Lightweight & Beautiful 3D Printing
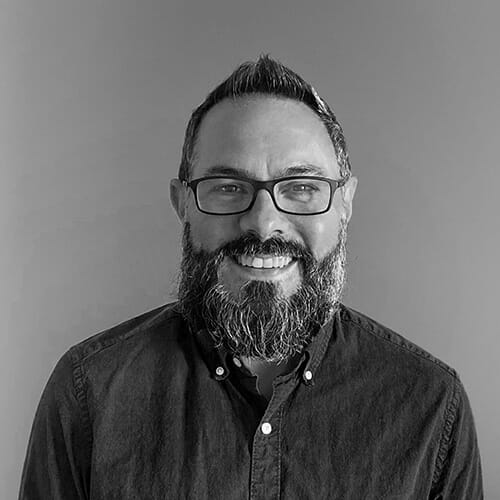
John McCabe is the Advanced Concepts Designer at Branch Technology, recently transitioning into that role from the Director of Marketing position at the company. McCabe has a Bachelor’s Degree in Architecture and a Masters in Industrial Design. He taught design at various institutions before moving to Branch in 2019.
Offsite Advantages
When you think of 3D printing buildings, you probably picture giant outdoor robot gantries “pooping out concrete” as John McCabe of Branch Technology puts it. Layer upon layer, gradually building up the walls “as has been done for millennia” — only now with robotics.
Branch Technology does 3D printing very differently, starting with printing offsite. “Printing onsite adds chaos, where there’s already a lot of safety issues,” says McCabe. Branch’s facility is far from chaotic — it’s a precise robotic ballet, with multiple projects being coordinated at the same time.
“In our facility, we have 12 foot robots printing a range of different types and scales of projects. One might be working on part of a parking deck, and another might be working on a bank, while another is printing something for the Department of Defense.”
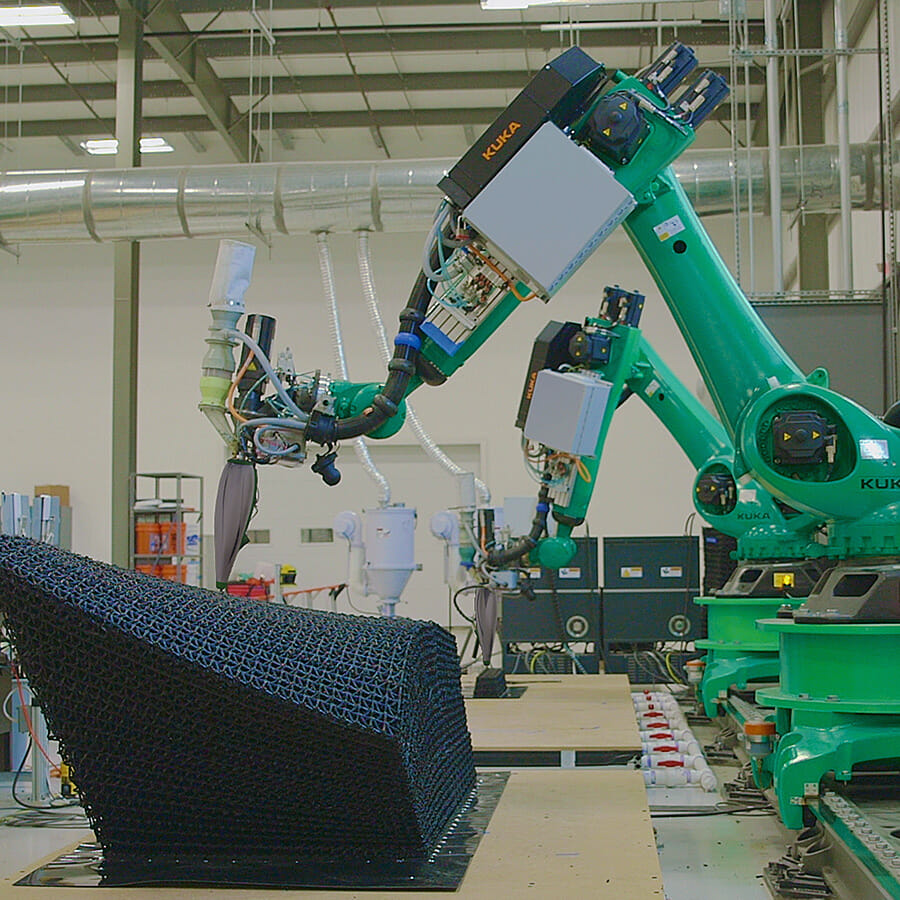
Special Structures
The structures that Branch robots print are also very different from layers of undifferentiated concrete. They are complex lattices that can be manufactured from various substances, have many different shapes and sizes, and be filled with different materials.
