What is Modular Construction?
Modular construction is a process in which a building is constructed off-site, under controlled plant conditions, using the same materials and designing to the same codes and standards as conventionally built facilities – but in about half the time. Buildings are produced in “modules” that when put together on site, reflect the identical design intent and specifications of the most sophisticated site-built facility – without compromise.
The factory-controlled process generates less waste, creates fewer site disturbances and allows for tighter construction.
Greater Flexibility and Reuse: Modular buildings can be disassembled and the modules relocated or refurbished for new use, reducing the demand for raw materials and minimizing the amount of energy expended to create a building to meet the new need.
Less Material Waste: When building in a factory, waste is eliminated by recycling materials, controlling inventory and protecting building materials.
Improved Air Quality: Because the modular structure is substantially completed in a factory-controlled setting using dry materials, the potential for high levels of moisture being trapped in the new construction is eliminated.
Download MBI's report: The Sustainability of Modular Construction
Faster.
Construction of modular buildings occurs simultaneously with site work, allowing projects to be completed in half the time of traditional construction.
Reduced Construction Schedule:
Because construction of modular buildings can occur simultaneously with the site and foundation work, projects can be completed 30% to 50% sooner than traditional construction.
Elimination of Weather Delays:
60 - 90% of the construction is completed inside a factory, which mitigates the risk of weather delays. Buildings are occupied sooner, creating a faster return on investment.
Built to Code with Quality Materials:
Modular buildings are built to meet or exceed the same building codes and standards as site-built structures, and the same architect-specified materials used in conventionally constructed buildings are used in modular construction projects – wood, concrete and steel.
Smarter.
Modular buildings are built with the
same materials and to the same building codes and architectural specifications as traditional construction. Once assembled, they are virtually indistinguishable from their site-built counterparts.
Safer Construction:
The indoor construction environment reduces the risks of accidents and related liabilities for workers.
Better Engineered Building & BIM:
PMC relies on advanced BIM for visualization to assess the energy performance and identify the most cost-effective efficiency measures. PMC is ideal for the use of this technology where the construction process is already a collaboration of systems, materials and people—much like the software itself.
Limitless Design Opportunities:
Modular units may be designed to fit in with external aesthetics of any existing building and modular units, once assembled, are virtually indistinguishable from their site-built counterparts.
Discover the Benefits of Modular Construction: Why Not Build Modular?
Structurally, modular buildings are generally stronger than site-built construction because each module is engineered to independently withstand the rigors of transportation and craning onto foundations. Once together and sealed, the modules become one integrated wall, floor, and roof assembly. Explore what modular construction options. Building offsite ensures better construction quality management. Manufacturing plants have stringent QA/QC programs with independent inspection and testing protocols that promote superior quality of construction every step of the way.
Beyond quality management and improved completion time, modular construction offers numerous other benefits to owners. Removing approximately 80% of the building construction activity from the site location significantly reduces site disruption, vehicular traffic, and improves overall safety and security. Highly active businesses such as those in the education and healthcare markets have need for reduced on-site activity and offsite construction eliminates a large part of ongoing construction hazards, ensuring a tremendous advantage when building new projects.
For architects, developers, and owners alike, modular construction companies today can work with levels of design and construction sophistication that will exceed all expectations, rivaling their site-built counterparts. It is beneficial that when exploring the various project delivery methods, offsite construction is chosen early in the design development process, and the project built around that methodology, to avoid redesigning. Most modular companies, however, can take a site-built design and create a modular version when required, so it’s never too late to explore the possibilities!
As owners and designers explore the benefits of Modular Contruction and look for more sustainable designs for improved environmental impact, modular construction is inherently a natural fit. Building in a controlled environment reduces waste through avoidance upstream rather than diversion downstream. This, along with improved quality management throughout the construction process and significantly less on-site activity and disturbance, inherently promotes sustainability. High quality, sustainable, innovative, efficient, cost-effective, and shorter time to completion.
