need a lot more labor to produce modules at the same rate,” Murdock says. “And even if you had that labor, you wouldn’t have the precision. People get tired, they make mistakes. After working with heavy tools for a few hours, there’s more variation in placement. Robot arms never get tired, sluggish, or inaccurate.”
Autovol’s robots work alongside humans
To develop Autovol’s plant in Idaho, Murdock collaborated with experts in automation and robotics technology in the automobile and other industries. At this point, the factory lines that build module walls are already fully automated. Murdock explains: “Robots pick the lumber, stage it, do all the framing. They nail, glue, or screw all the parts. They pick the OSB [oriented strand board] or sheet rock, place it, and other robots come in to secure it. More robots cut the openings. Robots complete entire wall sections and move them to the storage area without human hands touching them at all.”
Using overhead cranes, humans put the wall sections together. Then tradespeople install windows, cabinets, MEP, and so on.
The lines for the floor systems and ceiling systems have not yet reached that same level of automation, but Murdock anticipates they will be fully automated within a few months, with a year or two to perfect the processes and gain maximum efficiencies.
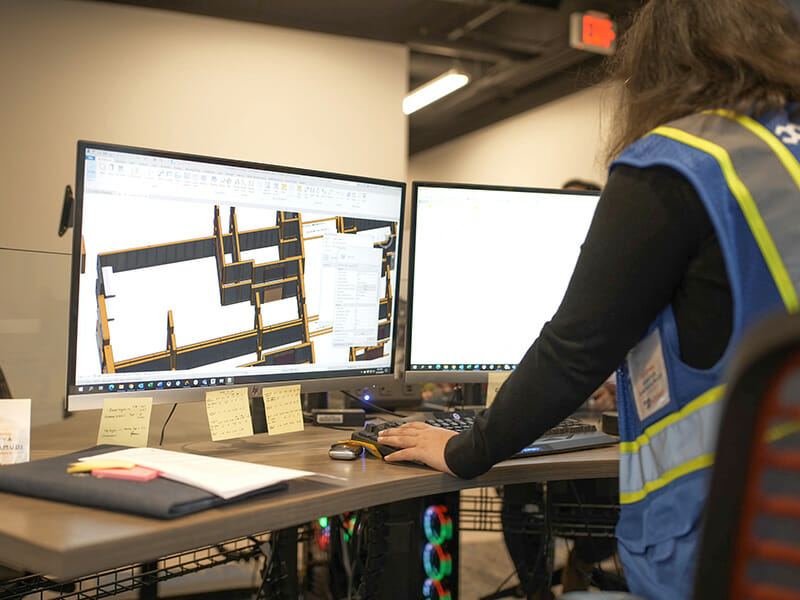
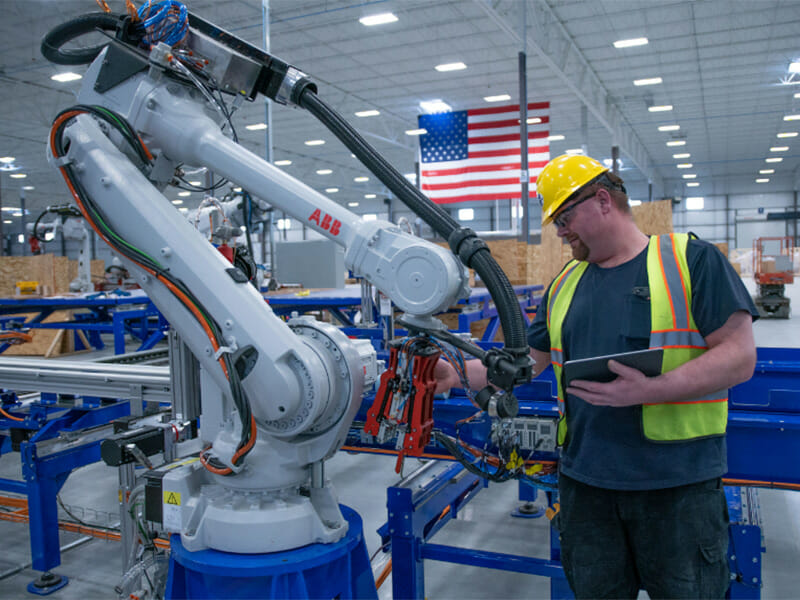
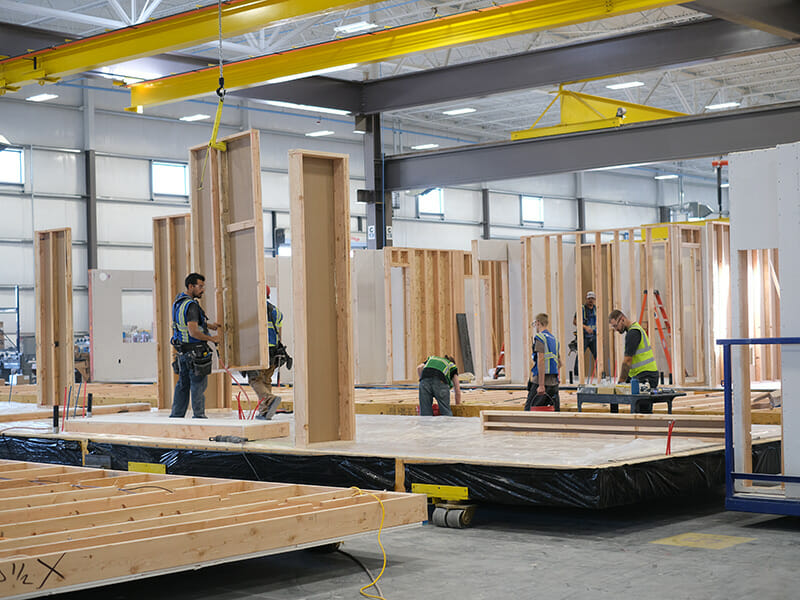
Making more affordable housing
“We’re focusing on affordable housing because that’s a crisis right now,” Murdock says. “By using automated modular manufacturing, we can build more efficiently and so lower the cost of construction in many markets. Ultimately, that lowers the cost people have to pay to live in an apartment.”
