HHI Corporation Develops & Donates State-of-the-Art Mobile Triage Unit
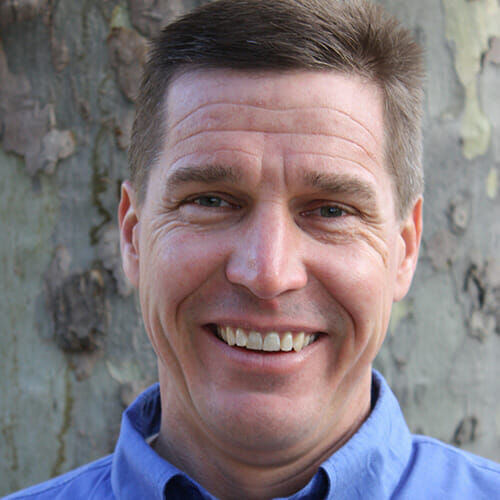
Cliff Hokanson’s parents founded HHI Corporation in 1971. Hokanson studied civil engineering at Utah State University, and during that time, he worked for a couple of years at a nonprofit research corporation that developed defense and space technologies. He joined the family business full-time in 1996. Hokanson is now the Executive Vice President of HHI Corporation, based in Utah, USA.
Before COVID-19, there was Ebola
HHI has extensive experience with precision engineering in the defense and aerospace industries, including manufacturing aircraft maintenance stands for 15 years. They’ve been doing industrial construction for 48 years for the U.S. Department of Defense and other clients. And they have 30 years of experience with biological and chemical containment.
In 2014-2016, there was an outbreak of the deadly infectious disease, Ebola, in west Africa. When American medical professionals treating Ebola patients were infected and became sick, they were flown back to the United States for treatment. However, to keep the flight crew and other passengers safe from the virus, it was necessary for the sick patients to travel inside biocontainment units called Containerized Bio-Containment Systems (CBCS).
The CBCS units had to be manufactured so that even if there was loss of pressure inside the plane, the virus wouldn’t seep out of the box and into the rest of the airplane. Working with MRIGlobal, a nonprofit research lab, HHI was tasked with designing and manufacturing these units.
“This is something that had never been done before and we had to do it in six months!” says Hokanson. “We designed it, fabricated and built it, and got it third-party tested, all in about 190 days.”