What is Modular Construction: Exploring the Two Types of Modular Construction
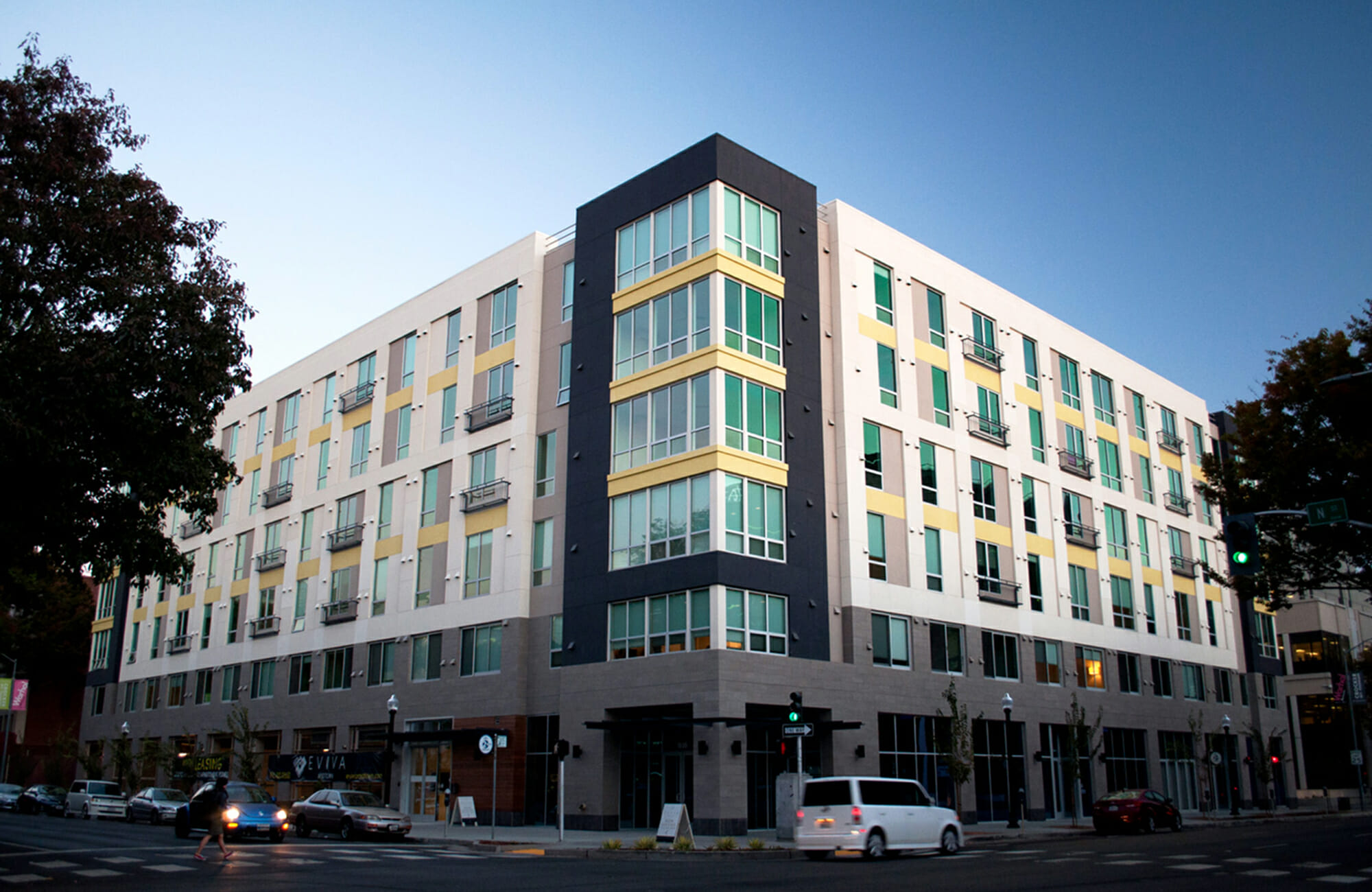
Permanent Modular Construction
Permanent Modular Construction (PMC) is an innovative, sustainable construction delivery method utilizing offsite, lean manufacturing techniques to prefabricate single or multi-story whole building solutions in deliverable module sections. PMC modules can be integrated into site built projects or stand alone as a turn-key solution and can be delivered with MEP, fixtures and interior finishes in less time -- with less waste, and higher quality control compared to projects utilizing only site-built construction. Recent research has come out supporting the fact that modular construction is an efficient construction process and poised to help the construction industry grow.
