What is an Air Balance? The Comfort Zone
An "air balance" is a useful process for measuring the performance of a simple or complex hvac system, and for providing the occupants with a comfortably conditioned space. To understand how this process works, let's first look at the different types of air balance by defining the two extremes: Comfort Balance and AABC Certified Air Balance.
A "comfort balance" is simply checking to see whether the room feels comfortably conditioned. It may be as easy as walking from room to room, holding a hand up to the ceiling to see if sufficient air is coming out of the registers, and asking the occupants if they are comfortable. If they are not, your journey starts to discover how to resolve the HVAC problems associated with the situation. It may involve adjusting/moving registers, installing restrictors/dampers after the fact, or just insuring the air doesn't blow directly on an occupant. Many occupant complaints are associated with air circulation: too much and too little.
At the other end of the spectrum is the AABC Certified Air Balance. The purpose of this type is to insure all components of the hvac (heating, ventilating, air conditioning) system are working in harmony, at their optimum performance, providing total occupant comfort. While the journey toward a certified air balance starts before the testing stage, let's begin ours with the mechanical engineer.
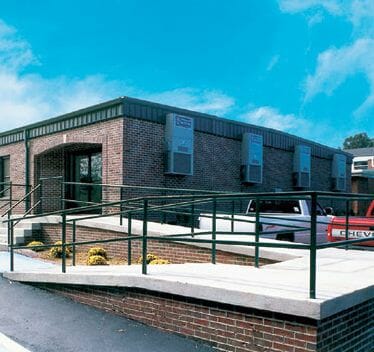
A mechanical engineer develops specifications and a set of mechanical drawings from a mix of occupant desires, local codes, ASHRAE standards, and many years of training. The correct ducting, airflow, registers, and unit performance are brought together with consideration for ventilation requirements and building exhaust needs.
The most important part of the mechanical plans used by the certified balance company is the list of "cfm" requirements next to each supply, return, intake, exhaust and ventilation opening. Without this important information a certified balance is not possible.
To conduct an AABC Certified Air Balance, the building must first be totally sealed/enclosed. Therefore this process would fall under the modular dealer's scope of work. If your project is complex, or your customer includes a certified air balance in the bid specs, be sure to include the following cost allowances on the front end:
- A mechanical engineer
- A system with products capable of a certified balance
- The cost for a balancing company
- An HVAC contractor on site during balance.
The HVAC contractor is advisable because, according to their association, a true AABC certified balance contractor must not be affiliated with any mechanical contractors, design engineers, or equipment manufacturers. So if the HVAC unit needs service during the air balance process, and an HVAC contractor is not on site, the balance will most likely stop.
A total air balance requires an opposed blade damper (OBD) behind the face of each intake and exhaust opening in each room and of the building. Other balancing dampers are required at all branch locations of the duct system.
At the building site prior to occupation, the certified balance technician will change all of the filters in the system, and insure that all dampers are fully open. Readings are taken at every opening inside, on the roof, etc. Slowly the dampers are closed in an effort to meet the cfm requirements set by the mechanical engineer. Adjusting one damper changes the cfm at all other openings. The air balance technician returns to every opening, making new adjustments and readings based on the changes from the previous one. Registers, grills, exhaust fans, and fresh air must all "balance" to meet the system performance requirements.
After the technician believes the system is all in tune, he locks down all of the dampers and other devices, so that the settings will not change. While this should keep the system "balanced," the system can be thrown out of balance by such things as dirty filters, the occupants changing the register setting, office remodeling, and reconfiguring registers and ducting.
The cost to do an AABC Certified Air Balance ranges from $75-150 per opening. You're paying for time, labor, expertise, equipment, and a Certified Balance Report. A building with five supply openings, five return openings, one exhaust fan, and one OSA intake has 12 openings to verify. Depending on the complexity and location of the openings, you can expect to pay $900-$2,000 for an AABC Certified Balance.
Is it worth it on large projects? Definitely. Remember, to avoid wasting money on your balance, be sure to install registers that the occupants cannot adjust.
Hiring a good air balance company with skillful technicians is also important. Visit www.aabchq.com for more information on the Associated Air Balance Council and a member list. The website also lists the requirements for membership, the types of certified technicians, their code of ethics, and their performance guarantee.
We have looked at the simple and the perfect air balance types, just hitting the high spots toward explaining certified air balance requirements and results. This understanding may help you avoid the temptation to put only $50 in your bid when you see your customer specifications requiring an AABC Certified Air Balance. The $50 only covers the cost of the "waving the hand" comfort balance.
More from Modular Advantage
AI, Faster Sets, and Automation: The Future of Modular is at World of Modular
While the modular building industry has long known that it can be an effective solution to increase affordable housing, the word is slowly spreading to more mainstream audiences. Three presentations at this year’s World of Modular in Las Vegas hope to provide insight and direction for those seeking a real solution to the crisis.
An Insider’s Guide to the 2025 World of Modular
The Modular Building Institute is bringing its global World of Modular (WOM) event back to Las Vegas, and with it comes some of the industry’s best opportunities for networking, business development, and education. Over the course of the conference’s four days, there will be numerous opportunities for attendees to connect, learn, and leverage event resources to get the most out of the conference.
Affordable Housing Now: The Industry’s Best Bring New Solutions to World of Modular
While the modular building industry has long known that it can be an effective solution to increase affordable housing, the word is slowly spreading to more mainstream audiences. Three presentations at this year’s World of Modular in Las Vegas hope to provide insight and direction for those seeking a real solution to the crisis.
Opportunities for Innovation in Modular Offsite Construction
Modular Offsite Construction has already shattered the myth that it only produces uninspired, box-like designs. Architectural innovations in module geometry, configurations, materials, and products make it possible to create visually stunning buildings without sacrificing functionality or efficiency.
Safe Modular Construction with Aerofilm Air Caster Transport
In collaboration with Aerofilm Systems, Heijmans developed innovative skids using air caster technology for moving modules easily and safely. These pallets are equipped with an auto-flow system, making operation extremely simple.
Miles, Modules, and Memes: Building a Modular Network One Flight at a Time
At the end of the day, social media is just another tool for building connections, and like any other tool, needs to be used skillfully to work properly. Use social media thoughtfully, and it will open doors to real opportunities and relationships you didn’t even see coming.
Falcon Structures: Thinking Inside the Box
Some of Falcon’s latest projects include creating container solutions for New York’s Central Park and an East Coast professional baseball team. More and more, Falcon is shipping out container bathrooms and locker rooms to improve traditionally difficult work environments, like those in oil and gas or construction.
UrbanBloc—From Passion to Industry Leader
UrbanBloc specializes in three main categories or markets – what they call “Phase 0” projects, amenities, and urban infill. Clients are often attracted to shipping containers because from a real estate perspective they are considered an asset. Having the flexibility to move and transport these assets allows owners to respond to different circumstances in a fluid manner that they can’t get with standard construction.
The Hospitality Game-Changer
“Hospitality is about more than just providing a service – it’s about delivering an experience,” says Anthony Halsch, CEO of ROXBOX. “And that’s where containers thrive. They allow us to create spaces that are unique, efficient, and sustainable.”
Container Conversions Counts on Simplicity to Provide Critical Solutions
Container Conversions has fabricated and developed thousands of containers for varied projects, including rental refrigeration options, offices, kitchens, temporary workplace housing, and mobile health clinics.