HHI built a total of four of these biocontainment pods for the U.S. Department of State. The units involve complex, precision engineering and were manufactured to a significantly higher standard than Biosafety Level 4 (BSL-4), the CDC’s highest standard for biocontainment. “The entire door system is a new invention. We had to make sure that patients would be safe, even if the units were sitting on the tarmac for 12 hours. So they each have their own power source, HVAC system, and adequate air flow,” Hokanson explains. “Medical-grade oxygen needed to be available. And the staff inside the unit needed to be able to communicate with the outside.”
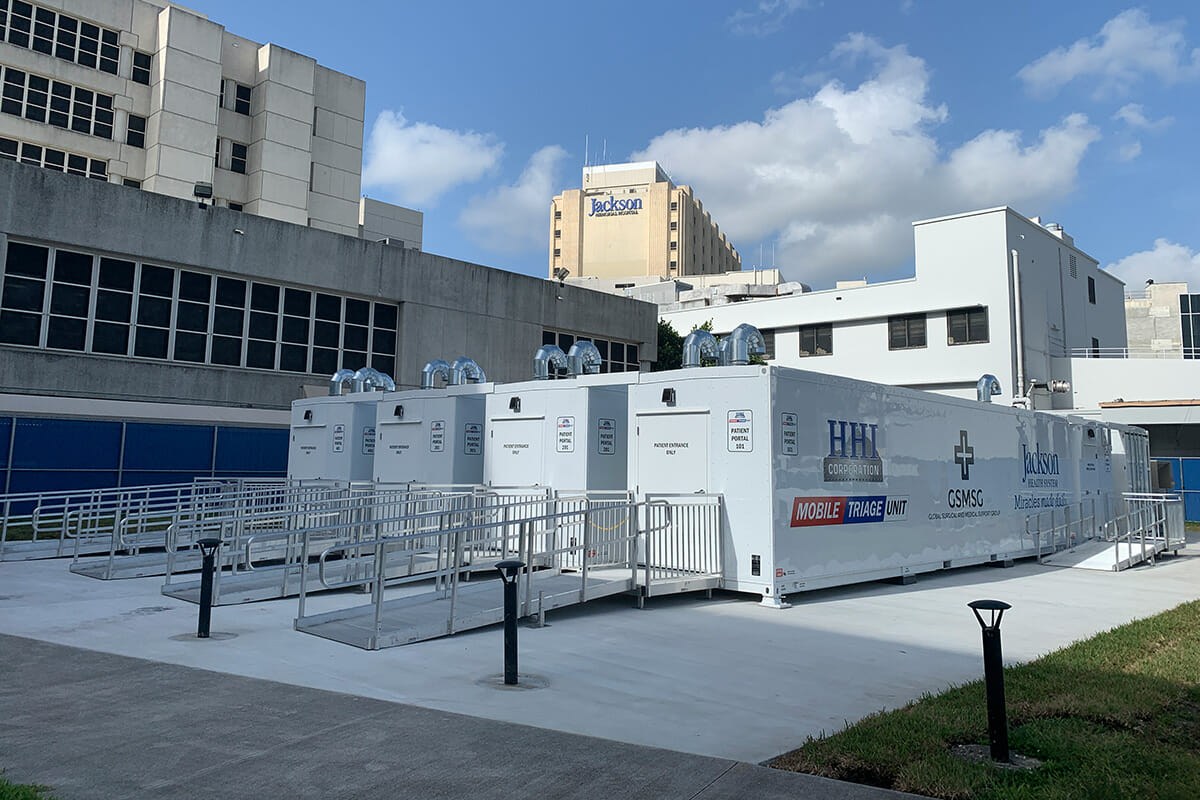
The layout of HHI Corporations' Mobile Triage Unit (MTU)—seen here outside the Jackson Memorial Hospital in Florida—includes four patient rooms with three beds each, nurses stations and support equipment. Systems include UPS power circuits, insulated wall and ceiling panels, hospital grade flooring with welded joints, two 1,500 gallon tanks for fresh and waste water, HVAC system with 18 air exchanges per hour, visual air flow sensors, single pass air system, HEPA filters, seven days of power via diesel generator, and fire alarm system with dialer. It also includes a HIPAA-approved networking package to integrate with existing hospital/medical facilities communications.
The COVID-19 Cruise Ship
Then, this year, Hokanson happened to see those same CBCS pods on TV — this time on flights bringing home COVID-infected patients from the Diamond Princess cruise ship, which had been quarantined off the Japanese coast.
He felt both proud and inspired.
HHI had the experience and skills to do something significant to help during the COVID-19 pandemic. So the team put their heads together and designed the Mobile Triage Unit. Once they developed the prototype, they got feedback and tweaked the design.
A press release from HHI describes the details of the MTU:
