Making the Leap: From Traditional General Contractor to Modular Builder
The Modular Building Institute estimates there are about 250 modular manufacturers in North America accounting for slightly more than three percent of all new commercial construction starts. With the construction industry gaining momentum, traditional general contractors (GCs) are not finding the labor needed to meet demand.
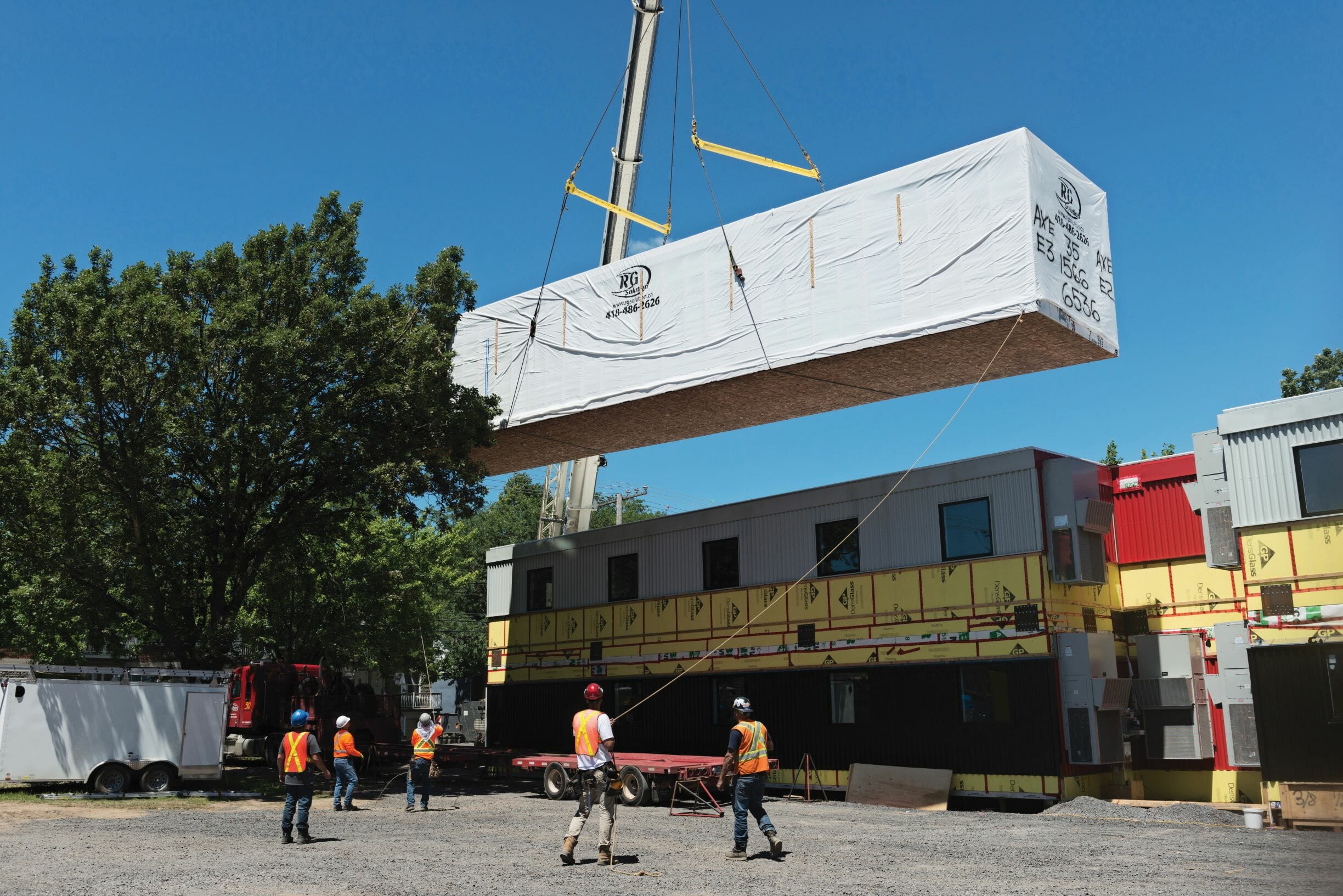
That’s one reason we are seeing more traditional contractors making the leap and turning to modular construction. In some cases, GCs are contracting with modular manufacturers on “hybrid” projects that incorporate the best of modular and site-built processes. In other cases, contractors are establishing their own prefab divisions as a hedge against this labor shortage.
PCL Construction, one of the largest general contractors in North America, created its “Agile” division about three years ago to move into the modular construction industry. MBI wanted to find out what drove PCL to this decision.
According to Terry Olynyk, Director of Business Development for PCL Construction, “The world of construction is rapidly moving towards the digital age and with that [so is] industrialized construction. PCL did not want to stay on the sidelines while this paradigm shift is occurring and wanted to lead the market by being the first fully integrated general contractor with its own modular factory.”
PCL’s strategy when approaching a project is to first ask how much of the project can be built offsite. “Our end goal is to target scopes that reduce the project critical path and gain us valuable time,” Olynyk said. He continued, “Another consideration is the complexity of the scope and challenges we have with hours of work, work location, available sub-trades to perform the work, geographical area. We then assess these constraints against our ability to ship the volumetric spaces and the associated costs. With advanced digital tools combined virtual models we are getting better at decoupling spaces and finding advantages with modular.” Anthony Zarilli’s transition took place more than 15 years ago while building homes in New Jersey. According to Zarrilli, he knew modular home building had the potential to change the future of new home construction when he first started researching it.
It all started when Zarrilli, while working alongside his father constructing custom “stick-built” houses, saw an article about modular homes which piqued his interest. After visiting several modular plants and receiving approval to build, he ordered his first modular home. Zarrilli set the home in Point Pleasant, New Jersey by himself, and because his real estate agent wasn’t quite sure how to market a modular home, he decided to sell it himself.