“Think about it. Very few buildings are made of only one type of material,” says McCabe. “Branch processes can combine complementary materials, increasing the resulting building’s capabilities and adding value for the client.”
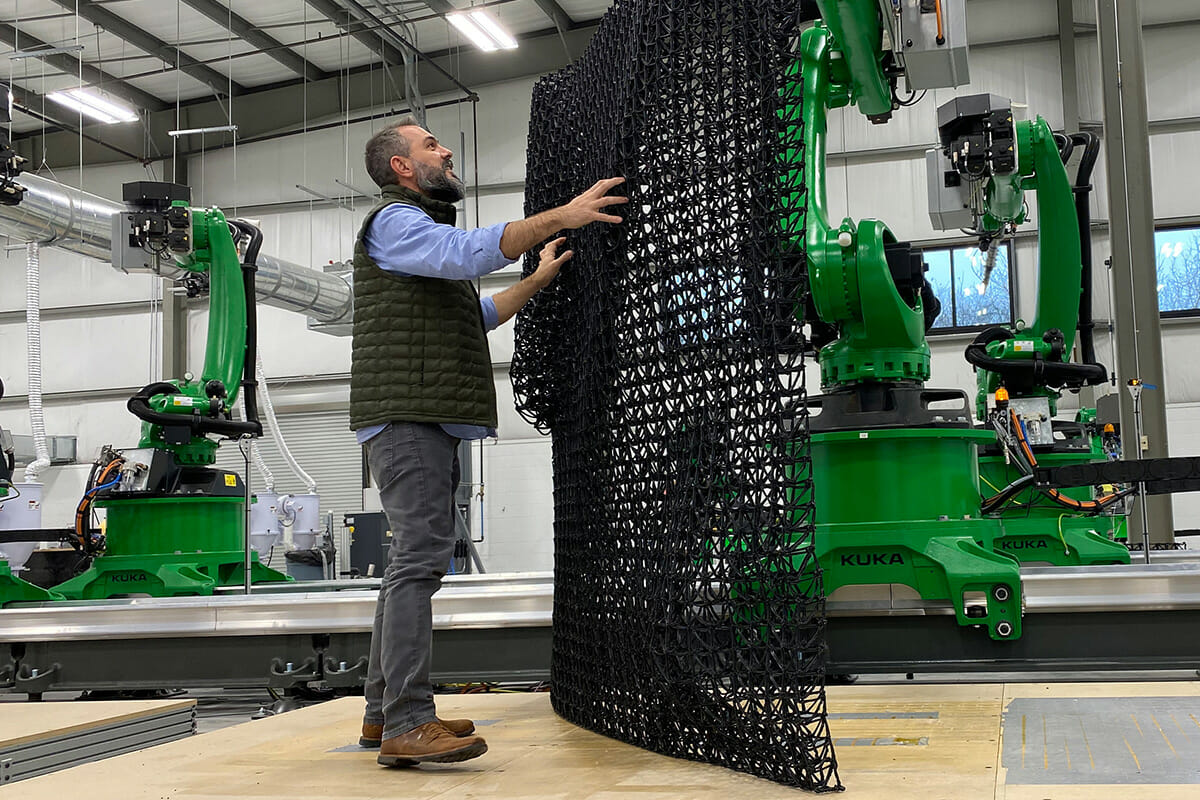
Branch’s 3D printing “uses 20 times less material than other 3D printing methods, with almost no waste” and the resulting structures are many times lighter than a similar size structure printed with concrete. Although they’re light, the structures are designed for strength too. “A matrix we print that’s the size of a concrete block — but which is 90% air — will hold 2000-3000
pounds of compressive force,” explains McCabe. “When we fill that space with a customized foam, we can get almost 10,000 pounds of compressive strength.”