The layout of the MTU includes four patient rooms with three beds each, nurses stations and support equipment. Systems include UPS power circuits, insulated wall and ceiling panels, hospital grade flooring with welded joints, two 1,500 gallon tanks for fresh and waste water, HVAC system with 18 air exchanges per hour, visual air flow sensors, single pass air system, HEPA filters, seven days of power via diesel generator, and fire alarm system with dialer. It also includes a HIPAA approved networking package to integrate with existing hospital/medical facilities communications.
“I’m pretty sure the MTU is the first of its kind. It’s mobile, can be completely set-up within a couple of days, and can withstand hurricane-force winds.”
Related Listening:
Modular Triage Units for COVID-19 w/ HHI Corporation
In this episode, MBI marketing director John McMullen talks with Cliff Hokanson, Executive VP of HHI Corporation, about HHI's new Mobile Triage Units. Cliff walks listeners through the layout of the units, describes their functions, and talks about the requirements for building modular healthcare facilities.
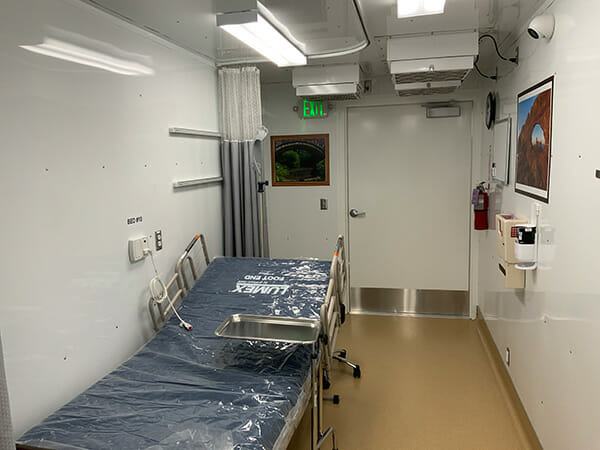
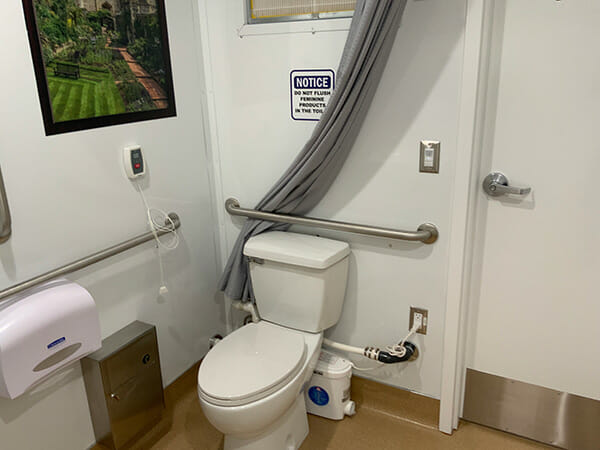
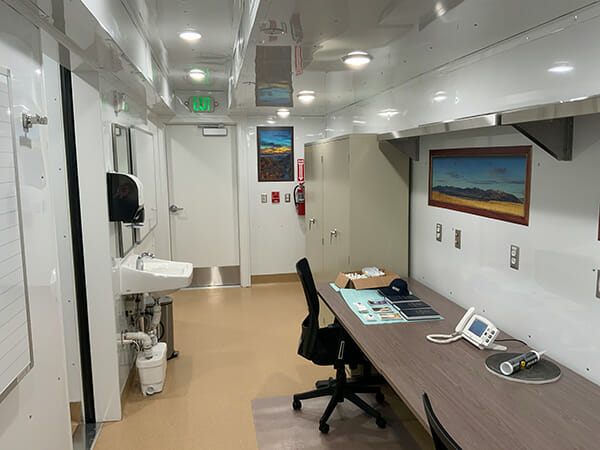
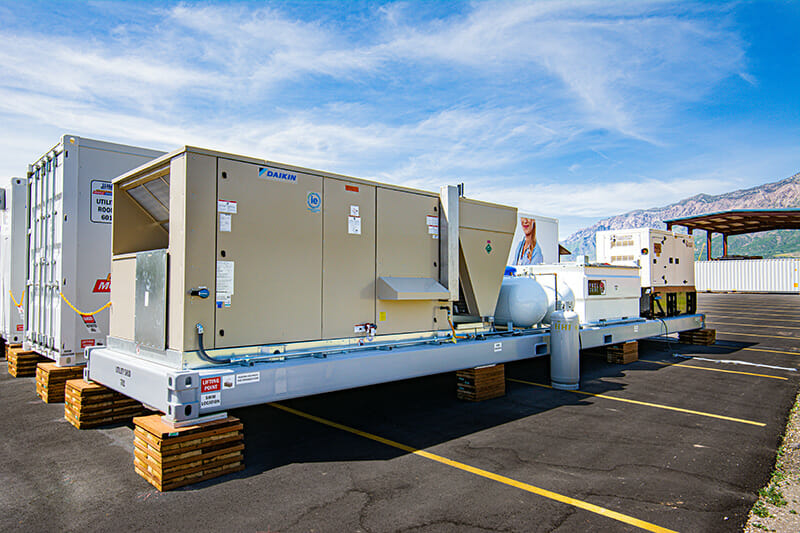
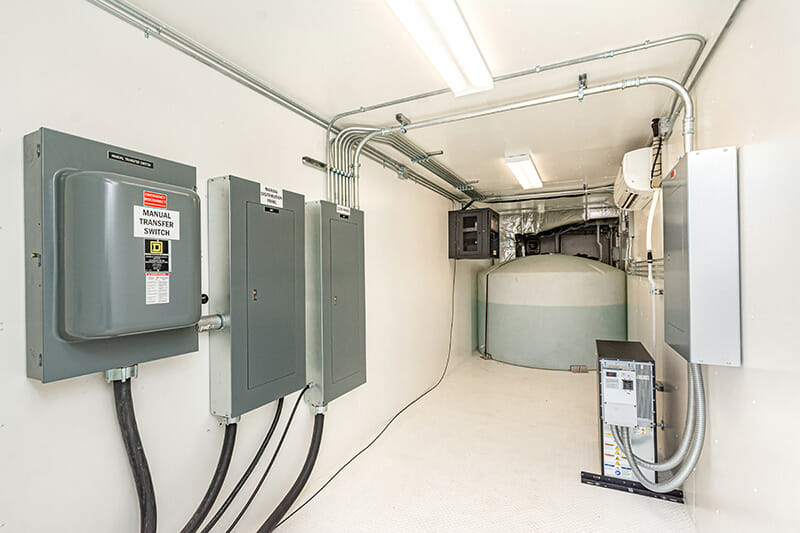
Supply Chain Challenges
Like other manufacturers, though, HHI struggled with disrupted supply chains. “Ordinarily, we have lots of suppliers for HEPA filters. These are a crucial component of the MTU because they capture the viruses as the air moves through them,” explains Hokanson. “But it was hard for suppliers to get enough of them, because factories were getting shut down and not making them.”
In fact, one of HHI’s usual suppliers was unavailable because she was sick with COVID-19 herself. Eventually, one supplier who knew what HHI was trying to do decided to put a hold on a delivery to another customer whose project wasn’t as urgent, and to prioritize HHI’s more urgent need.