The Idaho factory is currently manufacturing modules for Autovol’s fourth major project — a five-story affordable housing complex consisting of two- and three-bedroom apartments, which will be located in California. Their previous three projects were studio apartments, the first of which has been set, and the other two are getting ready for shipment.
Design for efficiencies
To gain maximum efficiencies and keep costs down, the company tries to standardize their manufacturing operations as much as possible. “Although in many ways each project is different, we are able to re-use some aspects of the designs so we can reap greater efficiencies,” Murdock says.
He also emphasizes the importance of the company being involved in design from the earliest stages of a project. “It’s always best when a project is designed to be modular from the beginning. We work with the architect on the design, engineering, and MEP [mechanical, electrical, plumbing] for each building.”
Autovol collaborates with Prefab Logic, a pre-construction firm, to translate the architectural vision into factory data. “That data is used to create the file that gives the robots instructions for the construction processes they need to perform.”
The future is robotic
Murdock believes that there’ll be more and more automation in the modular industry — both because it produces a better, more precise product and because of labor shortage pressures. In his view, there simply aren’t enough people available to build buildings fast enough to meet the demand for them. The only way to meet the demand is to use more automation.
“The demand for affordable housing is so high that one factory can’t make much difference. In the future, whether they’re Autovol plants or other automated volumetric plants, there’s going to be many more of them in the United States — and around the world — to meet the demand.”
Murdock says the idea behind Autovol is to improve the way construction is done, and that the company has fostered a community of people who share the same mission. “Automation and robotics are wonderful. But it’s people who make things happen. It’s people who build successful companies.”
About the Author: Zena Ryder is a freelance writer, specializing in writing about construction and for construction companies. You can find her at Zena, Freelance Writer or on LinkedIn.
More from Modular Advantage
Behind the Design of Bethany Senior Terraces, NYC’s First Modular Passive House Senior Housing Project
As more developers seek to meet new regulations for energy efficiency, the team at Murray Engineering has set a new record. With the Bethany Senior Terraces project, Murray Engineering has helped to develop NYC’s first modular structure that fully encompasses passive house principles — introducing a new era of energy efficiency in the energy-conscious city that never sleeps.
How LAMOD is Using Modular to Address Inefficiency, Sustainability, and the Future of Construction
As developers, designers, and contractors seek to understand the evolving needs of the modular industry, no one is as well-versed in the benefits of going modular as Mārcis Kreičmanis. As the co-founder and CBDO of LAMOD in Riga, Latvia, Mārcis has made it his ultimate goal to address the inefficiencies of traditional construction.
From Furniture Builder to ‘Activist Architect’: Stuart Emmons’ Unique Journey
Stuart Emmons was fascinated by buildings at a young age. He remembers building sand cities with his brother during trips to the Jersey shore. His father gave him his first drawing table at the age of ten. Today, he is an experienced architect who received his FAIA in June 2025. The road he took is unique, to say the least.
Forge Craft Architecture + Design: Codes, Contracts, and Intellectual Property
Founding Principal and Director of Modular Practice for Forge Craft Architecture + Design, Rommel Sulit, discusses the implications of codes, contracts, and intellectual property on
modular construction.
Eisa Lee, the “Bilingual” Architect
Now as the founder of XL
Architecture and Modular Design in Ontario, Canada, she applies not just her education as a traditional architect but an entire holistic view on modular design. It’s this expansive view that guides her work on being a true partner that bridges the gap between architects and modular factories as they collaborate on the design process.
Tamarack Grove Engineering: Designing for the Modular Sector
The role of a structural engineer is crucial to the success of a modular project, from initial analysis to construction administration. Tamarack Grove offers structural engineering services — project analysis, plan creation, design creation, and construction administration — for commercial, manufacturing, facilities, public services, and modular. Modular is only one market sector the company serves but it is an increasingly popular one.
Engineer Masters the Art of Listening to His Customers
Since founding Modular Structural Consultants, LLC. in 2014, Yurianto has established a steady following of modular and container-based construction clients, primarily manufacturers. His services often include providing engineering calculations, reviewing drawings, and engineering certification
Inside College Road: Engineering the Modules of One of the World’s Tallest Modular Buildings
College Road is a groundbreaking modular residential development in East Croydon, South London by offsite developer and contractor, Tide, its modular company Vision Volumetric (VV), and engineered by MJH Structural Engineers.
Design for Flow: The Overlooked Power of DfMA in Modular Construction
Unlocking higher throughput, lower costs, and fewer redesigns by aligning Lean production flow with design for manufacturing and assembly.
Choosing the Right Ramp
Modular construction offers a compelling alternative to traditional methods for designing and building ADA and IBC-compliant entrances. By addressing the challenges of traditional construction, such as time-consuming processes, unavailable specialized labor, and variable field conditions, modular solutions provide a more efficient, cost-effective, and reliable approach.