The lattice structures can be filled with various materials with different properties such as sound attenuation or thermal insulation. Sensors can be embedded within the materials to create a smart building.
Branch has printed a 3,000 square foot single story house. McCabe says it’ll be a few years before they can focus on building tall, self-supporting structures because the materials currently can’t compete with the capabilities of steel. “For the same reason, it’ll also be a long time before 3D printing with concrete can build taller than one storey.”
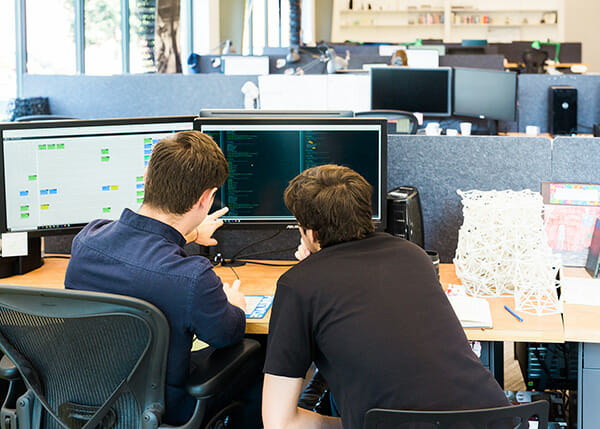
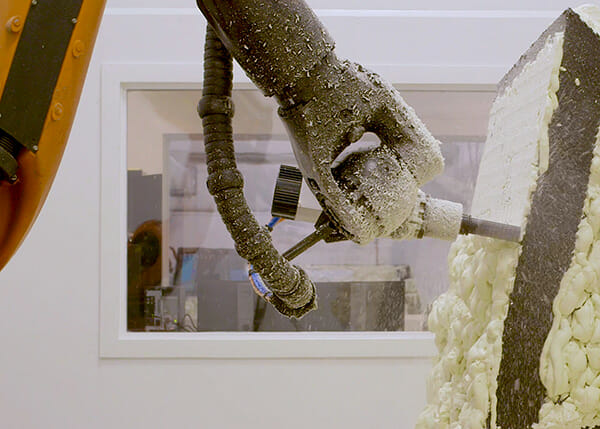
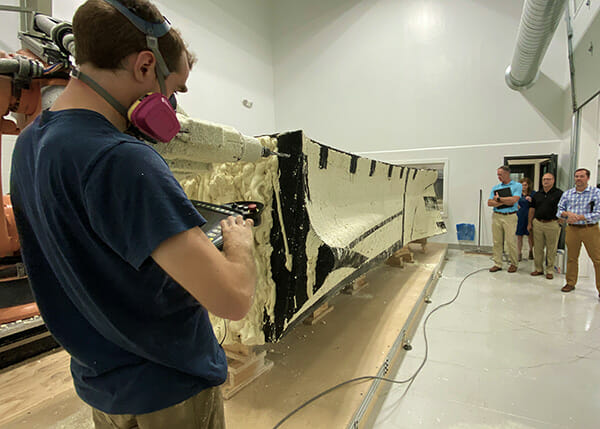
Founding and Focus
How was Branch founded? In 2013, there was a Kickstarter project for a 3D printing pen that could print in midair. Branch Founder and Chief Executive Officer, Platt Boyd, bought one and played around with it, attaching it to mini robots. He decided the idea had commercial potential in the construction industry, left the architecture firm where he’d worked for over 15 years, and moved to Chattanooga to found Branch. (Chattanooga and the surrounding area is a hotbed for innovation, especially in advanced manufacturing.)
“The company was embraced by the Chattanooga startup culture and the first employees were rockstars who came here from places like New York City and Boston. For the most part, they’re still here,” says McCabe. “We now have about 30 people working here and they’re the smartest group of people I’ve ever had the good fortune to work with.”
Because 3D printing is so versatile, Branch often received requests to make random things. But Boyd decided they needed to focus and the company went all-in on developing 3D printed façades. “They’re a great non-structural way to add a signature look to a building while still embracing the traditional construction trades.”
