Poland's iQ Module is Expanding What's Possible with Modular Construction
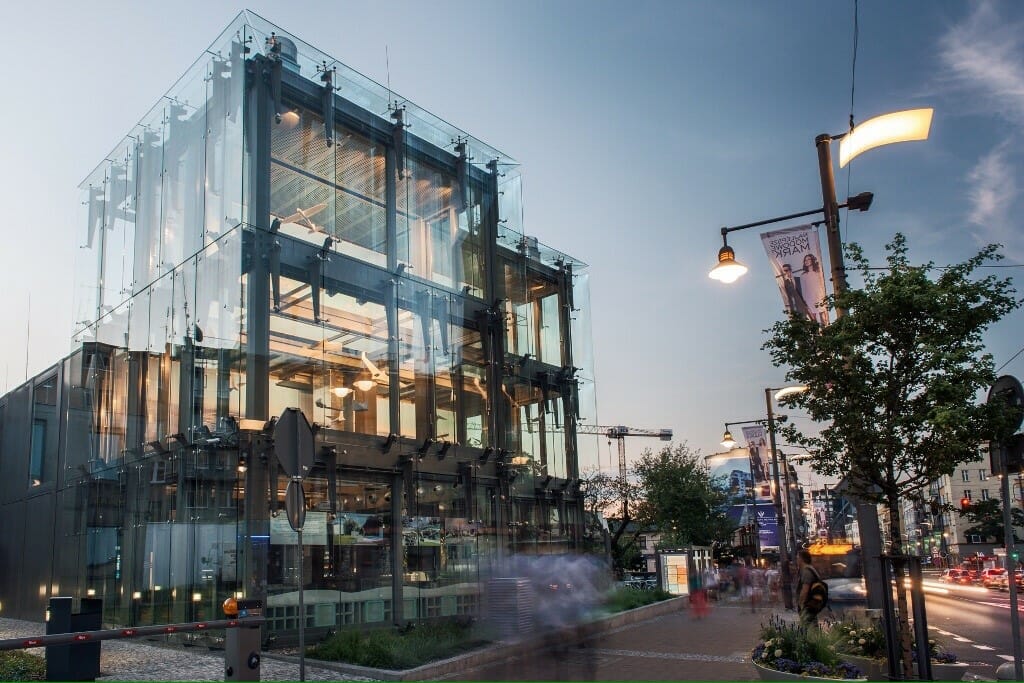
Located in Gdynia, Poland, the InfoBox—built by iQ Module— is Gdynia InfoBox is a center for information about urban developments and projects being implemented in the city. It also serves as a tourist attraction and features a 22-meter lookout tower.
The modular industry is expanding globally with considerable growth in Europe. iQ Module, headquartered in Gdansk, Poland, has contributed to that industry growth. MBI caught up with iQ Module co-founder Krzysztof Droszcz and talked to him about what iQ Module is doing and how the modular industry is growing in Europe.
MBI: What notable projects are you currently/have you recently worked on that you’d like to share?
KD: There are a few but the most significant has been InfoBox in Gdynia, Poland. This building was raised on steel frame modules using mostly glass structure facades as walls. The building itself is a city tourist Info Center with conference space, two restaurants, a few modular galleries, and a viewing tower that overlooks the city and the sea. It’s situated in the Gdynia city center and has become an iconic, well-known building..
We were the designers as well as the builders of that magnificent structure. The building itself got a few national and international awards and distinctions.
Another notable project is a single house in Sopot, Poland. It received an award for the best project in Sopot in 2019. The house represents simplicity in architecture. The whole roof and facade are made from fiber cement boards decorated with subtle wood finishing, making that project interesting to see and touch.
MBI: How has COVID-19 affected your business this year? How have you had to adapt?
KD: That’s a question we are still answering. Everything has changed and we’ve had to adapt to the new order of the world. We have recently been preparing iQ for global market expansion and we have been concentrating on the US, UK, and Germany especially. We have developed some paths to the hotel and residential market. After the COVID-19 lockdown, we were forced to diversify our production targets and modify our products.
We have also been involved in creating quarantine and isolation units. We have to produce to keep the company rolling but we’re also trying to get involved in stopping the pandemic as that’s in all of our interest to take it down. It’s a hard time but we try to use it most effectively.
MBI: What’s been the biggest benefit of being an MBI member?
We were looking for a wider view on the modular market and possibilities. Entering the US market as a member of MBI gives us much more contact with fellow modular producers, designers, and specialists so we can get involved in the global modular market. Another great thing about membership is getting to meet industry pioneers, experienced investors, and architects with whom we are happy to work. As we expand outside of Europe, we’re seeking to be a part of a global modular family. Being an MBI member is proving to be a great value for us.
MBI: Have you noticed the industry change since you became part of it? How so?
KD: Since the COVID-19 pandemic hit, the changes have been significant. We’ve seen how members of MBI have been developing new ideas to keep the industry well. The situation we are all affected by is also a time of opportunity. The trick is to use wisdom and convince more stakeholders to trust modular technology.