“Manufacturing building components off-site provides for more controlled conditions and allows for improved quality and precision in the fabrication of the component.” - National Institute of Standards and Technology and the National Research Council
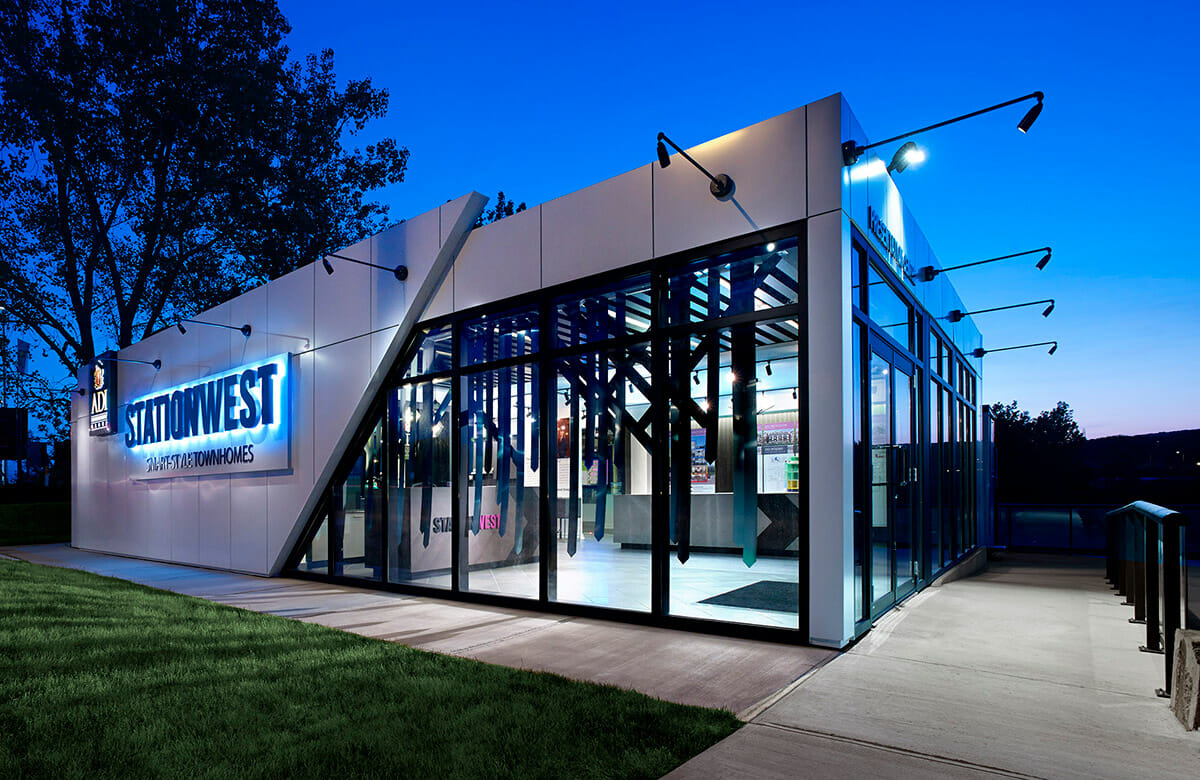
Relocatable Buildings
A Relocatable Building (RB) is a partially or completely assembled building that complies with applicable codes or state regulations and is constructed in a building manufacturing facility using a modular construction process. Relocatable buildings are designed to be reused or repurposed multiple times and transported to different building sites. They are utilized for schools, construction site offices, medical clinics, sales centers, and in any application where a relocatable building can meet a temporary space need. These buildings offer fast delivery, ease of relocation, low-cost reconfiguration, accelerated depreciation schedules and enormous flexibility. Relocatable buildings are not permanently affixed to real estate but are installed in accordance with manufacturer’s installation guidelines and local code requirements. These buildings are essential in cases where speed, temporary space, and the ability to relocate are necessary.
Explore Modular Building Case Studies
Hawthorn Extended Stay by Wyndham—Jackson, WY
The plan was to build the project in two phases. This would enable the property to open sooner and start
accommodating guests while completing the second phase. The digital twin was designed to provide a complete factory-ready model for both phases upfront. That gave the factory everything it needed to bring each phase into production quickly. It also enabled everyone a way to plan both
phases ahead of time, and begin prepping the site in advance.
102-108 Westford Street
102-108 Westford was an opportunity for New England-based GreenStaxx to show how project costs could be trimmed by using a standardized, modular-ready Triple Decker design.
Geberit In-Wall Systems Makes a New Breed Luxury Room Concept a Reality for International Hotel Brand
Geberit in-wall flush toilet systems for wall-hung toilets are the classics for modern bathroom design. citizenM has specified the Geberit systems into their bathroom walls worldwide as a basis of their bathroom design. This installation is part of the over one million times building owners have installed Geberit systems in their buildings around the globe for over the past 50 years.
Panel Built Provides Custom Modular Enclosure for Major Beverage Manufacturer
The challenge was twofold. Firstly, Panel Built needed to create a spacious enclosure that could accommodate a large facility crane. This enclosure required a design that provided ample storage space and integrated seamlessly with the existing infrastructure. Secondly, the structure needed to incorporate office space that offered personnel an unimpeded, 360-degree view of the factory floor.
Fire Station 67
Fire Station 67 is designed in direct response to the climate crisis, the increasing threat of wildfires, and the needs to the Rancho Mission Viejo community. Prefabricated off-site and assembled from 10 modules, the 4,667-square-foot fire station is a modular design with the ability to reconfigure the structure into something new in the future.
Maceo May
Maceo May is a six-story, all-electric modular construction, affordable housing development located on Treasure Island in San Francisco Bay. The climate-responsive design provides 104 homes for formerly homeless veterans and their families with a strong focus on decarbonization, resilience and wellness. The apartment building offers 1 on-site manager’s unit, and a mix of 24 studio, 47 one-bedroom and 34 two-bedroom units.