Labor
It’s a persistent refrain that it’s hard to hire young people to work in the construction industry, and labor shortages are a major problem. But working in the Branch facility is a far cry from a typical construction environment and Branch hasn’t had hiring problems.
“Construction companies can’t find talent,” says McCabe. “I’m privileged to work with a large, diverse group of young people who are very excited about robotics and the future of construction. They want to work in this industry.”
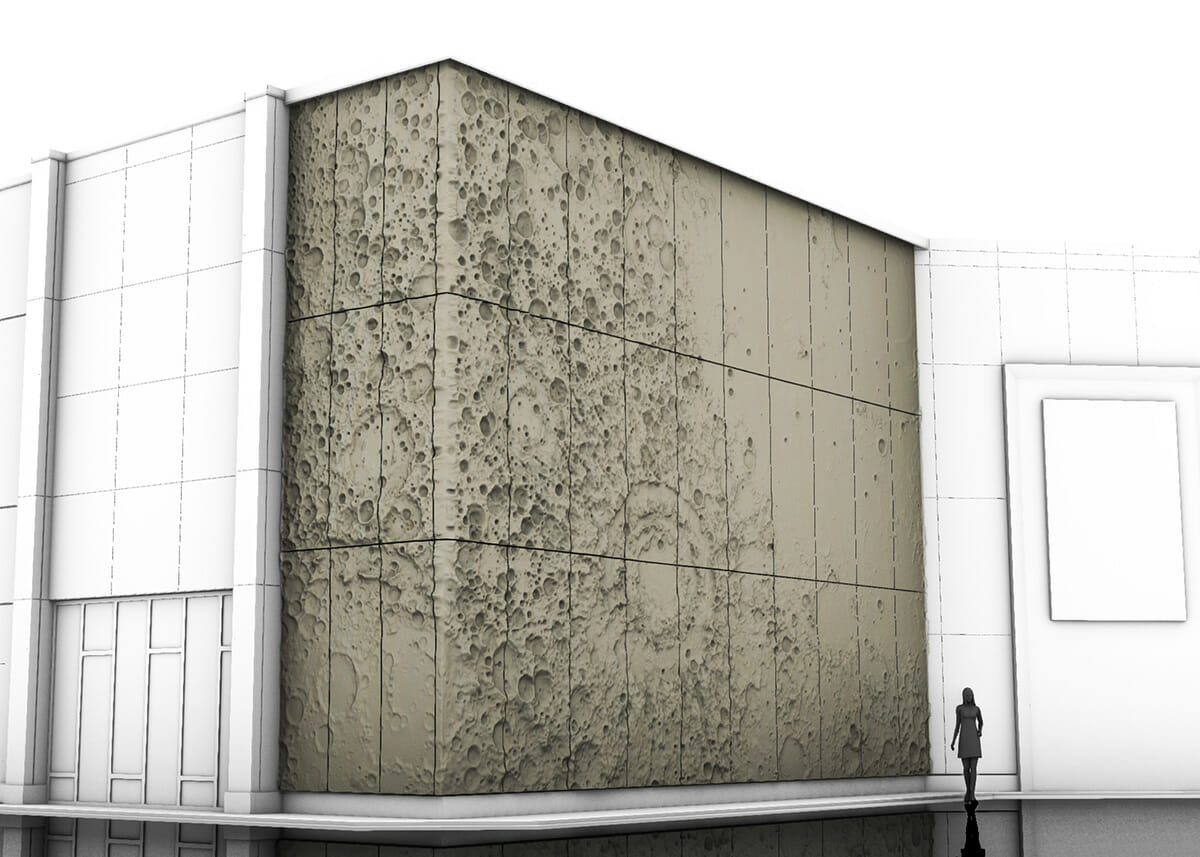
Off-World Construction
Branch has a team focused on developing solutions for the Department of Defense. “We’ve been taking speculative ideas and creating advanced manufactured products to fit their customized need,” says McCabe. “The kind of project ranges from a logistics solution for high-tech equipment, a building façade for onsite housing, or lightweight EMP-hardened expeditionary structures.”