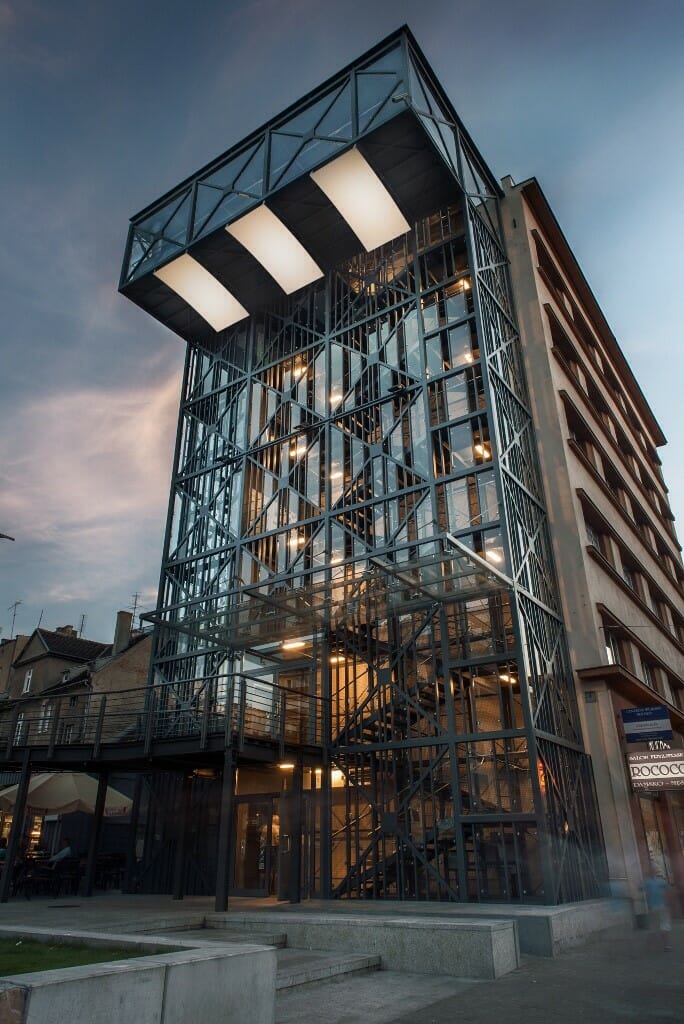
MBI: How would you describe the modular construction industry in Europe overall?
KD: There is tremendous potential for modular construction in Europe. On the one hand, there is a lot of tradition on our continent, but on the other hand, there is a huge need for new technologies.
For example, one of the most interesting markets we have experienced is in Scandinavia. Our wood modules fit in that environment perfectly and it’s eco-friendly. Norway and Sweden have a long history of building modules and wood structure buildings. That market is still developing. Steel structure modules are not as popular yet but they’re almost a necessity to use for higher structures. The market is beginning to realize that modular technology is a solution yet there is still a lot to do to encourage clients to think modular.
More from Modular Advantage
AI, Faster Sets, and Automation: The Future of Modular is at World of Modular
While the modular building industry has long known that it can be an effective solution to increase affordable housing, the word is slowly spreading to more mainstream audiences. Three presentations at this year’s World of Modular in Las Vegas hope to provide insight and direction for those seeking a real solution to the crisis.
An Insider’s Guide to the 2025 World of Modular
The Modular Building Institute is bringing its global World of Modular (WOM) event back to Las Vegas, and with it comes some of the industry’s best opportunities for networking, business development, and education. Over the course of the conference’s four days, there will be numerous opportunities for attendees to connect, learn, and leverage event resources to get the most out of the conference.
Affordable Housing Now: The Industry’s Best Bring New Solutions to World of Modular
While the modular building industry has long known that it can be an effective solution to increase affordable housing, the word is slowly spreading to more mainstream audiences. Three presentations at this year’s World of Modular in Las Vegas hope to provide insight and direction for those seeking a real solution to the crisis.
Opportunities for Innovation in Modular Offsite Construction
Modular Offsite Construction has already shattered the myth that it only produces uninspired, box-like designs. Architectural innovations in module geometry, configurations, materials, and products make it possible to create visually stunning buildings without sacrificing functionality or efficiency.
Safe Modular Construction with Aerofilm Air Caster Transport
In collaboration with Aerofilm Systems, Heijmans developed innovative skids using air caster technology for moving modules easily and safely. These pallets are equipped with an auto-flow system, making operation extremely simple.
Miles, Modules, and Memes: Building a Modular Network One Flight at a Time
At the end of the day, social media is just another tool for building connections, and like any other tool, needs to be used skillfully to work properly. Use social media thoughtfully, and it will open doors to real opportunities and relationships you didn’t even see coming.
Falcon Structures: Thinking Inside the Box
Some of Falcon’s latest projects include creating container solutions for New York’s Central Park and an East Coast professional baseball team. More and more, Falcon is shipping out container bathrooms and locker rooms to improve traditionally difficult work environments, like those in oil and gas or construction.
UrbanBloc—From Passion to Industry Leader
UrbanBloc specializes in three main categories or markets – what they call “Phase 0” projects, amenities, and urban infill. Clients are often attracted to shipping containers because from a real estate perspective they are considered an asset. Having the flexibility to move and transport these assets allows owners to respond to different circumstances in a fluid manner that they can’t get with standard construction.
The Hospitality Game-Changer
“Hospitality is about more than just providing a service – it’s about delivering an experience,” says Anthony Halsch, CEO of ROXBOX. “And that’s where containers thrive. They allow us to create spaces that are unique, efficient, and sustainable.”
Container Conversions Counts on Simplicity to Provide Critical Solutions
Container Conversions has fabricated and developed thousands of containers for varied projects, including rental refrigeration options, offices, kitchens, temporary workplace housing, and mobile health clinics.