“We had similar things happen for the generators, aluminum sheet stock, and flooring material,” says Hokanson. “Companies said they would work overtime shifts to get us what we needed. People really wanted to be part of this project.”
Inspiration
Instead of selling the first MTU, Hokanson decided to donate it to a healthcare facility that could make good use of it.
“I’m sure later in the year my accountant will say, ‘What were you thinking? Don’t you know how to add!’” laughs Hokanson. “But I believe in inspiration and I was inspired to donate it.”
Hokanson sent out an email to all his contacts and asked them to email all their contacts to find a suitable recipient for the MTU. In the end, HHI selected the Global Surgical Medical Support Group. The Jackson Memorial Hospital in Florida is housing the unit — and the medical staff are thrilled with the state-of-the-art addition to their facility.
HHI has a couple more MTUs that are close to completion. They’ll be ready to deliver in less than 6 weeks. Hokanson notes that we were unprepared for this pandemic, even though experts had been warning us for years. The MTU is a way that healthcare systems can be better prepared for outbreaks of future infectious diseases — as well as helping them cope this time around.
The MTU can also be used for other health crises — hurricanes and earthquakes to car accidents and mass shootings. They’re built to withstand hurricane force winds up to 185mph (298km/hr), and are designed to comfortable in outside temperatures between -20F to 110F (-29C to 43C). If necessary, they can be self-sufficient at full capacity for up to 7 days.
“We built it. But it’s inspiration and a lot of collective brainpower that made it happen.”
About the Author: Zena Ryder is a freelance writer, specializing in writing about construction and for construction companies. You can find her at Zena, Freelance Writer or on LinkedIn.
More from Modular Advantage
Oregon’s Prevailing Wage Proposal: A Wake-Up Call for Modular Construction
Should House Bill 2688A become law, building projects would increase in price, face longer completion timelines, and produce significantly more waste. The bill also incentivizes contract awards to out of state businesses who would not reinvest their earnings into the local Oregon economy.
Behind the Design of Bethany Senior Terraces, NYC’s First Modular Passive House Senior Housing Project
As more developers seek to meet new regulations for energy efficiency, the team at Murray Engineering has set a new record. With the Bethany Senior Terraces project, Murray Engineering has helped to develop NYC’s first modular structure that fully encompasses passive house principles — introducing a new era of energy efficiency in the energy-conscious city that never sleeps.
How LAMOD is Using Modular to Address Inefficiency, Sustainability, and the Future of Construction
As developers, designers, and contractors seek to understand the evolving needs of the modular industry, no one is as well-versed in the benefits of going modular as Mārcis Kreičmanis. As the co-founder and CBDO of LAMOD in Riga, Latvia, Mārcis has made it his ultimate goal to address the inefficiencies of traditional construction.
From Furniture Builder to ‘Activist Architect’: Stuart Emmons’ Unique Journey
Stuart Emmons was fascinated by buildings at a young age. He remembers building sand cities with his brother during trips to the Jersey shore. His father gave him his first drawing table at the age of ten. Today, he is an experienced architect who received his FAIA in June 2025. The road he took is unique, to say the least.
Forge Craft Architecture + Design: Codes, Contracts, and Intellectual Property
Founding Principal and Director of Modular Practice for Forge Craft Architecture + Design, Rommel Sulit, discusses the implications of codes, contracts, and intellectual property on
modular construction.
Eisa Lee, the “Bilingual” Architect
Now as the founder of XL
Architecture and Modular Design in Ontario, Canada, she applies not just her education as a traditional architect but an entire holistic view on modular design. It’s this expansive view that guides her work on being a true partner that bridges the gap between architects and modular factories as they collaborate on the design process.
Tamarack Grove Engineering: Designing for the Modular Sector
The role of a structural engineer is crucial to the success of a modular project, from initial analysis to construction administration. Tamarack Grove offers structural engineering services — project analysis, plan creation, design creation, and construction administration — for commercial, manufacturing, facilities, public services, and modular. Modular is only one market sector the company serves but it is an increasingly popular one.
Engineer Masters the Art of Listening to His Customers
Since founding Modular Structural Consultants, LLC. in 2014, Yurianto has established a steady following of modular and container-based construction clients, primarily manufacturers. His services often include providing engineering calculations, reviewing drawings, and engineering certification
Inside College Road: Engineering the Modules of One of the World’s Tallest Modular Buildings
College Road is a groundbreaking modular residential development in East Croydon, South London by offsite developer and contractor, Tide, its modular company Vision Volumetric (VV), and engineered by MJH Structural Engineers.
Design for Flow: The Overlooked Power of DfMA in Modular Construction
Unlocking higher throughput, lower costs, and fewer redesigns by aligning Lean production flow with design for manufacturing and assembly.