They also work with the Air Force and the Space Force, leaning into this since 2017 when, out of a field of 77 global competitors, Branch won first place in the NASA Martian Habitat Challenge. The material they co-developed for printing the Martian habitat was the equivalent of 70% Martian soil, mixed with 30% recyclable mission waste such as bags and parachutes.
“The Space Force is expanding their knowledge and capabilities in off-world construction. We’ve been involved in developing zero-g and other-world concepts to save fuel and time, as well as to protect our service-people and equipment
from harm.”
The Future
Branch is partnering with real estate companies, developers, construction companies, and architecture firms. McCabe says that small companies trying to make their mark as well as big companies looking for efficiencies see value in Branch’s work.
“In the long term, we want a distributed factory network around the world that can print, fill, and finish structural and non-structural components for buildings of all scales,” says McCabe. “We have a roadmap to get there. We have some great partnerships in the pipeline and it’s going to blow some minds when we can finally talk about them!”
About the Author: Zena Ryder is a freelance writer, specializing in writing about construction and for construction companies. You can find her at Zena, Freelance Writer or on LinkedIn.
More from Modular Advantage
Oregon’s Prevailing Wage Proposal: A Wake-Up Call for Modular Construction
In early February, 2024, the Massachusetts Board of Building Regulations and Standards (BBRS) released its proposed 10th Edition building codes. This draft included several amendments targeting modular construction that would have created an extremely difficult environment for the entire modular industry and could have eliminated the industry entirely in the state.
Behind the Design of Bethany Senior Terraces, NYC’s First Modular Passive House Senior Housing Project
As more developers seek to meet new regulations for energy efficiency, the team at Murray Engineering has set a new record. With the Bethany Senior Terraces project, Murray Engineering has helped to develop NYC’s first modular structure that fully encompasses passive house principles — introducing a new era of energy efficiency in the energy-conscious city that never sleeps.
How LAMOD is Using Modular to Address Inefficiency, Sustainability, and the Future of Construction
As developers, designers, and contractors seek to understand the evolving needs of the modular industry, no one is as well-versed in the benefits of going modular as Mārcis Kreičmanis. As the co-founder and CBDO of LAMOD in Riga, Latvia, Mārcis has made it his ultimate goal to address the inefficiencies of traditional construction.
From Furniture Builder to ‘Activist Architect’: Stuart Emmons’ Unique Journey
Stuart Emmons was fascinated by buildings at a young age. He remembers building sand cities with his brother during trips to the Jersey shore. His father gave him his first drawing table at the age of ten. Today, he is an experienced architect who received his FAIA in June 2025. The road he took is unique, to say the least.
Forge Craft Architecture + Design: Codes, Contracts, and Intellectual Property
Founding Principal and Director of Modular Practice for Forge Craft Architecture + Design, Rommel Sulit, discusses the implications of codes, contracts, and intellectual property on
modular construction.
Eisa Lee, the “Bilingual” Architect
Now as the founder of XL
Architecture and Modular Design in Ontario, Canada, she applies not just her education as a traditional architect but an entire holistic view on modular design. It’s this expansive view that guides her work on being a true partner that bridges the gap between architects and modular factories as they collaborate on the design process.
Tamarack Grove Engineering: Designing for the Modular Sector
The role of a structural engineer is crucial to the success of a modular project, from initial analysis to construction administration. Tamarack Grove offers structural engineering services — project analysis, plan creation, design creation, and construction administration — for commercial, manufacturing, facilities, public services, and modular. Modular is only one market sector the company serves but it is an increasingly popular one.
Engineer Masters the Art of Listening to His Customers
Since founding Modular Structural Consultants, LLC. in 2014, Yurianto has established a steady following of modular and container-based construction clients, primarily manufacturers. His services often include providing engineering calculations, reviewing drawings, and engineering certification
Inside College Road: Engineering the Modules of One of the World’s Tallest Modular Buildings
College Road is a groundbreaking modular residential development in East Croydon, South London by offsite developer and contractor, Tide, its modular company Vision Volumetric (VV), and engineered by MJH Structural Engineers.
Design for Flow: The Overlooked Power of DfMA in Modular Construction
Unlocking higher throughput, lower costs, and fewer redesigns by aligning Lean production flow with design for manufacturing and assembly.