Once the home sold, Zarrilli repeated the process, but this time in Point Pleasant Beach. While working on that project, people started to take notice. Before he knew it, Zarrilli was being asked to build modular homes for others.
“I went from building four homes per year to eight to 12 and it just kept on growing from there,” he said. “That’s really how it all started.” Today, Zarrilli Homes is expanding into new markets such as multifamily.
Making the move to modular construction is not without some challenges. Every aspect of the construction industry is considered from the perspective that the materials and labor show up on a specific site and work begins there. Moving construction to an offsite location requires greater coordination and communication among all parties. Everything from insurance to legal consideration to payment schedules need to be discussed and agreed upon in in advance.
Related Listening:
How Owner/Developers Can Best Get Started with Modular Construction w/ R & S Tavares Associates
In this episode of MBI's Inside Modular podcast, Pedro Tavares and Anthony Gude of R & S Tavares Associates share best practices for owner/developers looking to incorporate modular construction into their upcoming projects.
MBI is actively working with other organizations to address many of these site related barriers, including providing more resources in the building codes, a design guideline for architects, and a standard contractual language between general contractors and modular manufacturers.
But for many contractors, it’s simply a matter of time before this process is mainstream. Olynyk sums it up this way, “design tools and materials have greatly advanced over the past 20 years. The construction industry has been building the same for over 100 years and is about to change. A significant skilled labor decline has started in North America coupled with the rising cost of labor and productivity falling. The construction industry will soon be forced to look at alternatives that will keep the projects on track. We will soon realize a cost shift where onsite “stick-built” becomes more expensive than modular construction. Lack of construction labor, quality concerns, and project certainty with modular solutions will force the construction industry into a long overdue change.”
Other Contractors Making the Leap
Chicago-based Skender recently announced plans to open a new Skender Manufacturing facility that will assemble modular building parts for senior housing, multifamily, healthcare, and other commercial buildings in the Windy City. Manufacturing will begin as soon as this November.
Baltimore-based general contractor Whiting-Turner has a history of delivering successful modular projects including student housing and hotels. The company touts “prefab and modular” as part of their corporate expertise now. According to their website, “Prefabrication of building systems and components is made possible by the accuracy of the digital submission process. This saves costly rework; reduces waste, installation time and onsite labor; and significantly enhances quality and safety.”
This article originally appeared in the Modular Advantage Magazine - Fourth Quarter 2018 released in November 2018.
More from Modular Advantage
Oregon’s Prevailing Wage Proposal: A Wake-Up Call for Modular Construction
In early February, 2024, the Massachusetts Board of Building Regulations and Standards (BBRS) released its proposed 10th Edition building codes. This draft included several amendments targeting modular construction that would have created an extremely difficult environment for the entire modular industry and could have eliminated the industry entirely in the state.
Behind the Design of Bethany Senior Terraces, NYC’s First Modular Passive House Senior Housing Project
As more developers seek to meet new regulations for energy efficiency, the team at Murray Engineering has set a new record. With the Bethany Senior Terraces project, Murray Engineering has helped to develop NYC’s first modular structure that fully encompasses passive house principles — introducing a new era of energy efficiency in the energy-conscious city that never sleeps.
How LAMOD is Using Modular to Address Inefficiency, Sustainability, and the Future of Construction
As developers, designers, and contractors seek to understand the evolving needs of the modular industry, no one is as well-versed in the benefits of going modular as Mārcis Kreičmanis. As the co-founder and CBDO of LAMOD in Riga, Latvia, Mārcis has made it his ultimate goal to address the inefficiencies of traditional construction.
From Furniture Builder to ‘Activist Architect’: Stuart Emmons’ Unique Journey
Stuart Emmons was fascinated by buildings at a young age. He remembers building sand cities with his brother during trips to the Jersey shore. His father gave him his first drawing table at the age of ten. Today, he is an experienced architect who received his FAIA in June 2025. The road he took is unique, to say the least.
Forge Craft Architecture + Design: Codes, Contracts, and Intellectual Property
Founding Principal and Director of Modular Practice for Forge Craft Architecture + Design, Rommel Sulit, discusses the implications of codes, contracts, and intellectual property on
modular construction.
Eisa Lee, the “Bilingual” Architect
Now as the founder of XL
Architecture and Modular Design in Ontario, Canada, she applies not just her education as a traditional architect but an entire holistic view on modular design. It’s this expansive view that guides her work on being a true partner that bridges the gap between architects and modular factories as they collaborate on the design process.
Tamarack Grove Engineering: Designing for the Modular Sector
The role of a structural engineer is crucial to the success of a modular project, from initial analysis to construction administration. Tamarack Grove offers structural engineering services — project analysis, plan creation, design creation, and construction administration — for commercial, manufacturing, facilities, public services, and modular. Modular is only one market sector the company serves but it is an increasingly popular one.
Engineer Masters the Art of Listening to His Customers
Since founding Modular Structural Consultants, LLC. in 2014, Yurianto has established a steady following of modular and container-based construction clients, primarily manufacturers. His services often include providing engineering calculations, reviewing drawings, and engineering certification
Inside College Road: Engineering the Modules of One of the World’s Tallest Modular Buildings
College Road is a groundbreaking modular residential development in East Croydon, South London by offsite developer and contractor, Tide, its modular company Vision Volumetric (VV), and engineered by MJH Structural Engineers.
Design for Flow: The Overlooked Power of DfMA in Modular Construction
Unlocking higher throughput, lower costs, and fewer redesigns by aligning Lean production flow with design for manufacturing and assembly.