The Sphere Made Possible with Exterior Wall Panels
This one-of-a-kind structure required one-of-a-kind building materials and exterior cladding that could accommodate the atypical geometries, project timelines, and significant daily foot traffic. Offsite construction, in the form of Dryvit’s Outsulite prefabricated panels of continuous insulation (CI), was the key method for streamlining the façade installation and ensuring quality control for the difficult building connections.
Modular Construction for Financial Viability: The Norwalk Project Case Study
The Norwalk project serves as a prime example of how Offsite Modular Construction, in collaboration with Architects, Consultants/Engineers, General Contractors (GC), and Mechanical, Electrical, Plumbing, and Fire Protection (MEP/FP) Subcontractors, can make projects financially feasible by closely working with the Owner/Developer under an Integrated Project Delivery (IPD) approach.
STAAT MOD Patient Bed Expansion at M Health Fairview – St. John’s Hospital
Construction firm The Boldt Company, and interdisciplinary design firm, HGA were engaged by St. John’s Hospital to deliver a 16-bed ICU patient observation wing onto the existing facility, built to over 90 percent completion offsite in Appleton, Wisc., then seamlessly transported and installed on the St. John’s campus – the first of its kind in the state of Minnesota.
Offsite Modular Construction Builds and Installs 12 New Classrooms for Westlake Academy in 100 Days
OMC utilized modular construction techniques to manufacture two brand new permanent 6,400-square-foot modular buildings, each housing six classrooms. The process included innovative design features for safety, durability, environmental sustainability, integrated technology enhancements, and health-oriented construction.
Formula 1 Race, Las Vegas, Nevada
In partnership with InProduction, Phoenix Modular Elevator (PME) designed, manufactured, and installed seven modular elevators for the F1 Grand Prix race in Las Vegas, Nevada. To minimize space, the design utilized machine roomless (MRL) hydraulic elevators, eliminating the need for separate machine rooms for each elevator. Instead, using the MRL design, the machine room equipment is built into the hoistway, and accessed via a small door on the side.
Silverking Student Housing, Selkirk College
ROC Modular was proud to deliver a much-needed new permanent modular Student Housing Residence for Selkirk College, located at the Silverking Campus in Nelson BC. The project is a 3-storey, 12-module 38-student bed building with a mass-timber main common area for student amenities.
Parkhurst Elementary School Classroom Additions
The Parkhurst Elementary School in Winchester, MA, has recently undergone an expansion of 13,074 square feet. Due to renovations at the neighboring Lynch School, students were temporarily relocated to Parkhurst. Modular construction was chosen as the preferred method to accommodate the influx of students and prepare for the start of the 2023-2024 school year.
VBC Chooses MAESTRO SMART 9 HP
Volumetric Building Companies (VBC), a global leader in the construction sector with a focus on building the future through volumetric modular techniques, choose the Maestro Smart 9 Heat Pump as their ideal comfort solution to heat and cool their modular housing project in Philadelphia, PA, consisting of 60 modular housing units.
16’ x 37’ Welded Substation Enclosure
Instead of sourcing a new transformer, which would have taken over 100 weeks and cost several million dollars, Raytheon Technologies turned to Panel Built Inc. for a modular solution. Panel Built designed a 16’ x 37’ prefabricated enclosure that could be delivered to Guam in two pieces. Once it was put together, it was lowered over the transformer.
Temporary Visitors Center at Antietam National Battlefield Park
Antietam National Battlefield Park, a revered site listed on the U.S. National Register of Historic Places, presented unique challenges demanding meticulous preservation efforts. The paramount goal was to ensure minimal disruption to the sacred grounds surrounding the new modular building.
Wraptite Airtightness Protection for Northampton School for Boys
The Wraptite external air barrier system from the A. Proctor Group has been chosen for its high-performance, airtight insulation for a Department for Education (DfE) funded project of the offsite construction of Northampton School for Boys Multi-Academy Trust.
University Temporary Modular Student Housing— Ettrick, VA
Modular Genius, Inc. designed and built three temporary modular dormitory complexes featuring 134 dorm rooms, totaling 49,632 sq. ft. All three modular dorms feature a shared laundry room, kitchen and lounge area, showers, and restrooms for residents.
Hage’s Badehotel — Case Study — Denmark
For this project, Forta PRO delivered 72 buildings, 144 modules, with 5,200 m2 of gross modular area. With final onsite completion in June 2023, it provides exceptional long-stay accommodation in a stunning and serene environment.
355 Sango Court Case Study
The logic-intensive preconstruction method demanded of automated modular brought extra benefits to the Sango Court project. Autovol had worked side by side with preconstruction innovator Prefab Logic to create a digital twin modeling approach and a sprint process as advanced as the Autovol factory.